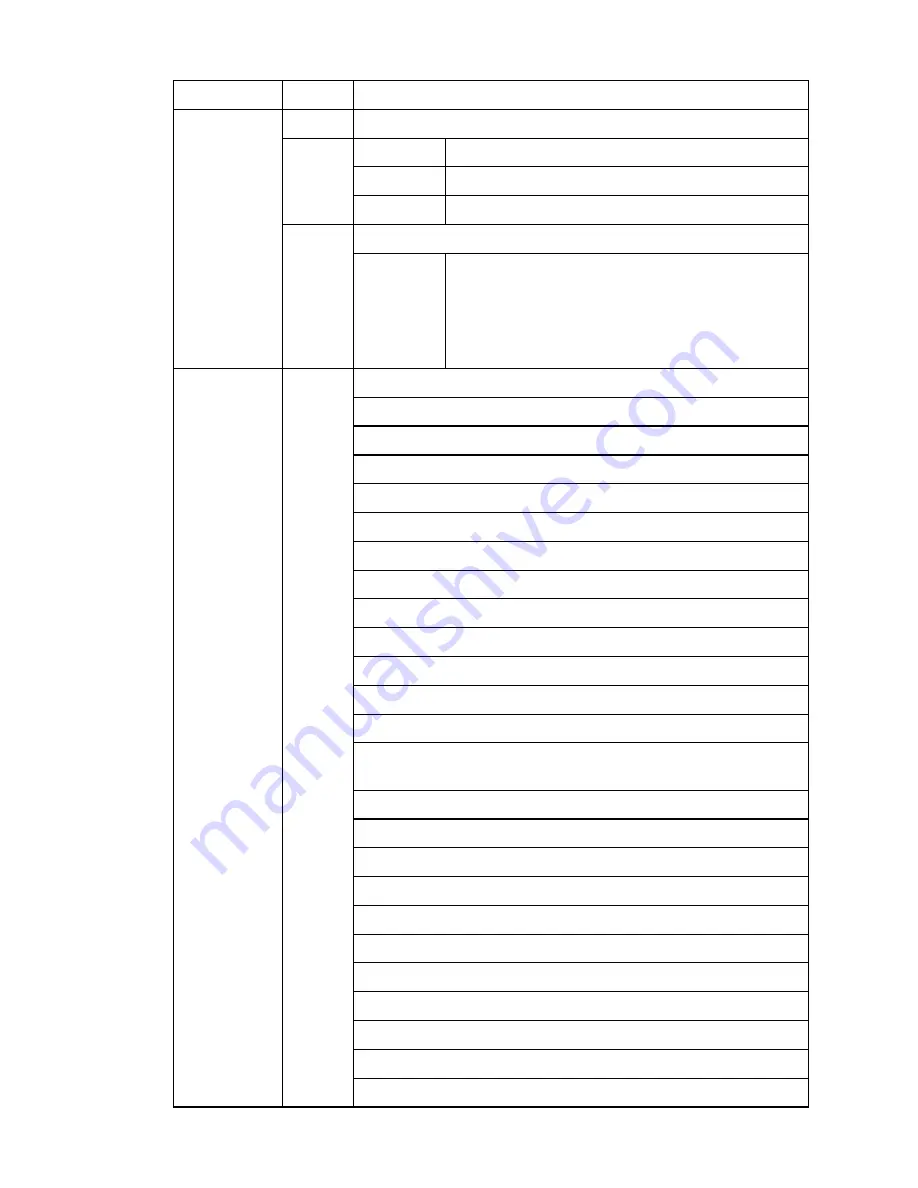
Chapter 5 Parameters
|
VFD-M-D Series
5-82
Revision Jan. 2007, MDE2, SW V1.05
Content Address
Function
2001H
Reserved
Bit 0
1: EF (external fault) on
Bit 1
1: Reset
2002H
Bit 2
Reserved
Multi-function Input Terminals (COM1~COM4)
Bit 0
COM1
Bit 1
COM2
Bit 2
COM3
Command
Write only
2006H
Bit 3
COM4
Error code:
00: No error occurred
Status monitor
Read only
2100H
01: Over-current (oc)
02:
Over-voltage
(ov)
03:
Overheat
(oH)
04:
Overload
(oL)
05:
Overload1
(oL1)
06: External fault (EF)
07:
Reserved
08: CPU failure (cF3.3~cF3.8)
09: Hardware protection failure (HPF.1~HPF.4)
10: Current exceeds 2 times rated current during accel (ocA)
11: Current exceeds 2 times rated current during decel (ocd)
12: Current exceeds 2 times rated current during steady state
operation (ocn)
13: Ground Fault (GFF)
14:
Reserved
15: CPU failure 1 (cF1)
16: CPU failure 2 (cF2)
17:
Reserved
18:
Overload
(oL2)
19:
Reserved
20: Software/password protection (PcdE/Ccde)
21:
Reserved
22:
Reserved
23:
Reserved
Summary of Contents for VFD-M-D series
Page 1: ...M D...
Page 2: ......
Page 3: ...M D...
Page 9: ...C 2 General Precaution C 4 C 3 How to Choose a Suitable Motor C 5...