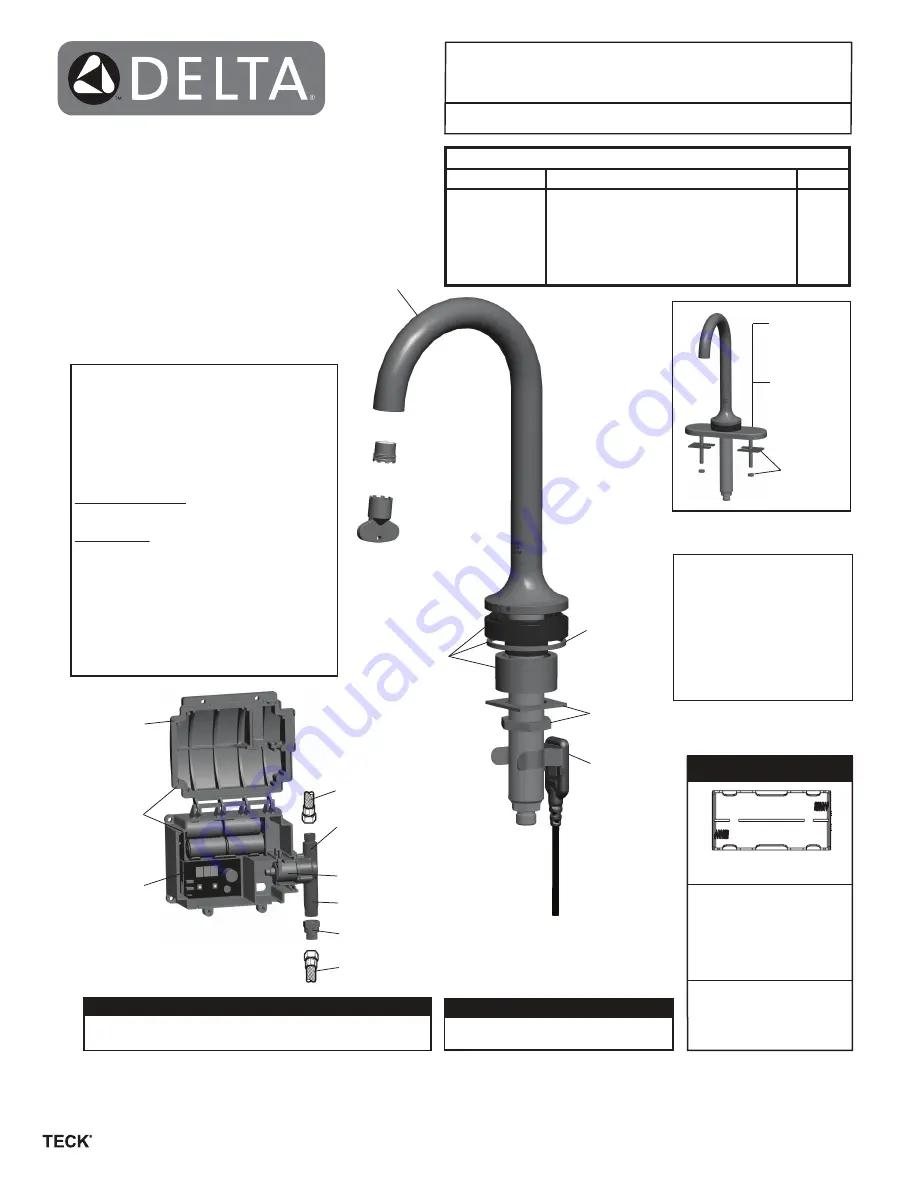
063222A / 063222SS / 063222BL
Proximity Gooseneck Spout Assembly
0.5 GPM (1.9 L/min)
063226A / 063226SS / 063226BL
Proximity Gooseneck Spout Assembly
1.0 GPM (3.8 L/min)
063227A / 063227SS / 063227BL
Proximity Gooseneck Spout Assembly
1.5 GPM (5.7 L/min)
063229A / 063229SS / 063229BL
Proximity Gooseneck Spout Assembly
2.2 GPM (8.3 L/min)
RP6087
Nut & Washer
061206A
Proximity
Sensor Module
Page 1
209989 Rev. B
62__TP3__ __ __
Write purchase model number here for future reference
PLEASE LEAVE this M&I Sheet with the owner, maintenance plumber, etc. as
items relating to ongoing maintenance suggestions and procedures are included.
060683A
24VAC to 6VDC Converter
061259A
Ground Wire Kit
(for hardwire models)
061047A
24VAC to 6VDC Converter with
Battery Backup
061256A
36” Sensor Module Extension Cable
061266A
Laminar Outlet (3/pkg, 1 key)
0.5 GPM (1.9 L/min)
061267A
Laminar Outlet (3/pkg, 1 key)
1.0 GPM (3.8 L/min)
061268A
Laminar Outlet (3/pkg, 1 key)
1.5 GPM (5.7 L/min)
061296A
Laminar Outlet (3/pkg, 1 key)
2.2 GPM (8.3 L/min)
209989
209989
209989
209989
209989
209989
209989
209989
w w w . s p e c s e l e c t . c o m
OPTION LIST
TRANSFORMERS
060704A
Transformer 110 to 24 VAC 20VA
up to 5 Electronic Valves
060771A
Transformer 110 to 24 VAC 40VA
up to 10 Electronic Valves
DECK PLATES
061269A / 061269SS / 061269BL
4” Deck Plate & Hold-Down Pkg
061270A / 061270SS
8” Deck Plate & Hold-Down Pkg
061295A
Nut & Washer
061269A
061269SS
061269BL
4” Deck Plate
& Holddown Pkg
061270A
061270SS
8” Deck Plate
& Holddown Pkg
061294A
Single Hole
Deck Gasket
for Proximity
Gooseneck
(6/pkg)
061293A
Spacer package for
Proximity Gooseneck
060681A
Battery Holder
Model Number
621TPxxx0
621TPxxx1TR
621TPxxx8TR
620TPxxx0
620TPxxx1TR
620TPxxx8TR
Description
Battery Operated Surface Mount Box #0
Battery Operated Control Box #1 Trim
Battery Operated Control Box #8 Trim
Hard Wire Operated Surface Mount Box #0
Hard Wire Operated Control Box #1 Trim
Hard Wire Operated Control Box #8 Trim
Page #
2
4
6
8
10
12
COVER
060073A
Screws (4/pkg) and driver bit for covers
060577A
12” Stainless Steel Cover
TMV Repair Kits
061137A
Adjustment Wrench
063164A
Check Valves (2/pkg)
INSTALLATION AND SET-UP INSTRUCTIONS
063128A
Battery Box Assembly less driver
board and battery holder
060905A
Cover Gasket
060906A
Surface
Mount Housing
061252A
Dual
Driver Board
060909A
Screen Assembly
063131A
3/8” Comp Connect Nut & Ferrile
063127A
Solenoid Valve with 3/8”
Compression Connectors
and Solenoid Holder
062032A
Braided Polymer Hose
060908A
Solenoid Holder
062032A
Braided Polymer Hose
NOTES:
For optimum performance of this product, the recommended
system pressure is between 20 and 80 PSI static. This
product will operate up to a maximum of 125 PSI static
per ANSI and CSA requirements. However, it is not
recommended the pressure go above 80 PSI. Thermal
expansion or leaking pressure reducing valves may require
the use of expansion tanks or relief valves to ensure your
system never exceeds its maximum intended pressure
setting.
Control Box #0 and #1
Designed for routine 180°F (82°C) disinfection cycles up to
10 minutes.
Control Box #8
High temperature disinfection cycles not recommended
for #8 control box as the thermostatic mixing valve limits
the higher temperature water flow output.
• Use 3-conductor 18AWG wire between transformer and
hardwire converter / driver board earth ground.
• Use Delta Commercial approved transformers and mount
the transformer a minimum of 6” (152 mm) away from the
Delta driver board enclosure.
• Refer to
Proximity Application Notes
on SpecSelect for
installation best practices, proper grounding and wiring
diagrams.