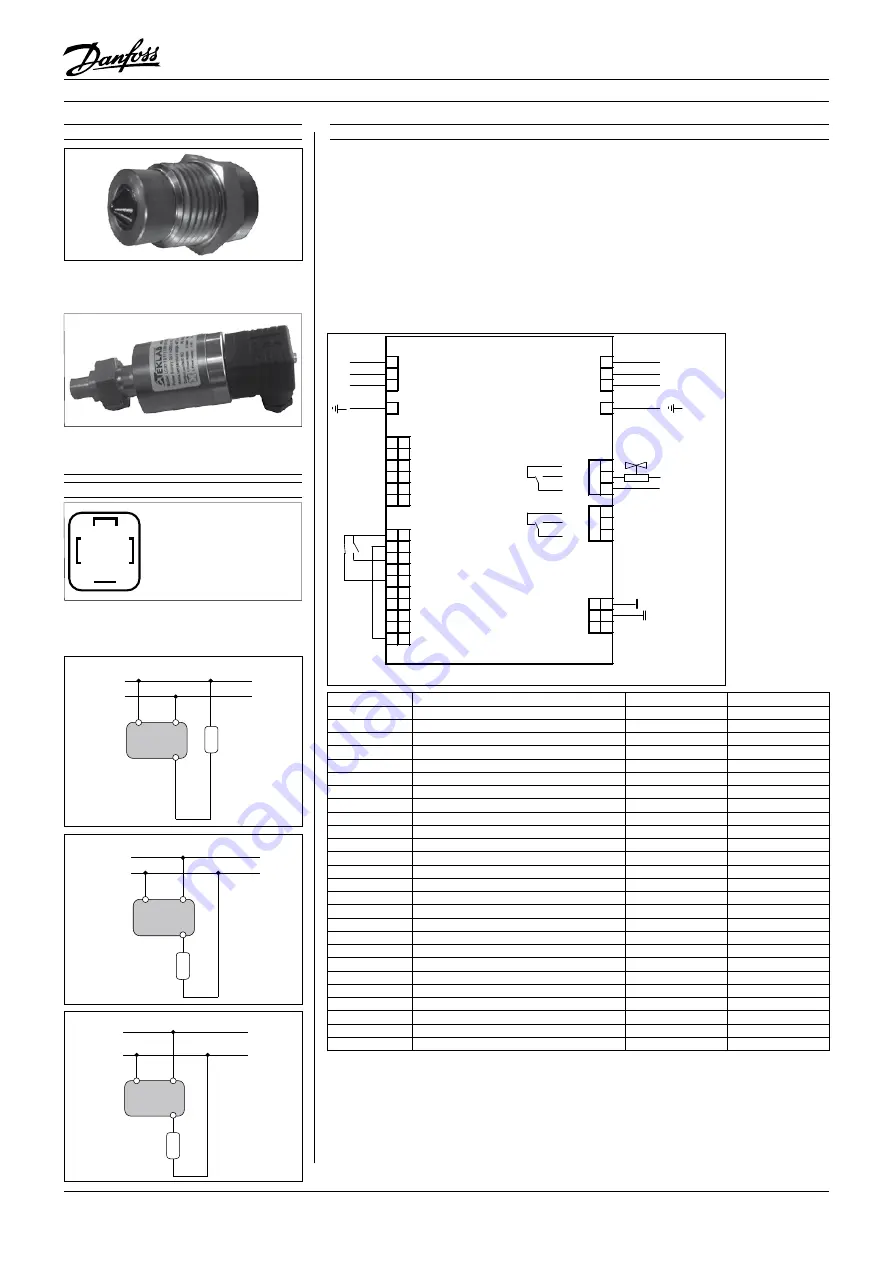
2
FRCC.EI.024.A1.02 © Danfoss Commercial Compressors 10/12
Basic connections
- Depending on the frequency converter
version, the physical position of individual
connectors may differ from below diagram.
- Always make sure that the compressor termi-
nals T1, T2, T3 are connected to the frequency
converter terminals 96, 97, 98 respectively.
- The compressor motor cable must be shielded
and the armoured part must be connected to
ground on both cable ends; at the side of the
compressor and at the side of the frequency
converter.
- Use an EMC cable gland for cable installation and
perfect grounding; The metallic terminal box of
the compressor has a paint-free surface around
the connection hole for better conductivity.
- A low pressure safety switch is mandatory
to avoid compressor vacuum operation.
- At start-up, verify that the compressor rotates
in the right direction and pumps.
230 V or 24V
~
2 A max
R
E
LA
Y
1
L1
91
L1
W
98
T3
L2
92
L2
V
97
T2
L3
93
L3
U
96
T1
95
PE
PE
99
39 39 Ana out COM
42 42 Ana out +
50 50 Ana out +10 V
NC
03
53 53 Ana in 0 ± 10 V
NO
02
54 54 Ana in 0 ± 10 V
COM
01
55 55 Ana in COM
NC
06
NO
05
12 12 +24V
COM
04
13 13 +24V
18 18 Dig in
19 19 Dig in
27 27 Dig in/out
29 29 Dig in/out
32 32 Dig in
N- RS485 69 69
33 33 Dig in
P+ RS485 68 68
20 20 Dig in COM
COM RS485 61 61
37 37 Dig in
R
E
LA
Y
2
C
D
S3
03
Legends:
Ana: Analogue
Dig: Digital
in:
Input
out: Output
COM: Common
NC: Normally-closed
NO: Normally-open
Open loop
Process loop
91, 92, 93:
3 Phase mains input
X
X
95:
Earth
X
X
39, 42
Analogue output
-
-
50:
Analogue output
-
-
53:
PLC+ (0 to 10 V)
X
-
54:
Sensor -
-
X
55:
PLC-
X
-
12:
HP/LP switch
X
X
12:
External On/Off (NO)
X
X
13:
Factory bridged to 37
X
X
13:
-
X
18:
External On/Off (NO)
X
X
19:
Digital input
-
-
27:
HP/LP switch (NC) / safety devices
X
X
29:
Digital input/output
-
-
32, 33
Digital input
-
-
20:
Digital input Common
-
-
37:
Factory bridged to 13
X
X
98:
To compressor terminal T3
X
X
97:
To compressor terminal T2
X
X
96:
To compressor terminal T1
X
X
99:
To compressor earth connection
X
X
02, 01:
Relay 1 to oil solenoid valve
X
X
06, 05, 04:
Relay 2
-
-
69, 68:
RS485 Bus
-
-
61:
RS485 Bus Common
-
-
The CDS303 frequency converter is factory pre-
set with parameters for the
open loop
control
principle. The
process loop
control principle
can be selected by changing parameters in the
«Quick menu».
Open loop
:
0 - 10 V control
Frequency converter in slave mode
Process loop:
4 - 20 mA control
Frequency converter under own PID controller
Oil level switch assembly
Electrical connections / Wiring
Install the screw-in optical part on oil level
switch port. (Factory preset for manifold version
VZH compressor.)
3
1
4
2
1: Power supply wire
2: Power supply wire
3: Output wire
4: Not used
Install the electrical part on optical part. Make
sure the cable outlet downside vertically
see at the correct diagram corresponding
to different power supply models for proper
wiring
1
OVDC
24VDC
2
3
Sensor
External
Load / Relay
24VDC MODEL
1
OVAC
24VAC
2
3
Sensor
External
Load / Relay
24VAC MODEL
1
N
L
2
3
Sensor
External
Load / Relay
230VAC MODEL
- : Optional connection
X : Mandatory connection
Instructions