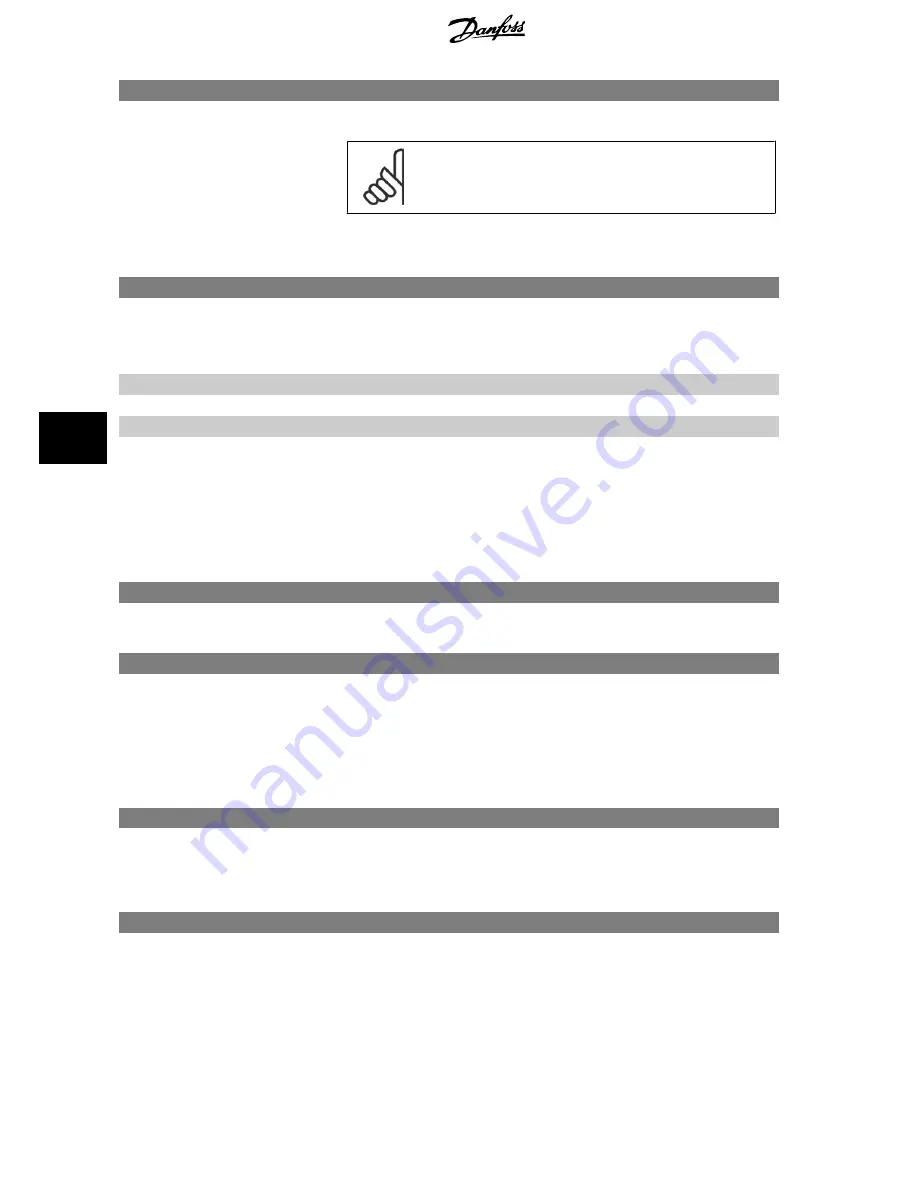
1-16 Brake Time
Range:
Function:
1 sec*
[1 - 30 secs]
Sets the duration for DC injection during a braking stop.
NB!
Parameter 1-16 is used in conjunction with Par. 1-11. See
Brake
for details.
7.6 Protection
2-1 Phase Sequence
Option:
Function:
Selects which phase sequences the soft starter will allow at a start. During its pre-start checks, the
starter examines the sequence of the phases at its input terminals and trips of the actual sequence
does not match the selected option.
Any sequence
*
Positive only
Negative only
7.6.1 Current Imbalance
The MCD 500 can be configured to trip if the currents on the three phases vary from each other by more than a specified amount. The imbalance is
calculated as the difference between the highest and lowest currents on all three phases, as a percentage of the highest current.
Current imbalance detection is desensitised by 50% during starting and soft stopping.
2-2 Current Imbalance
Range:
Function:
30%*
[10% - 50%]
Sets the trip point for current imbalance protection.
2-3 Current Imbal Dly
Range:
Function:
3 secs*
[0:00 - 4:00 (min:secs)]
Slows the MCD 500's response to current imbalance, avoiding trips due to momentary fluctuations.
7.6.2 Undercurrent
The MCD 500 can be configured to trip if the average current of all three phases drops below a specified level while the motor is running.
2-4 Undercurrent
Range:
Function:
20%*
[0% - 100%]
Sets the trip point for undercurrent protection, as a percentage of motor full load current. Set to a
level between the motor's normal working range and the motor's magnetising (no load) current
(typically 25% to 35% of full load current). A setting of 0% disables undercurrent protection.
2-5 Undercurrent Dly
Range:
Function:
5 secs*
[0:00 - 4:00 (min:secs)]
Slows the MCD 500's response to undercurrent, avoiding trips due to momentary fluctuations.
7.6.3 Instantaneous Overcurrent
The MCD 500 can be configured to trip if the average current of all three phases exceeds a specified level while the motor is running.
7 Programming
MCD 500 Operating Instruction
62
MG.17.K2.02 - VLT
®
is a registered Danfoss trademark
7