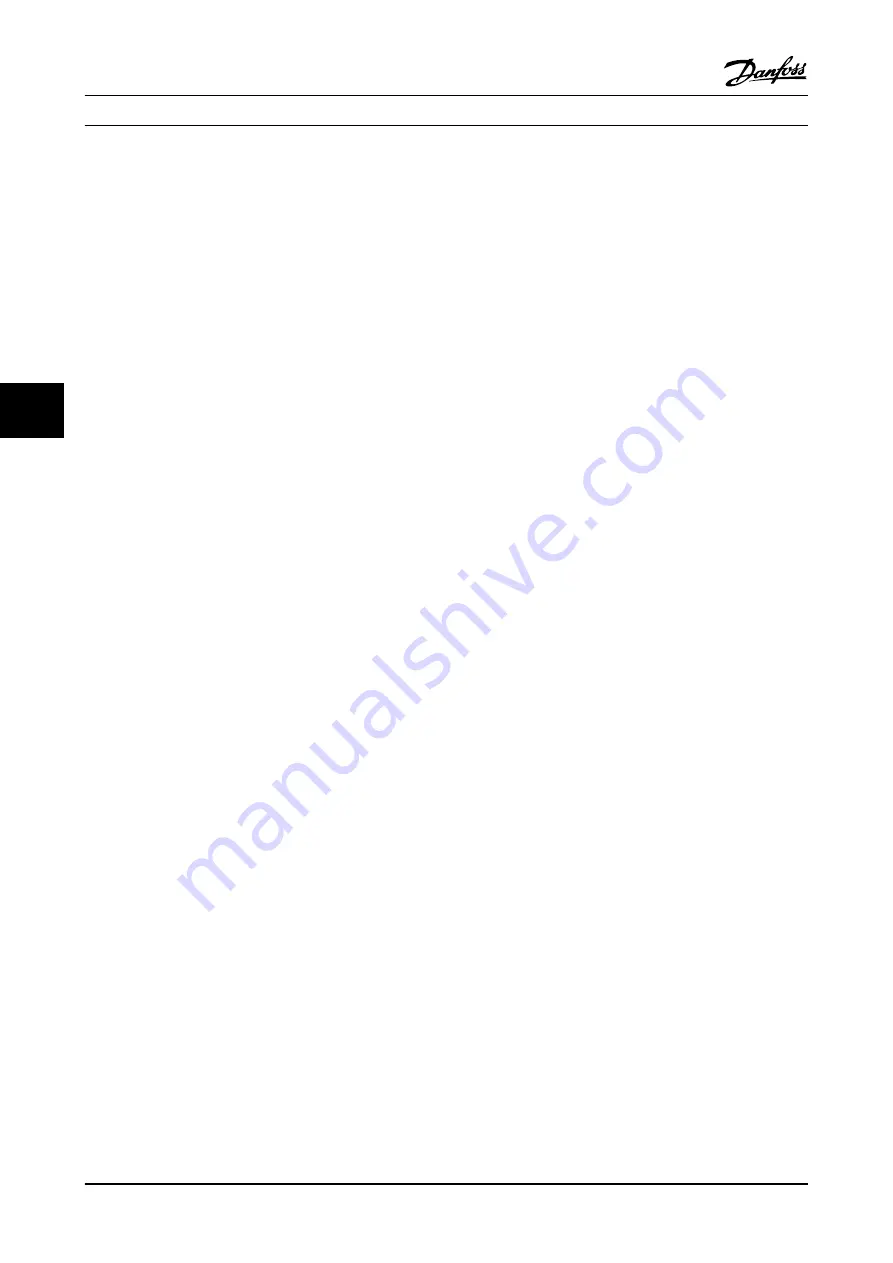
If the 10 volts is present proceed with checking the
individual inputs as follows.
2.
Connect the (-) negative meter lead to reference
terminal 55.
3.
Connect the (+) positive meter lead to desired
terminal 53 or 54.
For analog input terminals 53 and 54, a DC voltage
between 0 and +10 V DC should be read to match the
analog signal being sent to the filter. Or a reading of 0.9 to
4.8 V DC corresponds to a 4 to 20 mA signal.
Note that a (-) minus sign preceding any reading above
indicates a reversed polarity. In this case, reverse the
wiring to the analog terminals.
6.3.7 Line Power Resonance Test
Resonances can occur in systems when the filter is able
transfer energy between itself and other energy storage
devices with no damping. If often occurs between a filter
and other non-tuned capacitor banks. In case of resonance
faults, investigate if the grid contains other capacitor banks
and disconnect these, if possible. It might also be
advisable to de-tune the capacitors by adding reactors.
1.
Check the CT installation wiring.
2.
Check the voltage imbalance value. It should be
below 3%.
3.
Mount the CT shorter on all three CT inputs on
the CT input terminal. Give the active filter a run
command. If Alarm 7, DC overvoltage, occurs, go
to the troubleshooting procedure for Alarm 7. If
no Alarm 7 occurs, go to the next step.
4.
Remove CT short lugs.
5.
Program the filter for the selective harmonic
compensation mode (
300-00 Harmonic Cancel-
lation Mode
harmonic selection mode) and
program the filter for compensation of the 5th
and 7th harmonics only (
300-30 Compensation
Points
, compensation points for 5th and 7th
harmonics set to zero, and other harmonics to
the maximal value).
6.
Give the filter a run command and observe
whether the voltage distortion is reduced in the
5th and 7th harmonics. If not, check CT input/
installation and configuration for faults again.
7.
Program step by step the filter for compensation,
other harmonics, and monitor the AC output filter
current indicated on the LCP or by direct
measurements with a current probe. A high
current indicates possible resonance points in the
power supply. Ground these points by changing
the order of compensated harmonics and disable
by programming the active filter.
6.3.8 Control Card Digital Inputs/Outputs
Test
Control card test digital inputs/outputs test
Use the following procedure to test the control card, and
replace the control card if a problem is found.
1.
Power the control card from a 24 V DC backup.
Do not power the active filter from AC line
voltage.
2.
Program the digital inputs for PNP using
parameter 5-00.
3.
Verify the voltage across T12 and T20 is 24V DC
using a multi-meter.
4.
Verify that T32 is “0” using parameter 16-60.
5.
Use a jumper wire to connect T12 and T32.
6.
Verify that T32 is “1” using parameter 16-60.
7.
Remove the jumper wire.
8.
Verify that T33 is “0” using parameter 16-60.
9.
Use a jumper wire to connect T12 and T33.
10.
Verify that T33 is “1” using parameter 16-60.
11.
Remove the jumper wire.
12.
Change parameter 5-00 back to the previous
value, if changed earlier.
6.4 After Repair Tests
After any repair to a filter or after any testing of a filter
suspected of being faulty, follow this procedure to ensure
that all circuitry is functioning properly before returning
the unit to operation.
1.
Perform visual inspection procedures as described
in
.
2.
Perform the static test procedures to ensure that
the unit is safe to start.
3.
Apply AC power to the unit.
4.
Copy parameter settings to the LCP memory
0-50 LCP Copy
for backup.
5.
Program the filter according to CT installation in
the following parameters: Location (
300-26 CT
Placement
), CT Primary Voltage (
300-22 CT
Nominal Voltage
).
Test Procedures
VLT Advanced Active Filter AAF006 D and E Frames Service Manual
6-8
MG90Z122 - VLT
®
is a registered Danfoss trademark
6
6