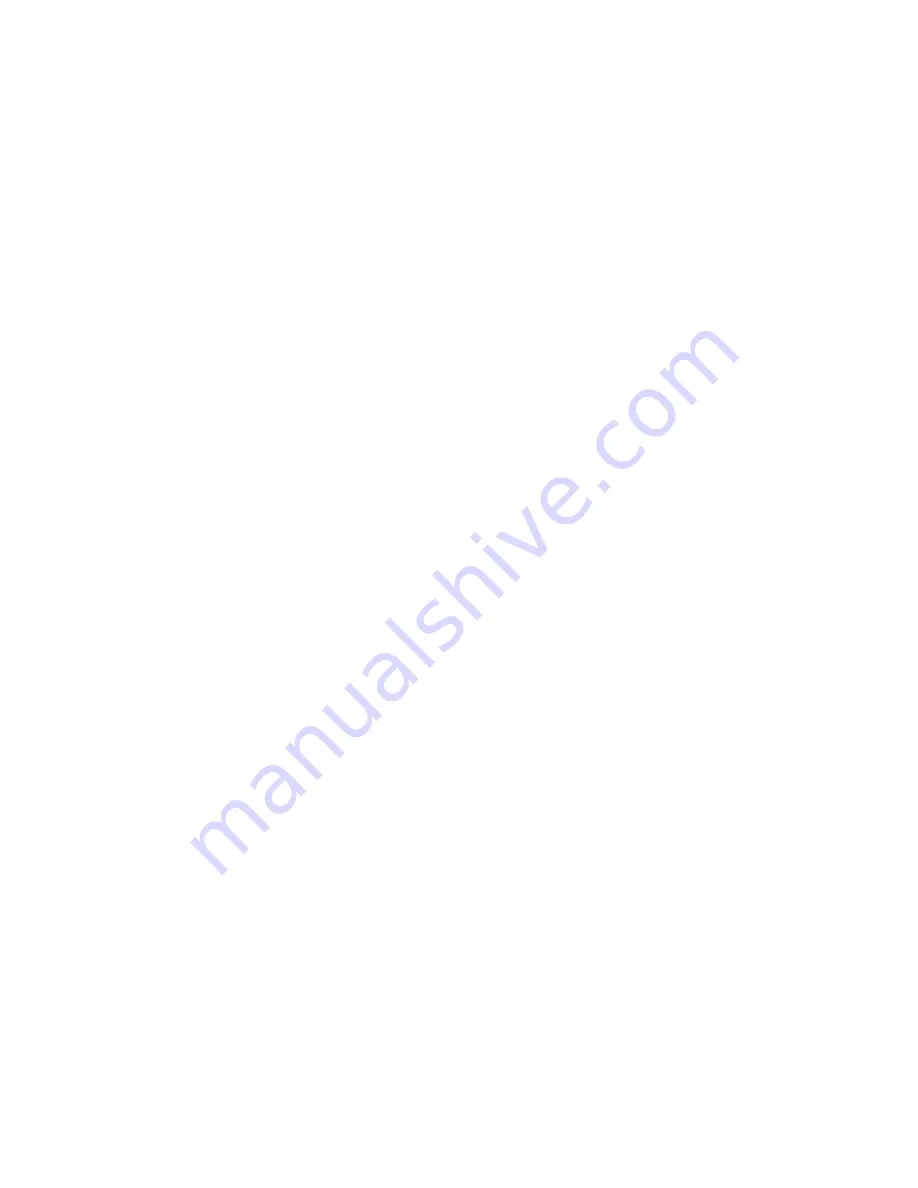
ADDITIONAL SAFETY RULES
FOR DRILL PRESSES
1. WARNING: DO NOT operate your drill press until it is
completely assembled and installed according to the
instructions.
2. IF YOU ARE NOT thoroughly familiar with the opera-
tion of drill presses, obtain advice from your supervisor,
instructor or other qualified person.
3. YOUR DRILL PRESS MUST be securely fastened to a
stand, workbench or floor. If there is any tendency for the
stand or workbench to move during operation, the stand or
workbench MUST be fastened to the floor.
4. NEVER turn the drill press “on” before clearing the
table of all objects (tools, scrap pieces, etc.).
5. NEVER start the drill press with the drill bit or cutting
tool in contact with the workpiece.
6. ALWAYS keep hands and fingers away from the drill bit
or cutting tool.
7. DO NOT ATTEMPT to drill material that does not have
a flat surface, unless a suitable support is used.
8. AVOID awkward hand positions where a sudden slip
could cause a hand to move into the drill bit or cutting
tool.
9. TO PREVENT ROTATION OF THE WORKPIECE,
ALWAYS clamp work securely to table if it is too short to
contact the column (see “OPERATION” section of this
manual) or when using hole saw or cutting tools larger than
1/2² in diameter.
10. WHENEVER POSSIBLE use clamps or vise to keep
workpiece from rotating with the drill bit or cutting tool.
11. USE recommended speed for drill, accessory or work-
piece material.
12. WARNING: The use of accessories or attachments not
recommended by Delta may result in risk of injury.
13. MAKE CERTAIN all lock handles are tightened before
starting the machine.
14. NEVER perform layout, assembly or set-up work on
the table while the drill is operating.
15. BE SURE drill bit or cutting tool is not damaged and is
properly locked in the chuck before operating.
16. MAKE SURE chuck key is removed from chuck before
starting drill press. ONLY use chuck key provided with
your drill press. It is equipped with a self-ejecting pin
which eliminates the hazard of the key being left in the
chuck.
17. ADJUST the table or depth stop to avoid drilling into
the table.
18. ALWAYS stop the drill press before removing scrap
pieces from the table.
19. WHEN drilling large workpieces, MAKE SURE the
material is supported at table height.
20. SHUT OFF the power, remove the drill bit or cutting
tool, and clean the table and work area before leaving the
machine.
21. WARNING: DO NOT wear gloves, necktie, or loose
clothing when operating the drill press.
22. SHOULD any part of your drill press be missing, dam-
aged or fail in any way, or any electrical component fail to
perform properly, shut off switch and remove plug from
power supply outlet. Replace missing, damaged or failed
parts before resuming operation.
23. ADDITIONAL INFORMATION regarding the safe and
proper operation of this product is available from the
National Safety Council, 1121 Spring Lake Drive, Itasca,
Illinois 60143-3201, in the Accident Prevention Manual for
Industrial Operations and also in the Safety Data Sheets
provided by the NSC. Please also refer to the American
National Standards Institute ANSI 01.1 Safety
Requirements for Woodworking Machinery and the U.S.
Department of Labor OSHA 1910.212 and 1910.213
Regulations.
24. SAVE THESE INSTRUCTIONS. Refer to them fre-
quently and use them to instruct others.