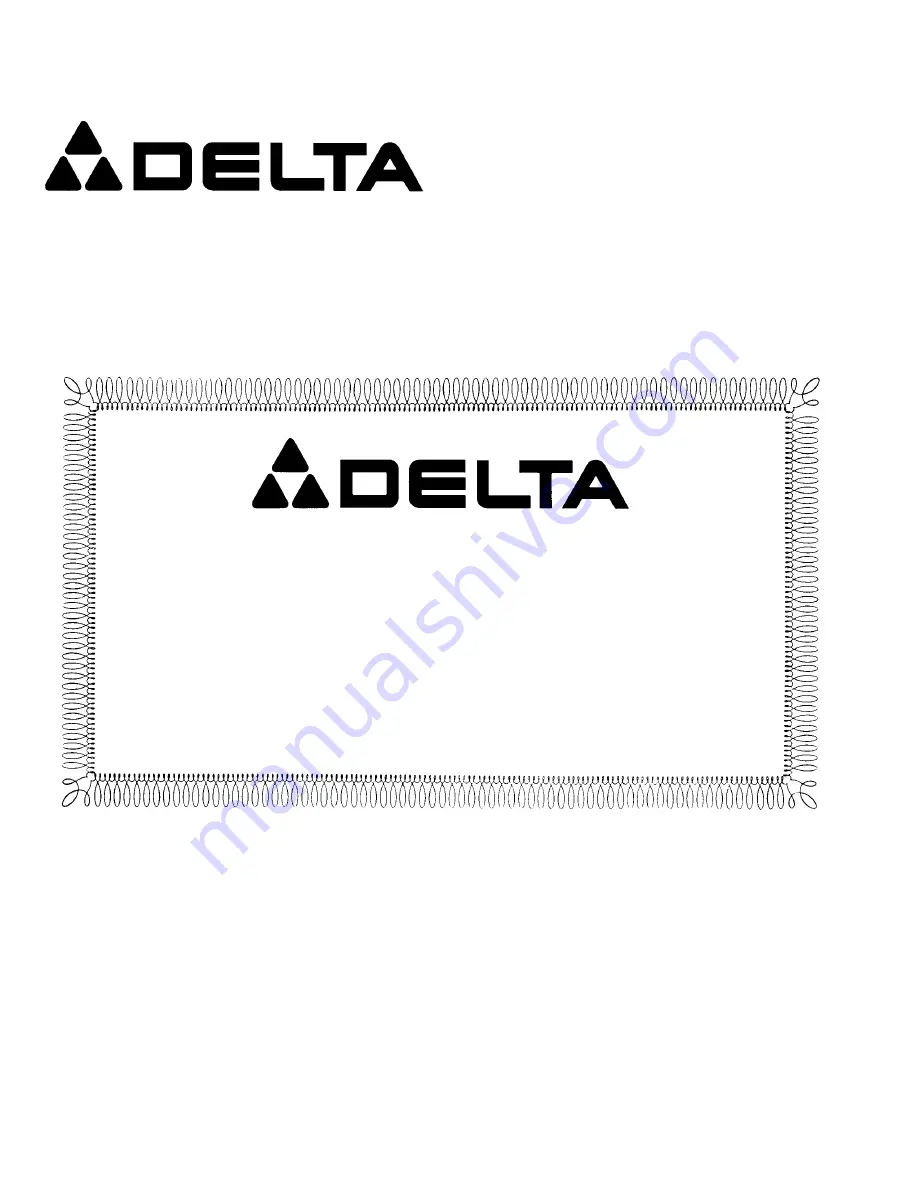
14
Delta Building Trades and Home Shop Machinery
Two Year Limited Warranty
Delta will repair or replace, at its expense and at its option, any Delta machine, machine part, or machine
accessory which in normal use has proven to be defective in workmanship or material, provided that the customer
returns the product prepaid to a Delta factory service center or authorized service station with proof of purchase
of the product within two years and provides Delta with reasonable opportunity to verify the alleged defect by
inspection. Delta may require that electric motors be returned prepaid to a motor manufacturer’s authorized
station for inspection and repair or replacement. Delta will not be responsible for any asserted defect which has
resulted from normal wear, misuse, abuse or repair or alteration made or specifically authorized by anyone other
than an authorized Delta Service facility or representative. Under no circumstances will Delta be liable for
incidental or consequential damages resulting from defective products. This warranty is Delta’s sole warranty and
sets forth the customer’s exclusive remedy, with respect to defective products; all other warranties, express or
implied, whether of merchantability, fitness for purpose, or otherwise, are expressly disclaimed by Delta.
All Delta Machines and accessories are manufactured to high quality standards and are serviced by a network of Porter-Cable/Delta
Factory Service Centers and Delta Authorized Service Stations. To obtain additional information regarding your Delta quality product or
to obtain parts, service, warranty assistance, or the location of the nearest service outlet, please call 1-800-223-7278 (In Canada call
1-800-463-3582).