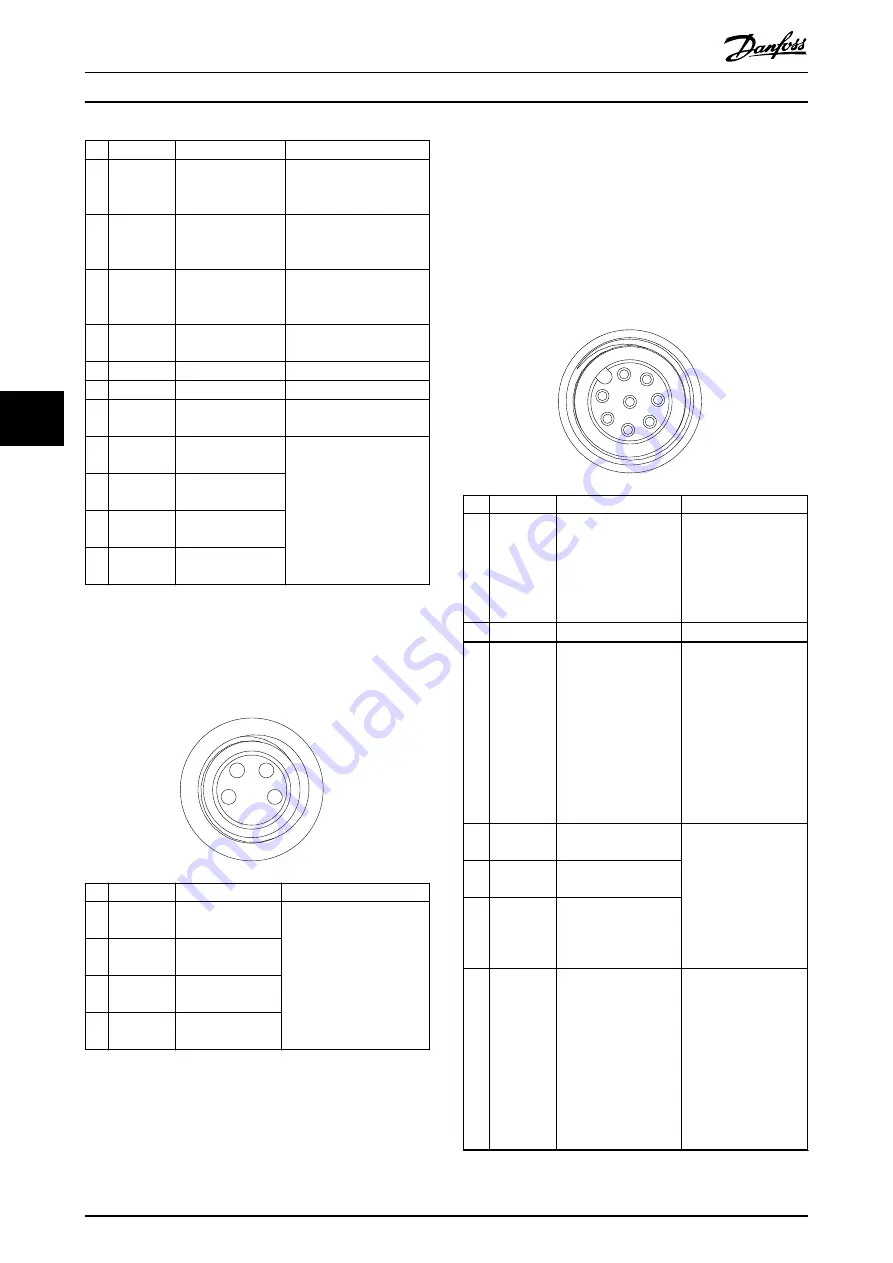
Pin Description Notes
Rating/parameter
A
UDC–
Negative DC mains
supply
Operating voltage:
Negative DC supply
(maximum –15 A)
B
UDC+
Positive DC mains
supply
Operating voltage:
Positive DC supply
(maximum 15 A)
C
AUX+
Auxiliary supply
24–48 V DC, 15 A
Absolute maximum
55 V DC
D
AUX–
Auxiliary supply
ground
15 A
PE PE
PE connector
15 A
2
STO+
Safety supply
24 V DC ±10%, 1 A
3
STO–
Safety supply
ground
1 A
5
TD+
Positive Ethernet
transmit
According to standard
100BASE-T
6
RD+
Positive Ethernet
receive
7
TD–
Negative Ethernet
transmit
8
RD–
Negative Ethernet
receive
Table 6.2 Pin Assignment of X1 and X2 Hybrid Connectors (M23)
X3: 3
rd
Ethernet connector (M8, 4 pole)
The advanced servo drive has an additional fieldbus port
(M8) for connecting a device that communicates via the
selected fieldbus.
130BE435.10
1
2
3
4
Pin Description Notes
Rating/parameter
1
TD+
Positive Ethernet
transmit
According to standard
100BASE-T
2
RD+
Positive Ethernet
receive
3
TD–
Negative Ethernet
transmit
4
RD–
Negative Ethernet
receive
Illustration 6.8 Pin Assignment of X3 3
rd
Ethernet Connector
(M8, 4 pole)
X4: M12 I/O and/or encoder connector (M12, 8-pole)
The M12 I/O and/or encoder connector is available on the
advanced servo drive and can be used or configured as:
•
Digital output
•
Digital input
•
Analog input
•
24 V supply
•
External encoder interface (SSI or BiSS).
130BE433.10
1 8
2
3
4
5
6
7
Pin Description Notes
Rating/parameter
1
Digital
output
Switched 24 V as
digital output or
supply (24 V/150 mA)
Nominal voltage
24 V
±
15%
Maximum current
150 mA
Maximum switching
frequency 100 Hz
2
Ground
Ground isolated
–
3
Input 1
Analog/Digital input
Digital input:
Nominal voltage 0–
24 V
Bandwidth:
≤
100 kHz
Analog input:
Nominal voltage 0–
10 V
Input impedance
5.46 k
Ω
Bandwidth:
≤
25 kHz
4
/SSI CLK
Negative SSI/BiSS
clock out
SSI:
Bus Speed: 0.5 Mbit
with 25 m cable
BiSS:
Fulfills the RS485
specification.
Maximum cable length
(SSI & BiSS): 25 m
5
SSI DAT
Positive SSI/BiSS data
in
6
SSI CLK
Positive SSI/BiSS clock
out
7
Input 2
Analog/Digital input
Digital input:
Nominal voltage 0–
24 V
Bandwidth:
≤
100 kHz
Analog input:
Nominal voltage 0–
10 V
Input impedance
5.46 k
Ω
Bandwidth:
≤
25 kHz
Specifications
VLT
®
Integrated Servo Drive ISD
®
510 System
56
Danfoss A/S © 08/2017 All rights reserved.
MG36C102
6
6