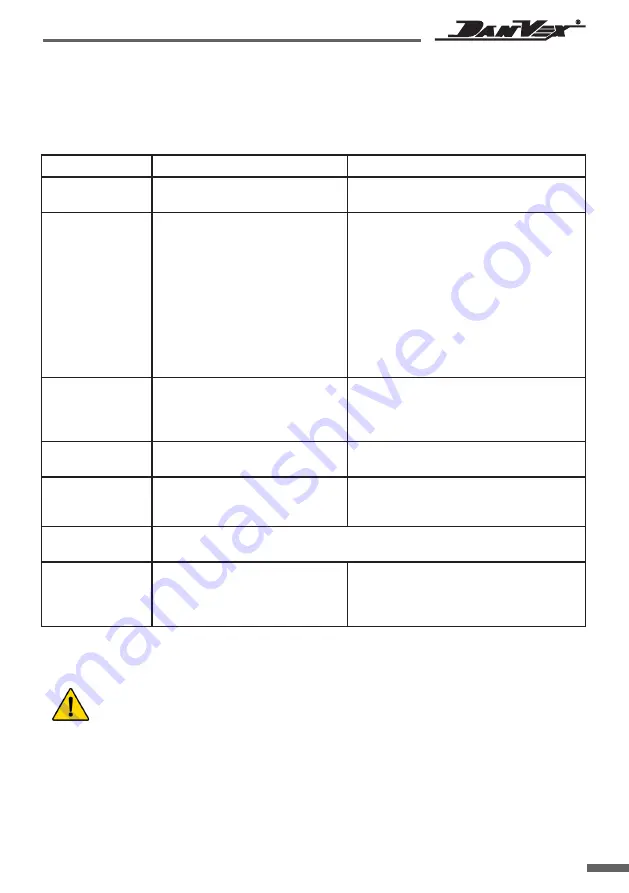
18
www.danvex.fi
6.
PREVENTION AND TROUBLESHOOTING
6.1
Frequency of inspection and maintenance
To prevent failure of units and assemblies of the dryer, it is necessary to periodically inspect
:
Knot
3-6
months
12
months
Filters
Filter cleaning.
If the filter soiled replace it.
Fan
Dust and debris in the cooling groove
on the surface of the motor housing
must be removed.
Check terminals of engine wiring to make
sure the wiring is not loose.
Check fan bearing lubrication
and add lubricating oil.
Check fan impeller for damage.
If there are signs of corrosion,
take immediate action.
Electric motor rotor
Check the drive belt for damage
and correct operation
Check motor wiring
and make sure wiring is not loose.
Check for signs of damage
and overheating.
Heater
Remove debris and dust from
the surface of the heater
Rotor
Check for signs of overheating and blockage.
Clean the dust from the surface of the rotor.
Seals
Check for signs of damage and displacement.
If there is wear or damage, then a replacement is required.
Sensors
of temperature
and humidity
Check the performance of all external
temperature and humidity sensors
and, if necessary, calibrate them
.
There is high voltage inside the block. Before any maintenance work,
check that the device is powered off.
There is a high temperature zone inside the unit (heating section of the regenerator)
that needs to be cooled down before maintenance.
Adjustment, maintenance and repair of the device must be carried out by qualified personnel.
Relevant personnel should be aware of the high temperature and high pressure inside the unit.