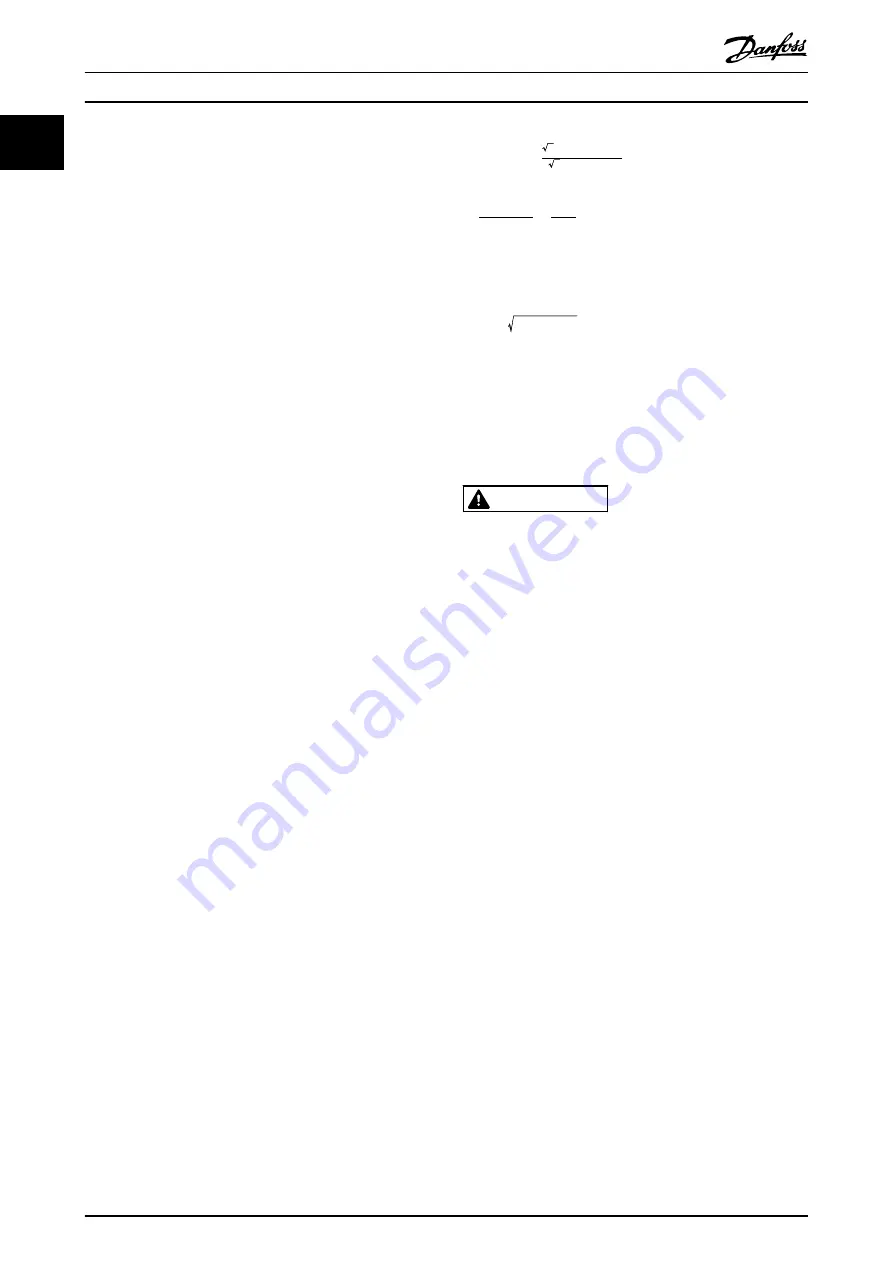
Slip Compensation
The frequency converter compensates for the motor slip
by giving the frequency a supplement that follows the
measured motor load keeping the motor speed almost
constant.
Smart Logic Control (SLC)
The SLC is a sequence of user defined actions executed
when the associated user defined events are evaluated as
true by the Smart Logic Controller. (Parameter group
13-**
Smart Logic Control (SLC)
.
STW
Status Word
FC Standard Bus
Includes RS-485 bus with FC protocol or MC protocol. See
8-30 Protocol
.
THD
Total Harmonic Distortion states the total contribution of
harmonic.
Thermistor
A temperature-dependent resistor placed where the
temperature is to be monitored (frequency converter or
motor).
Trip
A state entered in fault situations, e.g. if the frequency
converter is subject to an over-temperature or when the
frequency converter is protecting the motor, process or
mechanism. Restart is prevented until the cause of the
fault has disappeared and the trip state is cancelled by
activating reset or, in some cases, by being programmed
to reset automatically. Trip may not be used for personal
safety.
Trip Locked
A state entered in fault situations when the frequency
converter is protecting itself and requiring physical
intervention, e.g. if the frequency converter is subject to a
short circuit on the output. A locked trip can only be
cancelled by cutting off mains, removing the cause of the
fault, and reconnecting the frequency converter. Restart is
prevented until the trip state is cancelled by activating
reset or, in some cases, by being programmed to reset
automatically. Trip may not be used for personal safety.
VT Characteristics
Variable torque characteristics used for pumps and fans.
VVC
plus
If compared with standard voltage/frequency ratio control,
Voltage Vector Control (VVC
plus
) improves the dynamics
and the stability, both when the speed reference is
changed and in relation to the load torque.
60
°
AVM
Switching pattern called 60
°
Asynchronous Vector
Modulation (
14-00 Switching Pattern
).
Power Factor
The power factor is the relation between I
1
and I
RMS
.
Power factor =
3
x U x I1 cosϕ
3
x U x IRMS
The power factor for 3-phase control:
= I1 x cosϕ1
IRMS
=
I1
IRMS
since cosϕ1 = 1
The power factor indicates to which extent the frequency
converter imposes a load on the mains supply.
The lower the power factor, the higher the I
RMS
for the
same kW performance.
IRMS = I1
2 + I
5
2 + I
7
2 + .. + In2
In addition, a high power factor indicates that the different
harmonic currents are low.
The frequency converters' built-in DC coils produce a high
power factor, which minimizes the imposed load on the
mains supply.
1.3 Safety Precautions
WARNING
The voltage of the frequency converter is dangerous
whenever connected to mains. Incorrect installation of the
motor, frequency converter or fieldbus may cause death,
serious personal injury or damage to the equipment.
Consequently, the instructions in this manual, as well as
national and local rules and safety regulations, must be
complied with.
Safety Regulations
1.
Always disconnect mains supply to the frequency
converter before carrying out repair work. Check
that the mains supply has been disconnected and
observe the discharge time stated in
before removing motor and mains supply.
2.
[Off/Reset] on the LCP does not disconnect the
mains supply and must NOT be used as a safety
switch.
3.
The equipment must be properly earthed, the
user must be protected against supply voltage
and the motor must be protected against
overload in accordance with applicable national
and local regulations.
4.
The earth leakage current exceeds 3.5 mA.
5.
Protection against motor overload is not included
in the factory setting. If this function is desired,
set
1-90 Motor Thermal Protection
to data value
[4]
ETR trip 1
or data value
[3] ETR warning 1
.
6.
The frequency converter has more voltage
sources than L1, L2 and L3, when load sharing
(linking of DC intermediate circuit). Check that all
voltage sources have been disconnected and that
the necessary time has elapsed before
commencing repair work.
Introduction
VLT
®
AutomationDrive FC 360 Design Guide
8
MG06B202 - VLT
®
is a registered Danfoss trademark
1
1