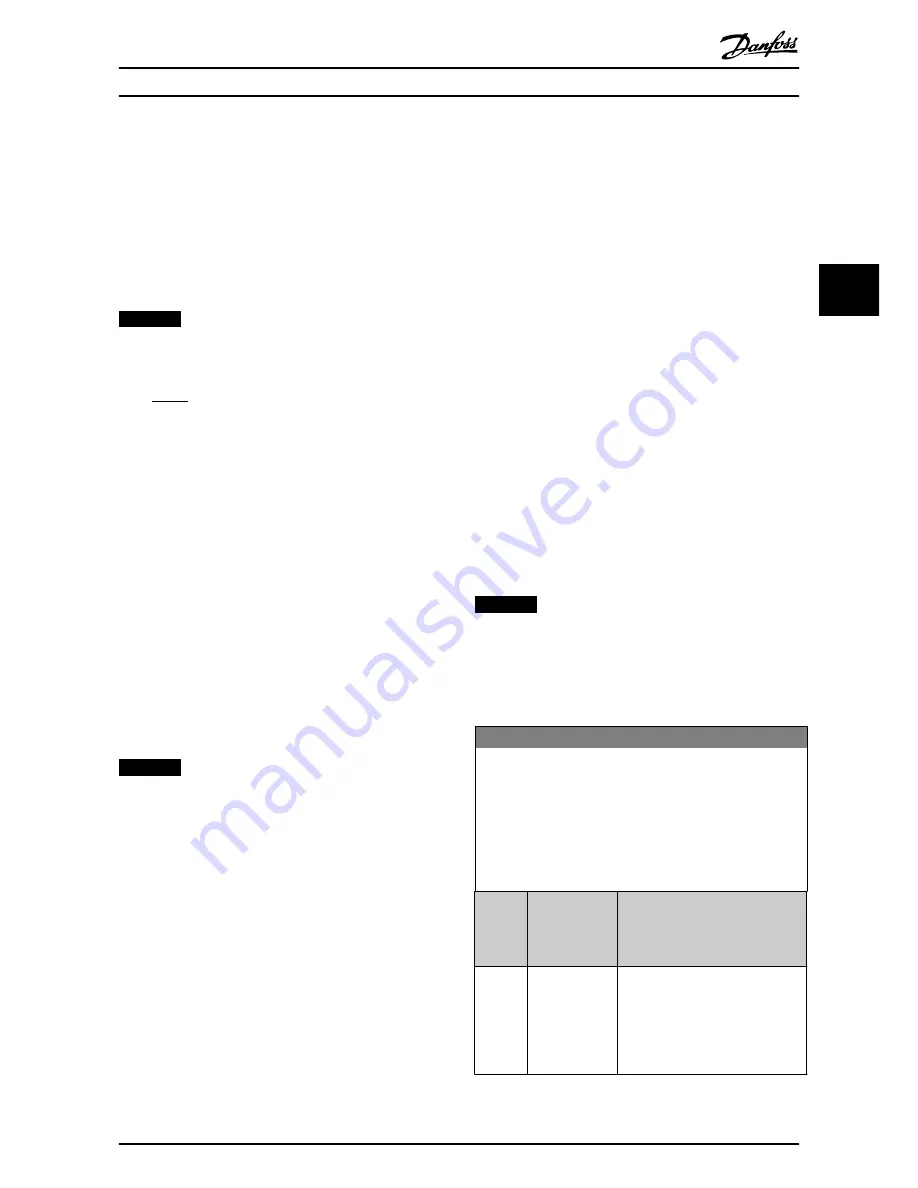
Operation below the minimum frequency for more than
60 s within a period of 600 s triggers
Alarm 166 ATEX ETR
freq.lim.alarm
. The frequency converter trips.
4.3.4 Maximum Motor Frequency
Do not exceed the maximum allowable output frequency.
The motor data sheet or nameplate shows the maximum
permissible value.
NOTICE
This value can be reduced for long motor cables, sine-
wave filter, or reduced supply voltage.
f
max
=
U
n
− U
loss
U
n
x f
n
Example
:
Nominal voltage = 480 V
Nominal frequency = 50 Hz
Voltage loss due to supply voltage of 450 V =
30 V
Resulting maximum frequency = 47 Hz
Use the result from the equation as the value set in
4-19 Max Output Frequency
.
4.3.5 Minimum Switching Frequency
Thermal motor losses increase with lower switching
frequencies. Ensure that the frequency converter switching
frequency does not drop below the value stated by the
motor manufacturer.
NOTICE
It is mandatory to compare the minimum switching
frequency requirement of the motor to the minimum
switching frequency of the frequency converter, which is
the default value in
14-01 Switching Frequency
. If the
frequency converter does not meet this requirement, use
a sine-wave filter.
4.3.6 Disable Protection Mode
In
protection mode
, the frequency converter derates the
switching frequency below the default in
14-01 Switching
Frequency
. For example, if the default value is 3 kHz, it can
derate down to 2.5 kHz, depending on EEPROM. Therefore,
disable
protection mode
in
14-26 Trip Delay at Inverter Fault
.
More information about derating can be found in the
section Derating
in the frequency converter design guide.
4.3.7 Safe Torque Off Functionality
The desired Safe Torque Off functionality is specified in
parameter 5-19 Terminal 37 Safe Stop
. When a VLT
®
PTC
Thermistor Card MCB 112 is mounted, select 1 of the PTC
options to get the full benefit from the alarm handling.
Options
[4] PTC 1 Alarm
and
[5] PTC 1 Warning
are relevant
when the MCB 112 is the only interrupt device using STO.
Options
[6] PTC 1 & Relay A
to
[9] PTC 1 & Relay W/A
are
relevant when other safety sensors are also connected to
STO.
•
Alarm: The frequency converter coasts. Reset the
alarm manually (via bus, digital I/O, or by pressing
[Reset]). Auto reset does not apply here. For more
details, see
[4] PTC 1 Alarm
in
parameter 5-19 Terminal 37 Safe Stop
.
•
Warning: The frequency converter coasts, but
resumes operation when STO and the DI from
X44/10 are disabled. For more details, see
[5] PTC
1 Warning
in
parameter 5-19 Terminal 37 Safe Stop
.
Configuring a digital input in parameter group
5-1* Digital
Inputs
makes it possible to give a warning/alarm that
specifies what triggered the Safe Torque Off.
NOTICE
When selecting warning instead of alarm, automatic
restart is enabled. See
Installation in Combination with
VLT
®
PTC Thermistor Card MCB 112
in the
VLT
®
Frequency
Converters - Safe Torque Off Operating Instructions
.
Safe Torque Off-related Parameter
5-19 Terminal 37 Safe Stop
To configure the Safe Torque Off functionality, set this parameter.
A warning message makes the frequency converter coast the
motor and enables the automatic restart. An alarm message
makes the frequency converter coast the motor and requires a
manual restart (via a fieldbus, digital I/O, or by pressing [Reset]
on the LCP). When the MCB 112 is mounted, configure the PTC
options to get the full benefit from the alarm handling.
Option:
Function:
[1]
Safe Stop Alarm Coasts the frequency converter
when Safe Torque Off is activated.
Manual reset from LCP, digital input,
or fieldbus.
[3]
Safe Stop
Warning
Coasts the frequency converter
when Safe Torque Off is activated
(terminal 37 off). When Safe Torque
Off circuit is re-established, the
frequency converter continues
without manual reset.
Commissioning
Operating Instructions
MG33V302
Danfoss A/S © 01/2015 All rights reserved.
15
4
4