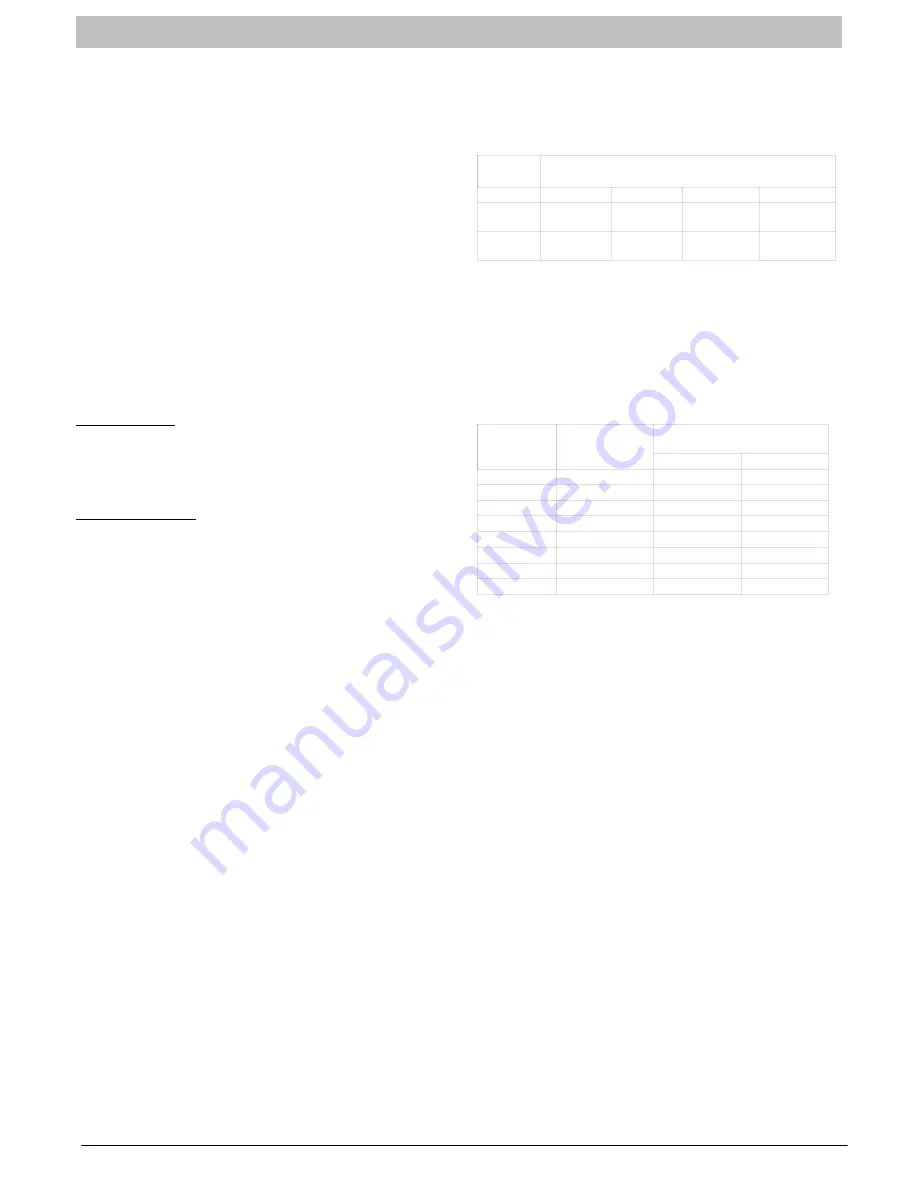
INSTALLATION INSTRUCTIONS
R
−
410A Split System Heat Pumps
428 01 1703 01
11
Specifications subject to change without notice.
Forced Defrost
On a system with non
−
communicating (non-Observer)
control, forced defrost can be initiated by manually shorting
the 2-pin header labeled FORCED DEFROST (see Fig 14)
on the control board for 5 seconds then releasing.
If coil temperature is at defrost temperature of 32
°
F
(0
°
C), and outdoor air temperature is below 50
°
F
(10
°
C), a full defrost sequence will occur.
If coil temperature or outdoor air temperature does not
meet the above requirements, an abbreviated 30
second defrost will occur.
Quiet Shift
−
2
Quiet Shift
−
2 is a field
−
selectable defrost mode which may
eliminate occasional noise that could be heard at the start
and finish of the defrost cycle. For installations using a
standard 2
−
stage thermostat, this feature must be enabled
by selecting the 3
rd
position dip switch on the outdoor control
board. For installations using an Observer Wall Control, it
must be enabled at the Wall Control. When activated, the
following sequence of operation occurs:
Defrost Initiation
−
the compressor is de
−
energized for 70
seconds. During this 70 second compressor off time, the
reversing valve will be energized. Once the 70 second
compressor off time has been reached, the compressor will
be energized then the outdoor fan will be de
−
energized at
which time the normal defrost cycle begins.
Defrost Termination
−
The outdoor fan will be energized
shortly before the compressor is de
−
energized for 60
seconds. During the compressor 60 second off time, the
reversing valve will be de
−
energized. Once the 60 second
compressor off time has been completed, the compressor will
be energized at which time the system will be in normal heat
mode.
Liquid
−
Line Accessory
In heat pump long
−
line applications, a liquid
−
line solenoid is
required to control refrigerant migration in the heating mode.
The solenoid should be installed near the outdoor unit with
the arrow facing the outdoor unit. This is the direction of flow
control. See application manual for long
−
line application
details.
Accessory Liquid Solenoid with Observer Communicating
Wall Control: When using the Observer Wall Control, the
liquid-line solenoid output is provided at the Y1 connection.
Connect the solenoid as shown in the wiring label diagram.
This is a 24vac output that is energized whenever the
compressor is energized. It closes, in the compressor off
mode, to prevent refrigerant migration into the unit through
the liquid
−
line.
On Systems with Accessory Liquid Solenoid Using a
Non
−
Communicating Thermostat: The liquid solenoid is
connected to the Y1 and C terminal connections. The liquid
solenoid closes, in the compressor off mode, to prevent
refrigerant migration into the unit through the liquid
−
line.
TROUBLESHOOTING
If the compressor fails to operate with a cooling call, Table 4
can be used to verify if there is any damage to the
compressor windings causing system malfunction.
Table 4
−
Winding Resistance
Winding Resistance At 70
F +/
−
20
F
(21.11
C +/
−
11.11
C)
Winding
24
36
48
60
Start
(S
−
C)
1.64
1.52
1.86
1.63
Run
(R
−
C)
1.30
0.88
0.52
0.39
Systems Communication Failure
If communication with the Observer Communicating Wall
Control will flash the appropriate fault code. (See Table 6)
Check the wiring to the wall control, indoor and outdoor units.
Model Plug
Each control board contains a model plug. The correct model
plug must be installed for or the system to operate properly
(see Table 5).
Table 5
−
Model Plug
Model
Number
Model Plug
Number
Pin Resistance
(kOhms)
Pin 1
−
4
Pin 2
−
3
*CH624
HK70EZ041
18
91
*CH636
HK70EZ043
18
150
*CH648
HK70EZ045
18
220
*CH660
HK70EZ047
18
360
*CH924
HK70EZ010
5.1
120
*CH936
HK70EZ012
5.1
180
*CH948
HK70EZ014
5.1
270
*CH960
HK70EZ016
11
5.1
The model plug is used to identify the type and size of unit to
the control.
On new units, the model and serial numbers are input into
the board’s memory at the factory. If a model plug is lost or
missing at initial installation, the unit will operate according to
the information input at the factory and the appropriate error
code will flash temporarily.
A FAST® Parts replacement board contains no model and
serial information. If the factory control board fails, the model
plug must be transferred from the original board to the
replacement board for the unit to operate.
NOTE
:
The model plug takes priority over factory model
information input at the factory. If the model plug is removed
after initial power up, the unit will operate according to the last
valid model plug installed, and flash the appropriate fault code
temporarily.
Pressure Switch Protection
The outdoor unit is equipped with high and low pressure
switches.
If the control senses the opening of a high or low pressure
switch, it will respond as follows:
1.
De-energize the appropriate compressor contactor.
2.
Keep the outdoor fan operating for 15 minutes.
3.
Display the appropriate fault code (see Table 6).
4.
After a 15 minute delay, if there is still a call for cooling
and the LPS or HPS is reset, the appropriate
compressor contactor is energized.
5.
If LPS or HPS has not closed after a 15 minute delay,
the outdoor fan is turned off. If the open switch closes
anytime after the 15 minute delay, then resume
operation with a call for cooling.