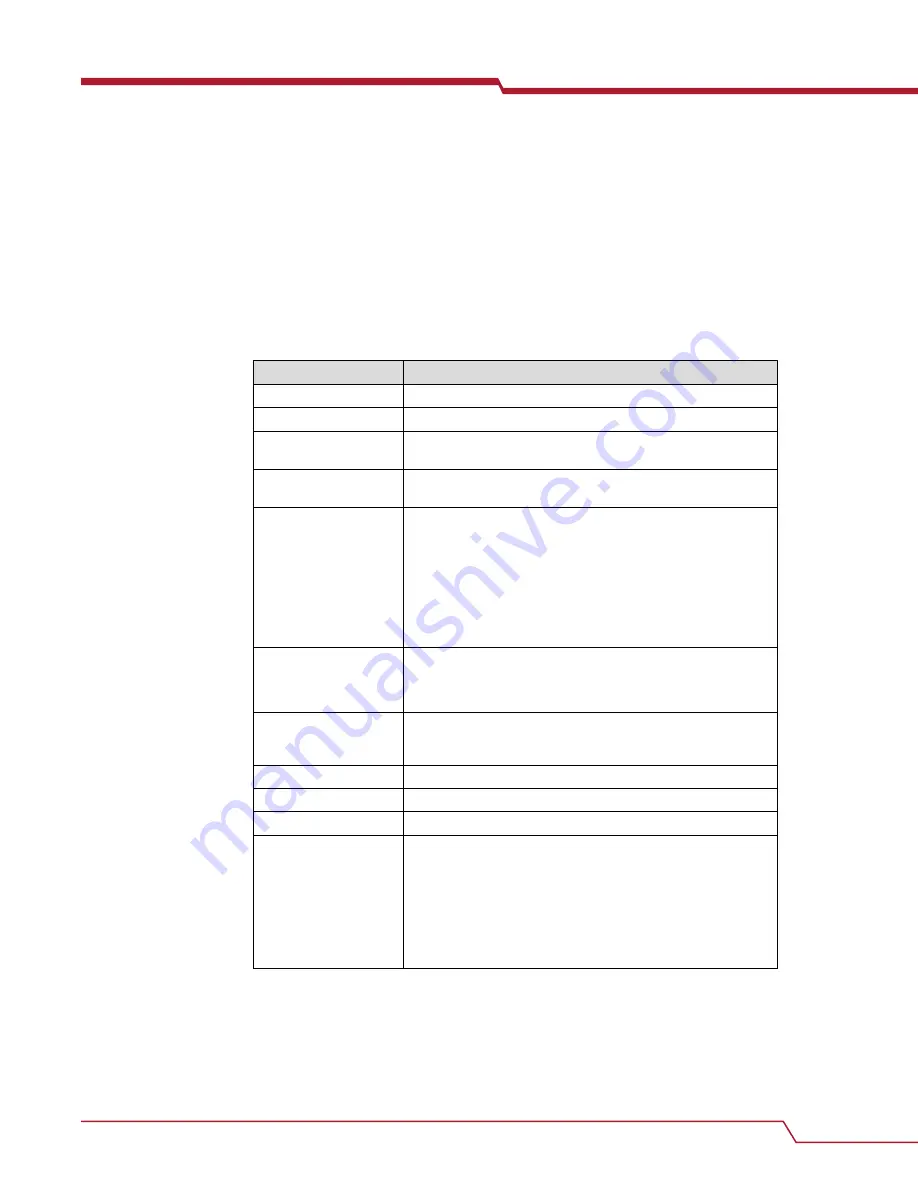
17
www.Daniel.com
USER MANUAL
2
Operating conditions and
specifications
2.1
Operating conditions for the control valve
Table 2-1: Operating conditions for the control valve
Condition type
Description
Fluid phase
Liquid
Process temperature
-20° F to 150° F (-29° C to 66° C)
Optional process
temperature
-50° F to 400° F (-46° C to 205° C )
Fluid velocity
Operational recommended flow velocity up to 30 ft/sec, beyond this
point will result in a high pressure drop and increased wear.
Fluid(s) controlled
•
Low/Medium viscosity crude oils and condensates
•
Refined products and intermediates (ie:
gasoline, diesel, kerosene,
light fuel oils, jet fuel, LPG, butanes, naphtha, alkylate, reformate,
straight run gasoline, cat-cracked gasoline
)
•
Petrochemicals (ie:
benzene, toluene, xylenes, cumene, olefins,
pyrolysis gasoline
)
•
Natural gas liquids
Viscosity limits on valves
and valves with pilots
•
Maximum valve viscosity is 8800 Cst
•
Maximum viscosity for valves with pilots is 440 Cst due to
response time of high viscosity pilot
Differential pressure
The maximum allowable differential pressure across a control valve is
6894 kPa (1,000 psi). Consult factory for location of first shut down
valve.
Atmospheric pressure
Absolute
Sizes (NPS)
2, 3, 4, 6, 8,10,12,16
Pressure class (ANSI)
150, 300, 600
Maximum safe working
temperature range
•
15° F to 400° F (-26° C to 204° C)
•
Using FKM O-rings
•
Temperature range is dependent of O-ring T
min
and T
max
•
Max temperature of valves with solenoid pilots is standard -20° F
to 150° F (-29° C to 66° C) (if applicable), Optional 250° F (121° C)
•
Consult the factory for other safe working temperatures
User manual
Operating conditions and specifications
P/N 3-9008-553
November 2020
User manual
19