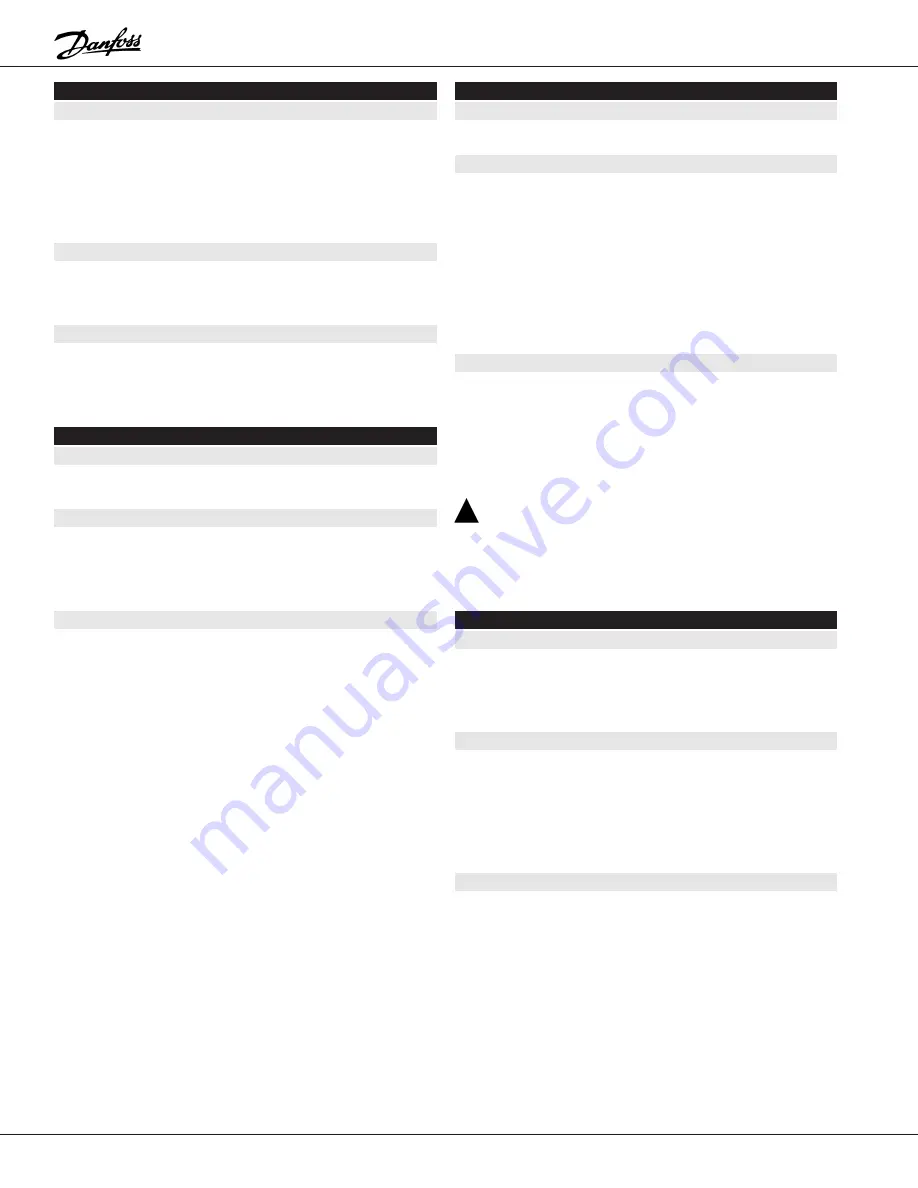
VLT
®
Series 3500
64
★
= ROM default setting.
✔
= Normal Danfoss setup. Text in ( ) = display text. Figures in [ ] are used when communicating with the bus.
105 Motor Frequency (f
N
)(MOTOR FREQ)
Value:
50 Hz (50 Hz)
[0]
✔
60 Hz (60 Hz)
[1]
87 Hz (87 Hz)
[2]
100 Hz (100 Hz)
[3]
★
Depends on unit
Function:
Choose the frequency that corresponds to the rated motor
frequency.
Description of choice:
Consult factory before selecting a motor frequency other
than the rated motor frequency. This is also chosen in
Quick Set Up Menu step 3.
107 Motor Current (MOTOR CURR)
Value:
Full load amps from motor nameplate
Function:
It is important to specify the rated motor current because it
is used in part to calculate torque and thermal motor protec-
tion, (ETR),
Description of choice:
The rated motor current, which can be seen from the motor
nameplate, must be entered. This is also chosen in Quick
Set Up Menu step 2.
109 Start Voltage (START VOLT)
Value:
0.0 to (U
M,N
+ 10%)
Function:
When
Constant torque start (CT) has been chosen in pa-
rameter 100, the start voltage can be adjusted. By increas-
ing the start voltage, a high start torque can be obtained.
Small motors (<1 HP) normally require a high start voltage.
When motors are connected in parallel, it may be desir-
able to increase the starting voltage.
When constant torque start is not selected, this value has
no effect on the operation of the drive.
Description of choice:
The lowest possible value that provides reliable motor start-
ing torque is desired.:
1. Select a value that enables starting with the given load.
2. Reduce this value until starting up with the given
load is barely possible, then increase slightly.
U
M,N
= rated motor voltage.
WARNING
!
If the start voltage is set too high, the motor may overheat
or the drive may fault trip. Do not set any higher than re-
quired for reliable starting.
114 Feedback Signal (FEEDBACK T)
Value:
Voltage (VOLTAGE)
[0]
★
Current (CURRENT)
[1]
Pulses (PULSES)
[2]
Function:
This parameter allows a choice of process feedback signal
in a closed loop system, as chosen in parameter 101. It has
no effect if parameter 101 is set to OPEN LOOP.
For further information, see the section on the PID control-
ler.
Description of choice:
If a PID controller is used, one of the inputs on terminal 17
(parameter 401), terminal 53 (parameter 412) or terminal
60 (parameter 413) must be used for the feedback signal.
The same type of signal cannot be the reference signal.