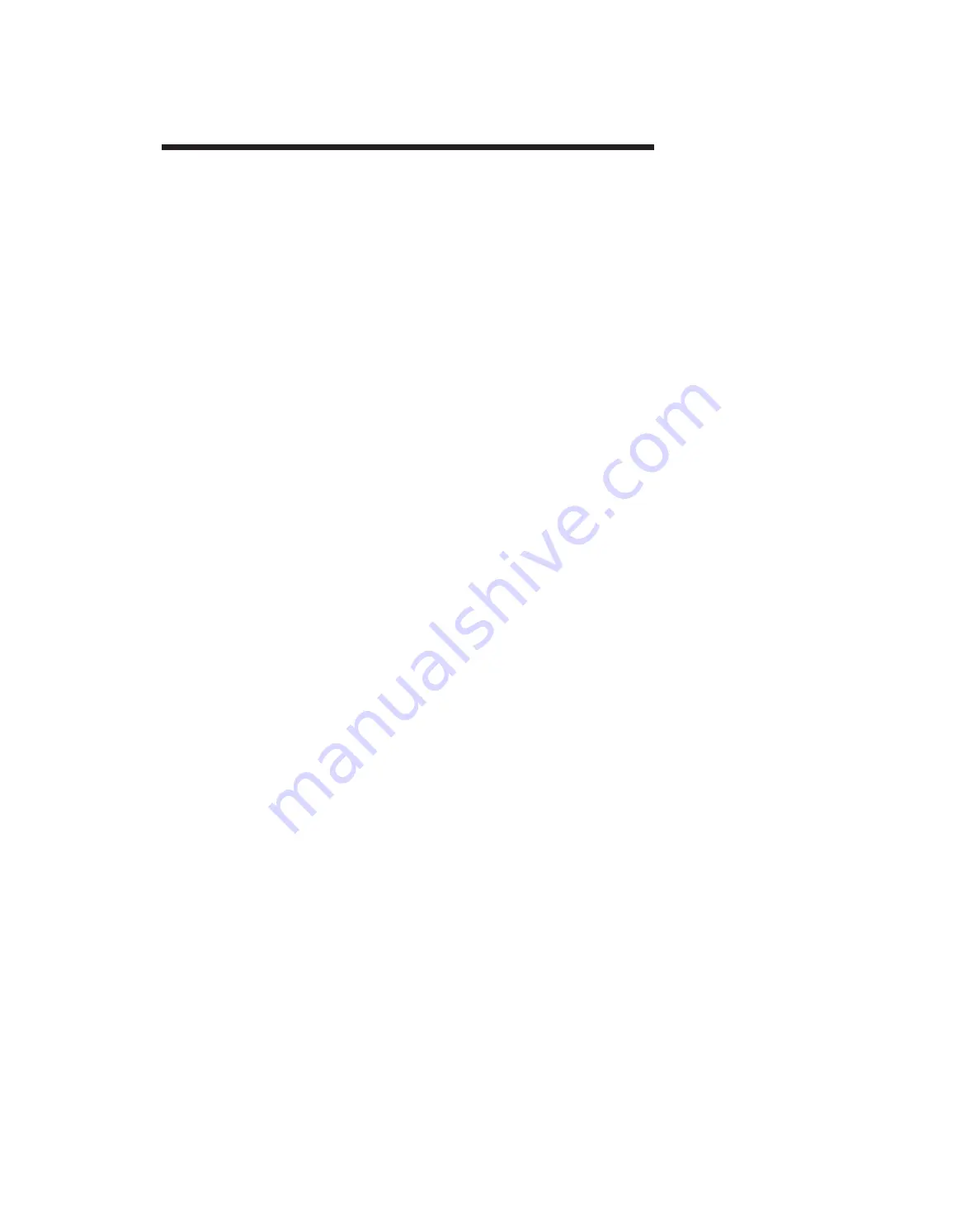
After calibrating your 4030's "live" input channel (No. 1), you should set
the high and low endpoints for the individual BARGRAPH display of
Channel 5 ("LIVE" INPUT WITH TARE), using the procedure given
below. This same procedure may be used to scale the bargraph dis-
play of any of the other 4030 data channels listed in Section 1.d. For
the relation of BARGRAPH endpoint values to the other four limit-zone-
defining parameters, see Fig. 8 in the next section.
1.
Display Channel 5 (see Section 2.d).
2.
Following the general procedure explained in Section 1.f, enter
"SETUP" mode and step to the "LEP" (LOW ENDPOINT)
parameter.
The initial "LEP" setting for Channel 5 is normally "-1.000." THIS
WILL HAVE BEEN AUTOMATICALLY SCALED, HOWEVER, SO
THAT ITS DECIMAL-POINT LOCATION MATCHES THAT OF THE
SCALING FACTOR ("F1") YOU ENTERED WHEN YOU CALI-
BRATED CHANNEL 1 IN SECTION 2.e. If, for example, your "F1"
value for Channel 1 was "XXX.X" (where "X" is any number), the
displayed "LEP" value for Channel 5 will be "-100.0." The
decimal-point position will always be the same for all six limit-zone
parameters ("LEP," "LLL," "LOL," "HIL," "HHL," and "HEP").
As mentioned in Section 1.f,
this position cannot be changed, since
it depends directly on the precision of the last "F1" entry.
3.
Using the "ARROW" buttons as explained in Section 1.f, enter the
desired LOW ENDPOINT value for the bargraph display of Chan-
nel 5, as expressed in the engineering units selected for that
channel.
4.
Press the STEP button five times. The "HEP" parameter should
now be displayed. Enter the desired HIGH ENDPOINT value for
the bargraph display of Channel 5 (again, as expressed in the
engineering units selected for that channel). The initial "HEP"
setting for Channel 5 is normally "1.000."
The "LEP" and "HEP" values for a given channel may be any numeric
constants from -32768 through 32767, provided that the "LEP" value is
less than the "HEP" value. At least 51 units (absolute count) must
separate the HEP and LEP values.
Scaling the Bargraph Display
2.g
2.12