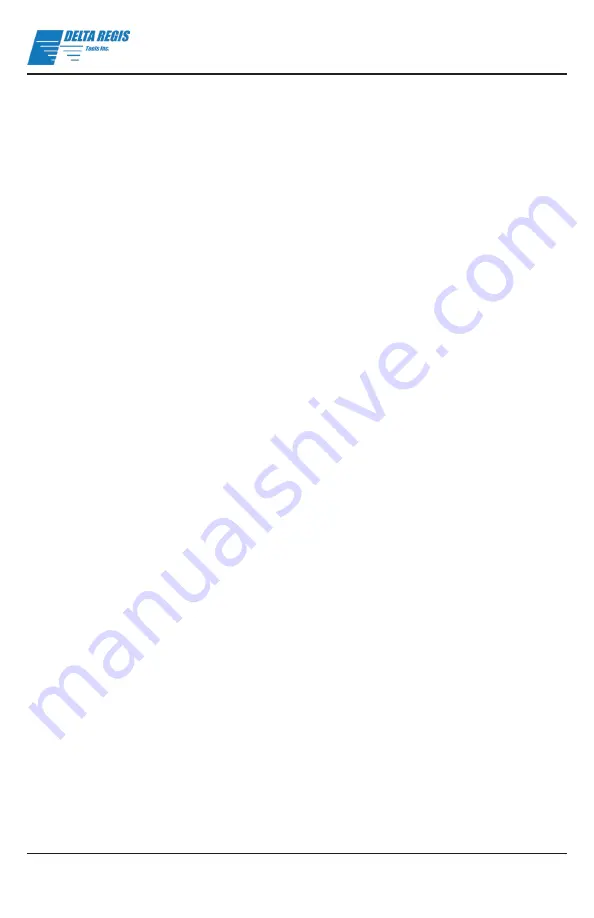
DRFF-208R / DRFF-512R / DRFF-519R Screw Feeder
Operation and Setup Manual
www.deltaregis.com
2
Warning — Failure to understand and follow proper installation guidelines, safety requirements,
and operating instructions may result in malfunction, component damage, property damage,
shock hazard, fire hazard, injury or death.
•
Please read and understand the operation manual and follow all safety and operation
instructions.
•
Use these products in a suitable dry, indoor location. Do not use the screw feeder in damp,
wet, or high temperature environments. Do not use in the presence of flammable liquids or
gases.
•
Use only a properly grounded electrical outlet of the correct supply voltage to power the
screw feeder.
•
Ensure that the supply outlet is overload protected and of sufficient amperage capacity.
•
Use only the supplied AC adapter and power cord for the screw feeder and outlet. Hold the
plug of the power cord when connecting or disconnecting. Do not pull on the cable.
•
Do not expose the cable, AC adapter or screw feeder to oil, chemicals, or heat. Ensure that
the cable is routed and used in such a manner as to not be subject to sharp objects that
may abrade or cut the cable.
•
Locate the screw feeder in a suitable, safe location on a steady, level surface.
•
Do not place in a high location where there may be a risk of it falling.
•
Do not tilt the screw feeder.
•
Do not raise the front or rear of the screw feeder.
•
The screw feeder rail must be kept free from oil, grease, dust or any other contaminates.
•
Do not place you hand or any foreign objects into the screw hopper when the unit is
running.
•
In the event that the screw feeder is overloaded beyond the maximum current rating, an
internal circuit will disrupt power and the screw feeder will produce an error code. Should
the screw feeder stop functioning, or exhibit abnormal or intermittent operation, please
discontinue use immediately and send the screw feeder to an authorized service center for
troubleshooting and repair.
•
Turn the main power switch off when the screw feeder is not being used. Unplug the screw
feeder if it is not being used on a regular basis.
•
Do not attempt to disassemble or repair the screw feeder. Repairs should only be
performed by qualified technicians properly trained in the safe operation, troubleshooting,
and repair of these devices. Please consult Delta Regis for the location of the nearest service
depot.
•
Use only the factory specified Delta Regis brand replacement parts and accessories with
these screw feeders.
•
Any damage to the screw feeder resulting from misuse, abuse, or failure to follow these
guidelines will void the limited product warranty.
Grounding — The AC power cord is equipped with a 3-prong electrical receptacle/plug with
ground pin. The screw feeder must be connected to a properly grounded AC electrical outlet. Do
not attempt to use this screw feeder without a properly functioning ground connection. Never
connect a live circuit to the ground pin or internal yellow-green ground wire.