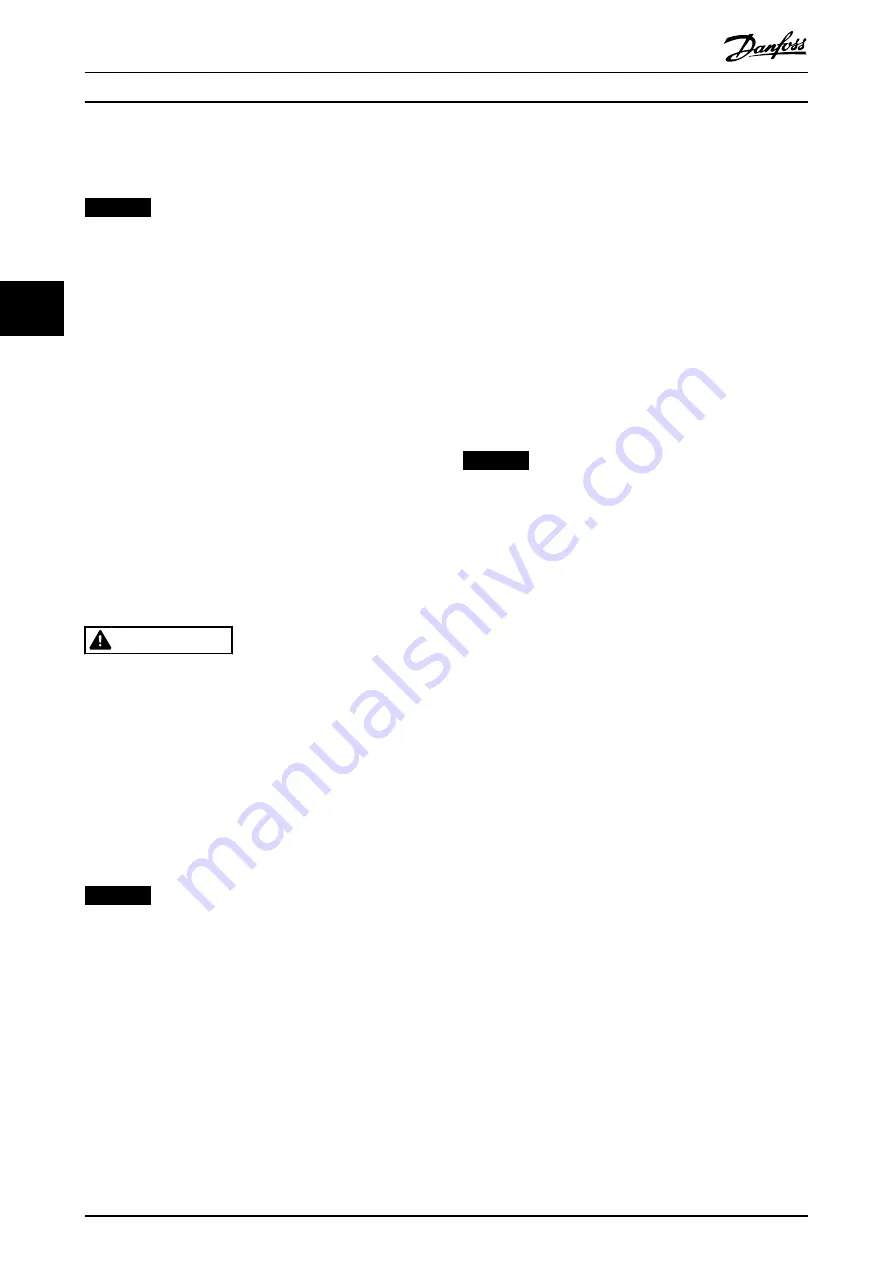
balance of electrical power. It compares the motor charac-
teristics with the data entered in
parameters 1-20
to
1-25
.
NOTICE
If warnings or alarms occur, see
Some motors are unable to run the complete version of
the test. In that case, or if an output filter is connected
to the motor, select
[2] Enable reduced AMA
.
For best results, run this procedure on a cold motor.
1.
Press [Main Menu].
2.
Select
1-** Load and Motor
and then press [OK].
3.
Select
1-2* Motor Data
and then press [OK].
4.
Select
parameter 1-29 Automatic Motor Adaptation
(AMA)
and then press [OK].
5.
Select
[1] Enable complete AMA
and then press
[OK].
6.
Press [Hand On] and then [OK].
The test runs automatically and indicates when it
is complete.
4.5 Testing Before System Startup
WARNING
MOTOR START
Failure to ensure that the motor, system, and any
attached equipment are ready for start can result in
personal injury or equipment damage. Before start:
•
Ensure that equipment is safe to operate under
any condition.
•
Ensure that the motor, system, and any
attached equipment are ready for start.
4.5.1 Motor Rotation
NOTICE
If the motor runs in the wrong direction, it can damage
equipment. Before running the motor, check its direction
of rotation by briefly running the motor. Run the motor
at either 5 Hz or the minimum frequency set in
parameter 4-12 Motor Speed Low Limit [Hz]
as follows:
1.
Press [Hand On].
2.
Move the cursor to the left of the decimal point
by using the left arrow key and then enter an
RPM value that causes the motor to rotate slowly.
3.
Press [OK].
4.
If the motor rotation is wrong, change
parameter 1-06 Clockwise Direction
to
[1] Inverse
.
4.5.2 Encoder Rotation
Only check encoder rotation if encoder feedback is used.
For more information on the encoder option, refer to the
option manual.
1.
Select
[0] Open loop
in
parameter 1-00 Configu-
ration Mode
.
2.
Select
[1] 24 V encoder
in
parameter 7-00 Speed
PID Feedback Source
.
3.
Press [Hand On].
4.
Press [
►
] for positive speed reference
(
parameter 1-06 Clockwise Direction
at
[0] Normal
).
5.
Check in
parameter 16-57 Feedback [RPM]
that the
feedback is positive.
NOTICE
NEGATIVE FEEDBACK
If the feedback is negative, the encoder connection is
wrong. Use either
parameter 5-71 Term 32/33 Encoder
Direction
or
parameter 17-60
to inverse the direction, or
reverse the encoder cables.
Parameter 17-60 Feedback
Direction
is only available with the VLT
®
Encoder Input
MCB 102 option.
4.5.3 Local Control Test
Perform the local control test as follows:
1.
Press [Hand On] to provide a local start command
to the drive system.
2.
Accelerate the unit by pressing [
▲
] until full
speed is reached. Moving the cursor to the left of
the decimal point provides quicker input changes.
3.
Note any acceleration problems.
4.
Press [Off]. Note any deceleration problems.
If acceleration or deceleration problems occur, see
. To reset the drive system after
a trip, clear all faults and then manually reset the system.
For a list of warnings and alarms, see
.
Commissioning
VLT
®
Parallel Drive Modules
20
Danfoss A/S © 08/2017 All rights reserved.
MG37L202
4
4