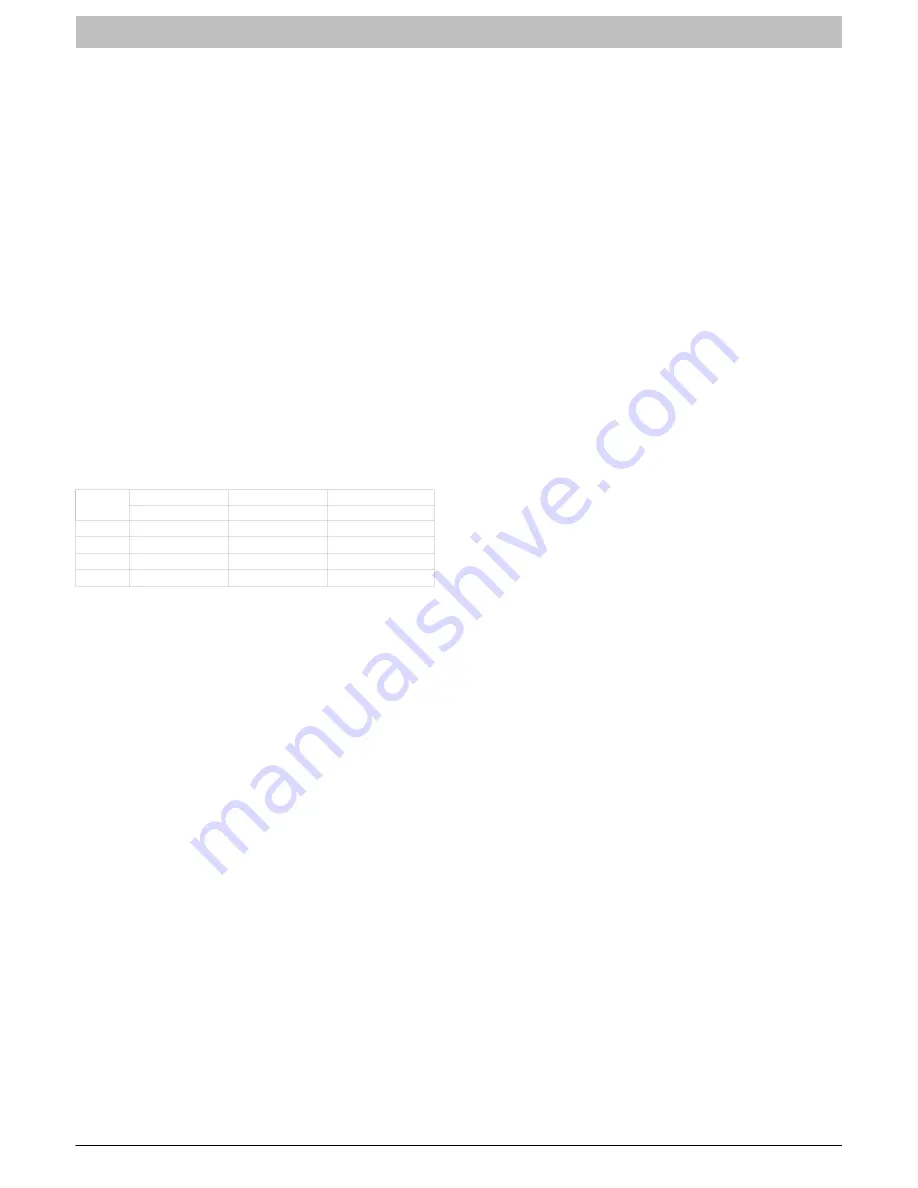
INSTALLATION INSTRUCTIONS
R
−
410A Split System Heat Pumps
10
428 01 1703 01
Specifications subject to change without notice.
the crankcase heater remains de-energized after the
compressor is turned off.
Outdoor Fan Motor Operation
The outdoor unit control energizes the outdoor fan any time
the compressor is operating. The outdoor fan remains
energized if a pressure switch or compressor overload
should open. Outdoor fan motor will continue to operate for
one minute after the compressor shuts off when the outdoor
ambient is greater than or equal to 100
F (37.8
C) to allow
for easier starting during next cooling cycle.
On CCH6, HCH6 and TCH6 models - The outdoor fan motor
is a PSC type. A fan relay on the control board turns the fan
off and on by opening and closing a high voltage circuit to the
motor. It does not change speeds between low and high
stage operation.
On CCH9, HCH9 and TCH9 models
−
The outdoor fan is an
ECM type. The motor control is continuously powered with
high voltage. The motor speed is determined by electrical
pulses provided by the PWM outputs on the control board.
The ECM motor RPM adjusts to outdoor conditions as
described in Table 3. The PWM output can be measured
between the PWM1 and PWM2 terminals on the circuit board
with a volt meter set to DC volts.
Table 3
−
Outdoor Fan Motor PWM
Outdoor Temp (DC volts, Tol/
−
2%)
Model
Size
Low
−
Stage
High Stage
Low & High Stage
OAT
104
F/ 40
C OAT
104
F/ 40
C OAT > 104
F/ 40
C
924
8.72
9.35
11.90
936
9.06
10.23
11.90
948
9.91
11.04
11.90
960
10.83
11.70
11.90
Time Delays
The unit time delays include:
Five minute time delay to start cooling operation when
there is a call from the thermostat or Wall Control. To
bypass this feature, momentarily short and release
Forced Defrost pins or hold the “Cool To” or “Heat To”
button on the Observer Wall Control for 10 seconds.
Five minute compressor re
−
cycle delay on return from
a brown
−
out condition.
Two minute time delay to return to standby operation
from last valid communication (Observer
Communicating Wall Control only).
One minute time delay of outdoor fan at termination of
cooling mode when outdoor ambient is greater than or
equal to 100
F (37.8
C).
Fifteen second delay at termination of defrost before
the auxiliary heat (W1) is de
−
energized.
Twenty second delay at termination of defrost before
the outdoor fan is energized.
Seventy and sixty second compressor delays when
Quiet Shifts
−
2 enabled.
There is no delay between staging from low to high
and from high to low capacity. The compressor will
change from low to high and from high to low capacity
“on the fly” to meet the demand.
DEFROST
This control offers 5 possible defrost interval times: 30, 60,
90, 120 minutes, or AUTO.
Defrost intervals are selected by dip switches on the unit
control board or by the Observer Wall Control. The Observer
Wall Control selection overrides the control board dip switch
settings.
AUTO defrost adjusts the defrost interval time based on the
last defrost time as follows:
When defrost time <3 minutes, the next defrost
interval = 120 minutes.
When defrost time 3 - 5 minutes, the next defrost
interval = 90 minutes.
When defrost time 5 - 7 minutes, the next defrost
interval = 60 minutes.
When defrost time >7 minutes, the next defrost
interval = 30 minutes.
The control board accumulates compressor run time. As the
accumulated run time approaches the selected defrost
interval time, the control board monitors the coil temperature
sensor for a defrost demand. If a defrost demand exists, a
defrost cycle will be initiated at the end of the selected time
interval. A defrost demand exists when the coil temperature
is at or below 32
°
F (0
°
C) for 4 minutes during the interval.
The defrost cycle is terminated when the coil temperature
reaches 65
°
F (18.33
°
C)or 10 minutes has passed. When
OAT is > 25
°
F (-3.9
°
C), defrost will occur in low or high stage
as demanded by the thermostat or Wall Control.
If OAT is
≤
25
°
F (
−
3.9
°
C), defrost will occur in high stage
only, regardless of thermostat or Wall Control demand, and
will terminate at 50
°
F (10
°
C) coil temperature with a
minimum of 2.5 minutes in defrost.
If the coil temperature does not reach 32
°
F (0
°
C) within the
interval, the interval timer will be reset and start over.
Upon initial power up the first defrost interval is
defaulted to 30 minutes. Remaining intervals are at
selected times.
Defrost is only allowed to occur below 50
°
F (10
°
C)
outdoor ambient temperature.
The outdoor fan output (ODF) will remain off for 20 seconds
after termination. This delay will allow time for the system to
capture the heat from the outdoor coil and reduce the “steam
cloud” effect that may occur on transition from defrost to
heating cycle.
Defrost Hold
On a non
−
communicating system, if the thermostat becomes
satisfied (Y1 or Y1 and Y2) before the defrost cycle is
terminated, the control will “hold” in defrost mode and finish
the defrost cycle on the next call for heat.
On models with communicating Observer Wall Control,
defrost hold is not needed because the system will complete
the defrost cycle before shutting down the system.