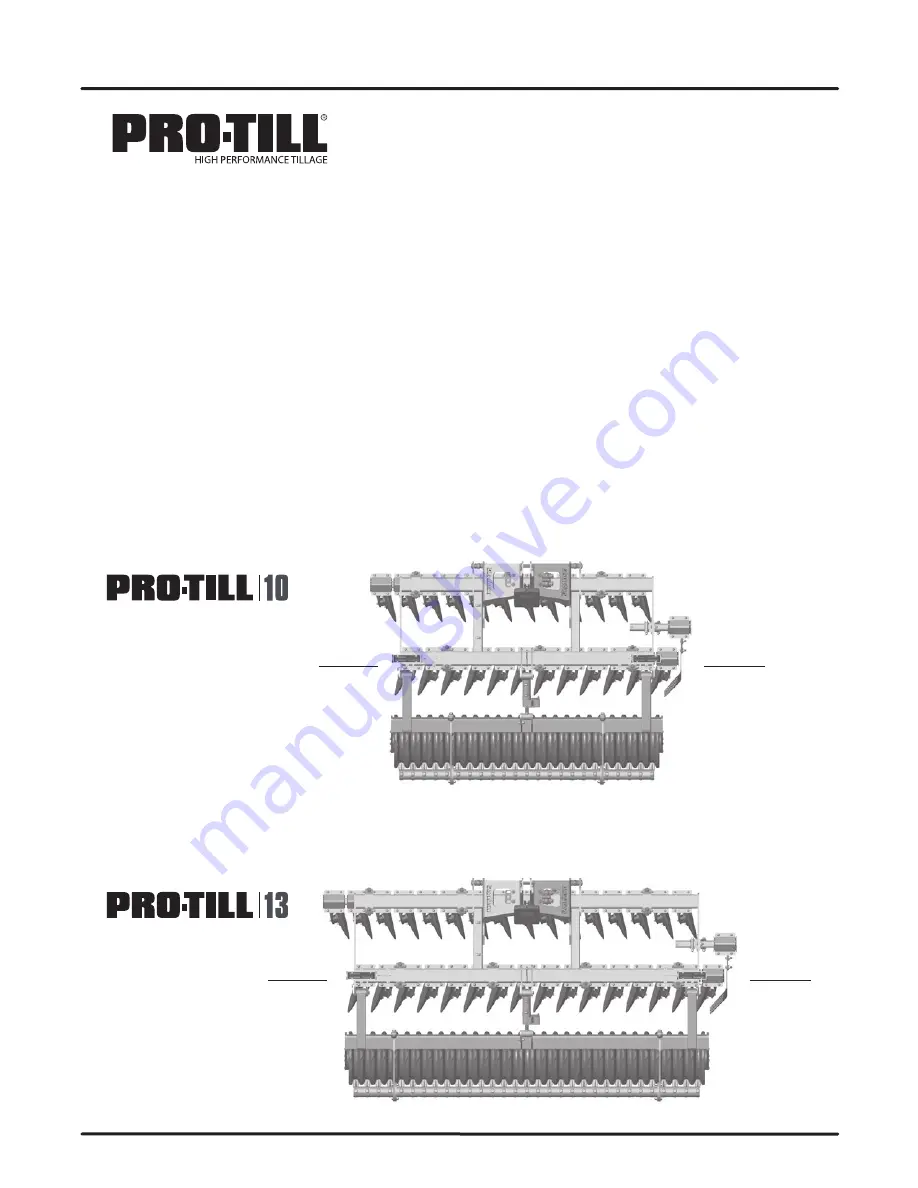
-1-
142766 - PRO-TILL 10|13 (10-February-2022)
Introduction
OPERATOR ORIENTATION
- The directions left, right, front and rear, as mentioned throughout the manual,
are as seen from the tractor drivers’ seat and facing in the direction of travel.
CONGRATULATIONS
on your choice of a Degelman PRO-TILL to complement your farming operation. It has
been designed and manufactured to meet the needs of a discerning agricultural market. Degelman PRO-TILL
shreds heavy fall residue, opens up spring fields, levels ruts, destroys clods and produces an absolutely perfect
seed bed. Degelman PRO-TILL is the fastest and most versatile piece of tillage equipment you will ever own.
Use this manual as your first source of information about this machine.
TO THE NEW OPERATOR OR OWNER
- Safe, efficient and trouble free operation of your Degelman PRO-TILL
requires that you and anyone else who will be operating or maintaining it, read and understand the Safety,
Operation, Maintenance and Troubleshooting information contained within this manual.
By following the operating instructions in conjunction with a good maintenance program your machine will
provide many years of trouble-free service. Keep this manual handy for frequent reference and to pass on to
new operators or owners. Call your Degelman Dealer if you need assistance, information, or additional copies
of the manual.
Front 3-point Hitch
Front 3-point Hitch
Roller Assembly
Roller Assembly
LH SIDE
LH SIDE
RH SIDE
RH SIDE
Summary of Contents for PRO-TILL 10
Page 2: ......