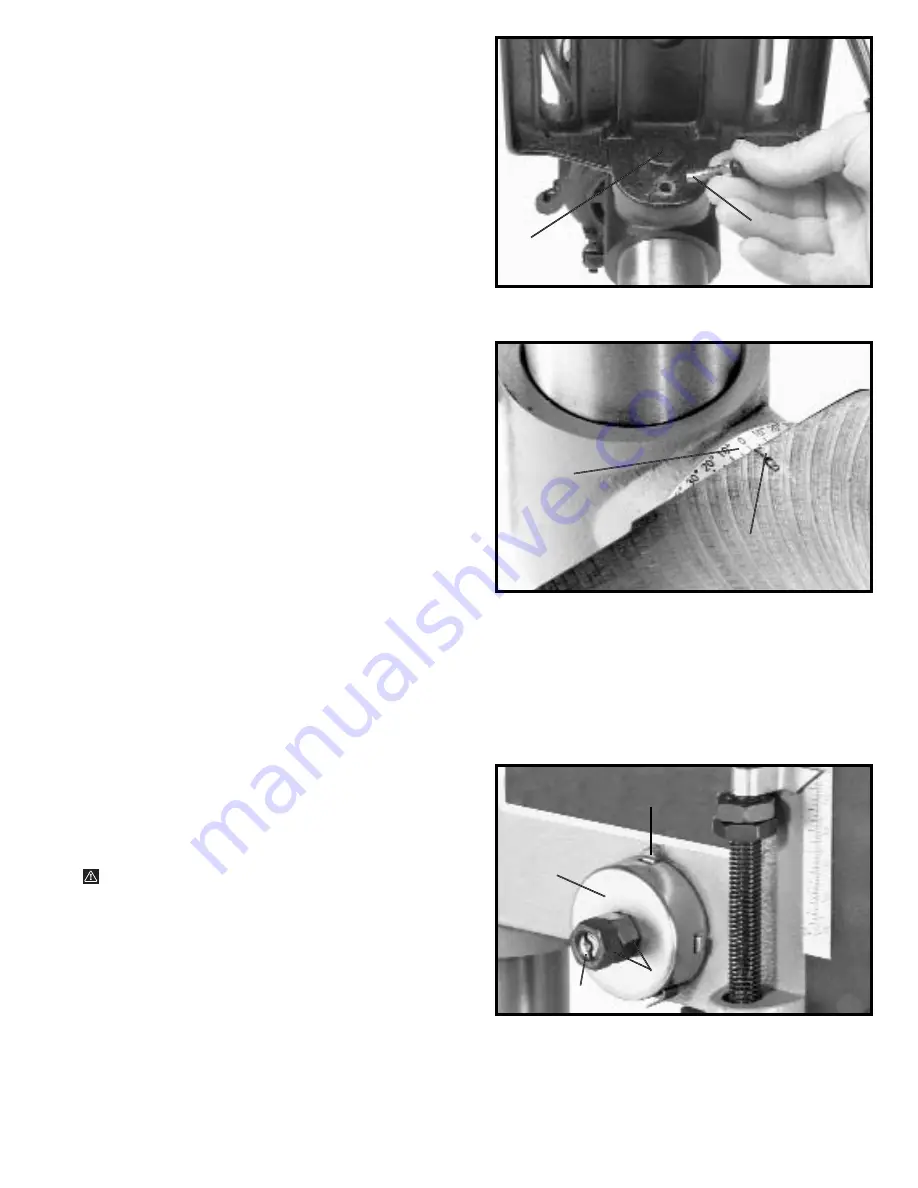
11
Fig. 22
The spindle is automatically returned to its upper most
position upon release of the handle. It is recommended
that the handle be allowed to slowly return to the top
position after all holes have been bored in the material.
This spring has been properly adjusted at the factory and
should not be disturbed unless absolutely necessary. To
adjust the return spring, proceed as follows:
WARNING: MAKE SURE THE TOOL IS DIS-
CONNECTED FROM THE POWER SOURCE.
1.
Loosen the two nuts (B) Fig. 24, approximately 1/4".
Do not remove nuts (B) from shaft (C).
2.
While firmly holding spring housing (A) Fig. 24, pull
out housing and rotate it until the boss (D) is engaged
with the next notch on the housing. Turn the housing
counterclockwise to increase and clockwise to de-
crease spring tension. Then tighten the two nuts (B) to
hold the housing in place.
IMPORTANT:
Inside nut (B)
should not contact spring housing (A) when tight.
Fig. 24
ADJUSTING SPINDLE RETURN SPRING
Fig. 23
3.
Fig. 22, illustrates the table alignment pin (B)
removed. Loosen table locking bolt (D), tilt table to the
desired angle and tighten bolt (D). When returning table
to the level position, replace table alignment pin (B). This
will automatically position the table surface at 90
degrees to the spindle.
4.
A tilt scale (E) Fig. 23, is provided on the table
bracket casting to indicate the degree of tilt. A witness
line and zero mark (F) are also provided on the table to
line up with the scale (E).
E
F
D
A
C
B
D
B