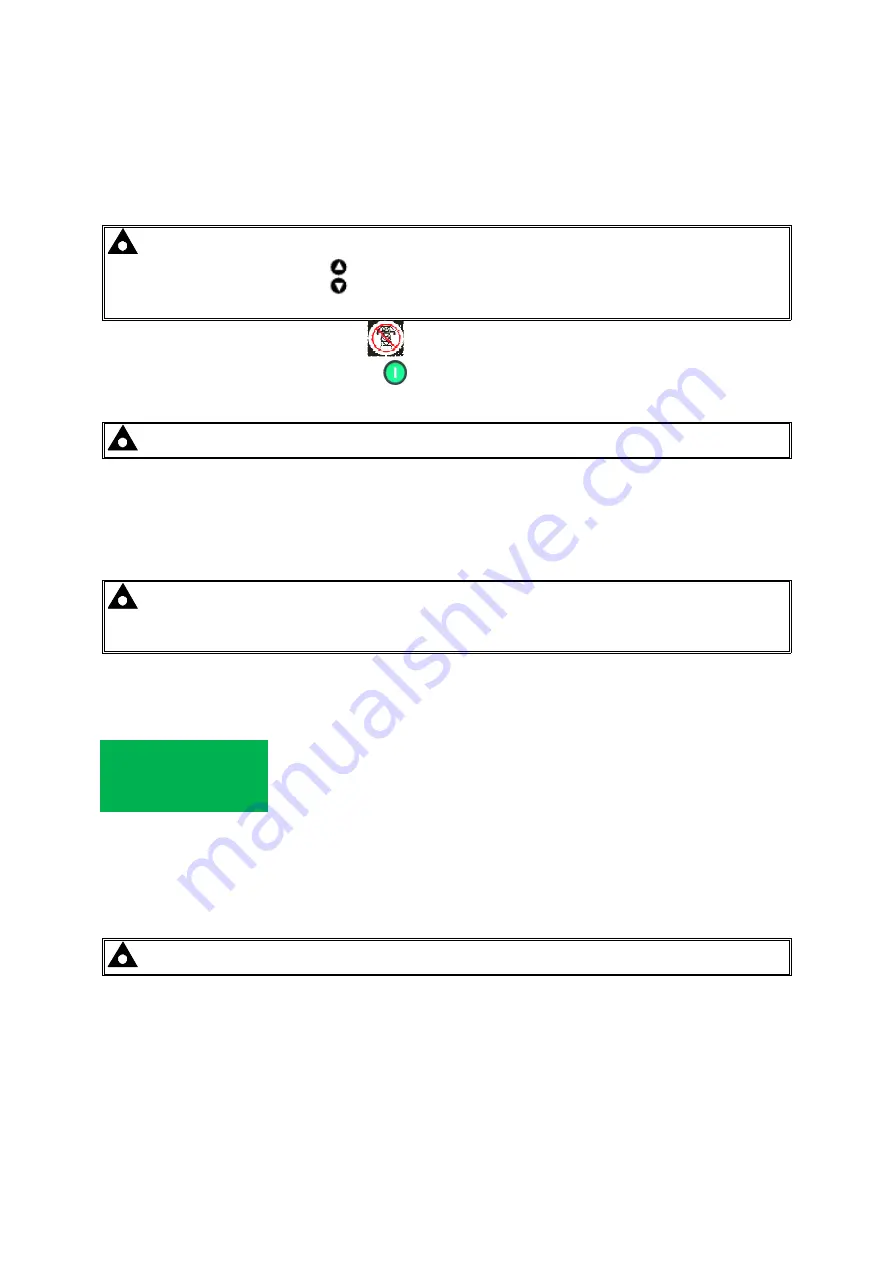
DSE Model 8620 AMF Controller Operators Manual
83
6.7 TEST OPERATION
Test operation is used to perform a full on load test sequence to allow for diagnosis of faults.
Alternatively, it may also be used to provide continuity of supply during expected black out events, peak
lopping or peak shaving during high tariff periods.
NOTE: - If a digital input configured to panel lock is active, changing module modes will not be
possible. Viewing the instruments
and event log is NOT affected by panel lock. If panel lock is active
the Panel lock indicator (if configured) illuminates.
TEST mode is initiated by pressing the
pushbutton. An LED besides the button will illuminate to
confirm this operation. When the START
button is operated, the module will initiate the start
sequence.
NOTE: - There is no Start Delay in this mode of operation.
If the pre-heat output option has been selected, this timer will initiate and the auxiliary output selected
will be energised.
After the above delay, the Fuel Solenoid (or ECU output if configured) is energised, and then one
second later, the Starter Motor is engaged.
NOTE: - If the unit has been configured for CAN Bus, compatible ECU’s will receive the start command
via CAN Bus. Refer to the Manual CAN and DSE Wiring. Part No. 057-004 for more information on utilising
DSE modules with electronically controlled engines.
The engine is cranked for a pre-set time. If the engine fails to fire during this cranking attempt then the
starter motor is disengaged for the pre-set rest period. Should this sequence continue beyond the set
number of attempts, the start sequence will be terminated and Fail to Start will be displayed.
Alarm
Shutdown
Fail to start
When the engine fires, the starter motor is disengaged and locked out at a pre-set frequency from the
Alternator output. Alternatively, a Magnetic Pickup mounted on the flywheel housing can be used for
speed detection (This is selected by PC using the DSE Configuration Suite software). Rising oil
pressure can also be used to disconnect the starter motor; however, it cannot be used for underspeed
or overspeed detection.
NOTE: - If the unit has been configured for CAN Bus speed sensing is via CAN Bus.
After the starter motor has disengaged, the Safety On timer is activated, allowing Oil Pressure, High
Engine Temperature, Under-speed, Charge Fail and any delayed Auxiliary fault inputs to stabilise
without triggering the fault.