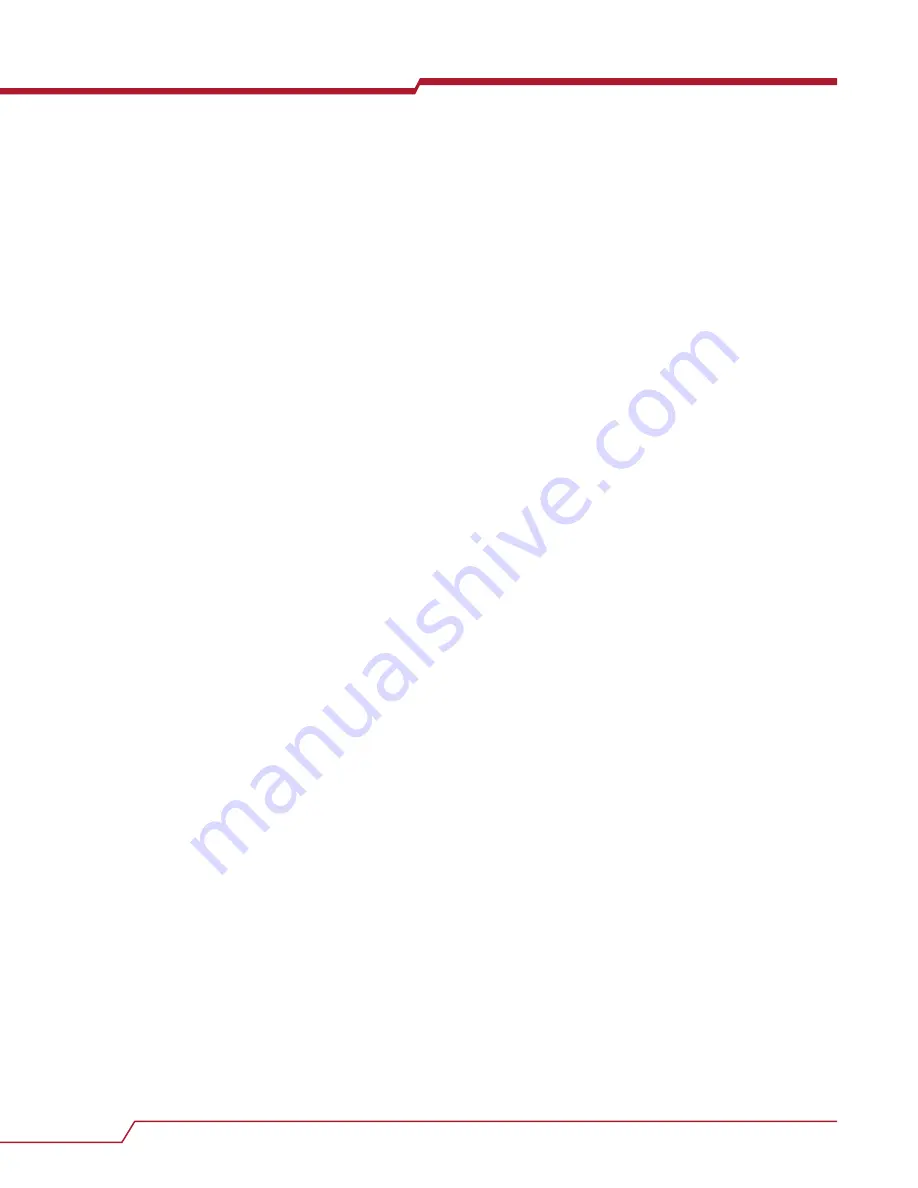
82
www.Daniel.com
SERIES 1200 LIQUID TURBINE METER
3. Evaluate the system setup to ensure that all components are in the correct
sequence for accurate product measurement: isolation valve, strainer, flow
straightener, turbine meter, downstream section, control valve, etc.
4. Ensure that the supply voltage to the preamplifier is within the 10-30 VDC range.
Corrective maintenance
User manual
September 2020
P/N 3-9008-513
92
Daniel Series 1200 Liquid Turbine Meter