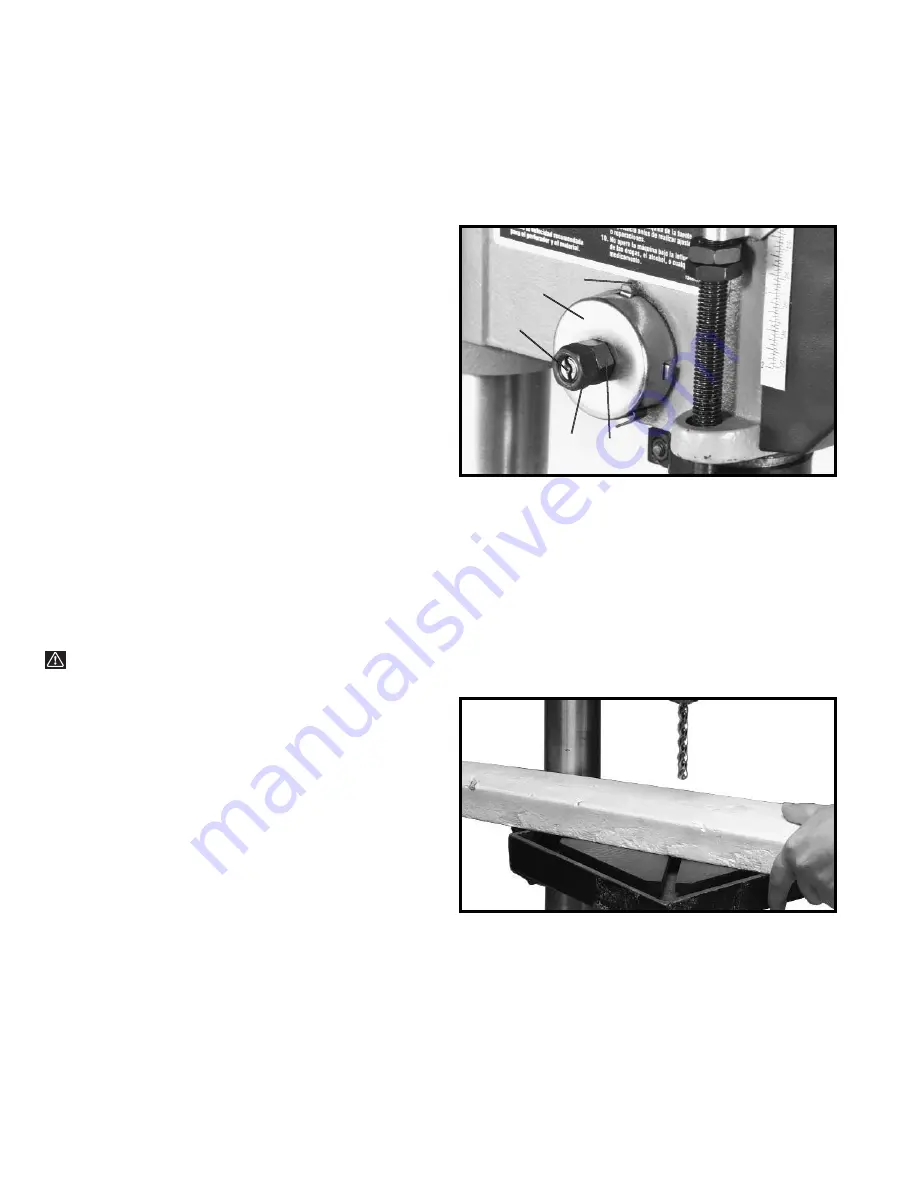
12
ADJUSTING SPINDLE
RETURN SPRING
The spindle is automatically returned to its upper most
position when the handle is released. It is recommended
that the handle be allowed to slowly return to the top
position after each hole has been drilled in the material.
This spring has been properly adjusted at the factory
and should not be disturbed unless absolutely
necessary. To adjust the return spring, proceed as
follows:
1.
DISCONNECT MACHINE FROM POWER SOURCE.
2.
Loosen nuts (B) and (E) Fig. 24. Make sure spring
housing (A) stays engaged with head casting.
3.
While
FIRMLY HOLDING
spring housing (A) Fig. 24
pull out housing and rotate it until boss (D) is engaged
with the next notch on the housing. Turn the housing
counterclockwise to increase or clockwise to decrease
spring tension. Turn nut (E) until it contacts spring
housing (A), then back nut (E) out a 1/4 turn. Tighten nut
(B) against nut (E), to hold the housing in place.
IMPORTANT: Inside nut (E) should not contact spring
housing (A) when tightened.
Fig. 24
D
A
C
E
B
OPERATION
Your drill press is to be used with drill bits with a shank of 1/2" or less in diameter. The following will give the inexperienced
operator a start on common drill press operations. Use scrap material for practice to get a feel of the machine before
attempting regular work.
WARNING: The use of accessories and attachments not recommended by Delta may result in risk of injury.
IMPORTANT:
When the workpiece is long enough it
should always be positioned on the table with one end
against the left side of the column, as shown in Fig. 25.
This prevents the workpiece from rotating with the drill
bit or cutting tool, causing damage to the workpiece or
personal injury to the operator. If it is not possible to
support the workpiece against the column, the
workpiece should always be fastened to the table using
clamps or a vise.
Fig. 25
Summary of Contents for ShopMaster DP115
Page 15: ...15 NOTES ...
Page 16: ...16 NOTES ...