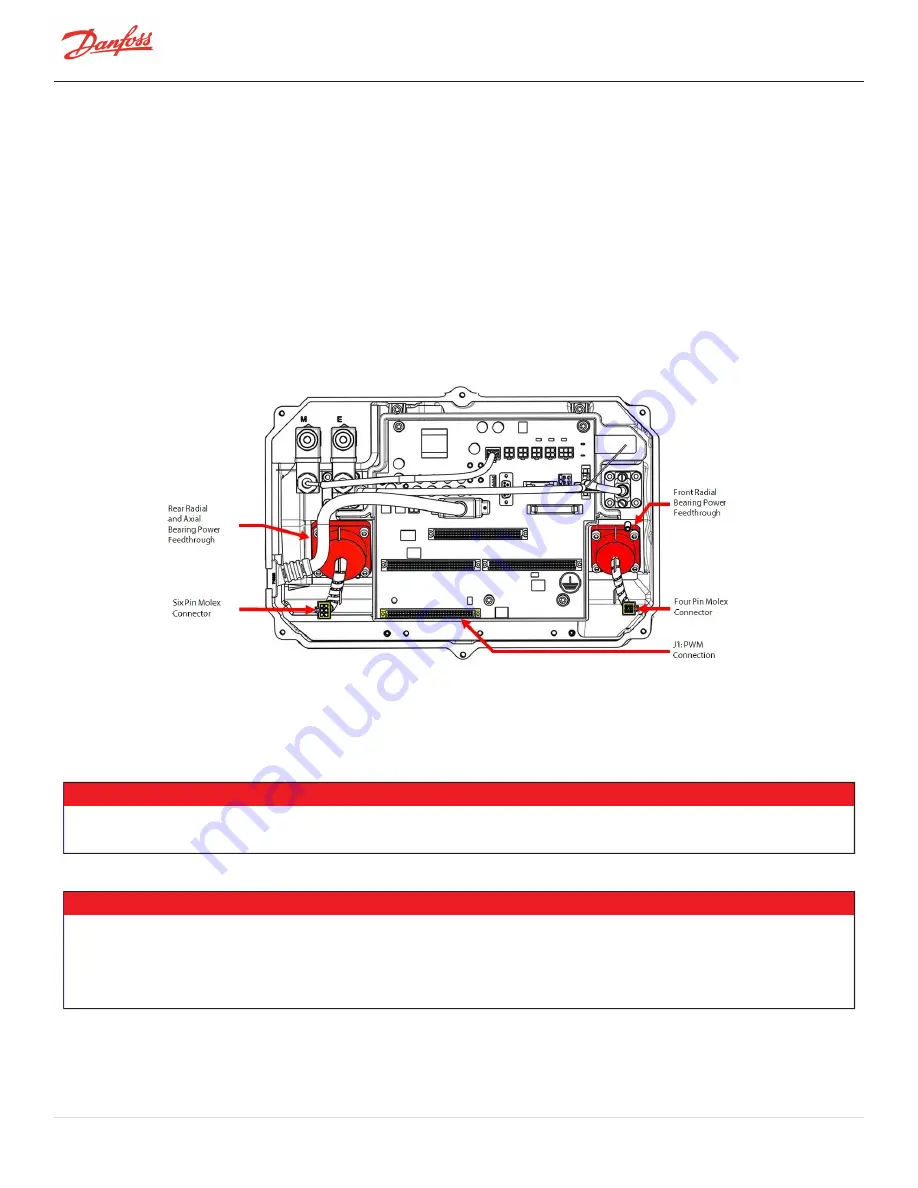
4.29 Magnetic Bearings
4.29.1 Magnetic Bearings Function
The compressor shaft and impellers levitate during operation and float on a magnetic cushion created by the
magnetic bearings. Permanent magnets do most of the work and electromagnets are used for trimming the shaft
position within 0.0003” (7 microns). One axial (Z axis) and two radial (X & Y axis) magnetic bearings are used to
maintain shaft position. Centered rotation is instantaneously self-corrected and maintained by the bearing control
loop. Refer to Figure 4-252 Bearing Control Signal Flow on page 226.
When not powered, the shaft is supported by carbon composite or roller touchdown bearings.
4.29.2 Magnetic Bearings Connections
PWM connectors supply power at the bearing power feedthroughs. Refer to Figure 4-255 Bearing Connections.
Figure 4-255 Bearing Connections
4.29.3 Bearing Verification
4.29.3.1 Bearing Coil Verification
• • • CAUTION • • •
Do not attempt to perform an insulation (megger) test on a component under vacuum. This can cause insulation breakdown or failure
during the testing process.
NOTE
l
To check bearing coil insulation integrity, a Mega ohm meter (e.g., Megger) set to 1KV should be used. Readings from coils
to ground should be greater than 100MΩ, and readings between coils should be greater than 100MΩ.
l
A faulty PWM Amplifier may be the result of a bearing failure and may cause a failure of the Potted DC-DC Converter
resulting in a blown F1 fuse on the Closed Top Soft Start. If a bearing coil is found to be faulty, then the PWM, Potted DC-DC
Converter, and Closed Top Soft Start F1 fuse must be verified as well.
Page 230 of 294 - M-SV-001-EN Rev. H 1/23/2023
Summary of Contents for Turbocor TT Series
Page 2: ...THIS PAGE INTENTIONALLY LEFT BLANK Page 2 of 294 M SV 001 EN Rev H 1 23 2023...
Page 14: ...Page 14 of 294 M SV 001 EN Rev H 1 23 2023 THIS PAGE INTENTIONALLY LEFT BLANK...
Page 16: ...Page 16 of 294 M SV 001 EN Rev H 1 23 2023 THIS PAGE INTENTIONALLY LEFT BLANK...
Page 18: ...Figure 1 2 New Type Code Page 18 of 294 M SV 001 EN Rev H 1 23 2023...
Page 46: ...Page 46 of 294 M SV 001 EN Rev H 1 23 2023 THIS PAGE INTENTIONALLY LEFT BLANK...
Page 250: ...Page 250 of 294 M SV 001 EN Rev H 1 23 2023 THIS PAGE INTENTIONALLY LEFT BLANK...
Page 268: ...Figure 5 3 Bearing Calibration Flow Page 268 of 294 M SV 001 EN Rev H 1 23 2023...
Page 274: ...Page 274 of 294 M SV 001 EN Rev H 1 23 2023 THIS PAGE INTENTIONALLY LEFT BLANK...
Page 286: ...Page 286 of 294 M SV 001 EN Rev H 1 23 2023 THIS PAGE INTENTIONALLY LEFT BLANK...
Page 290: ...Page 290 of 294 M SV 001 EN Rev H 1 23 2023 THIS PAGE INTENTIONALLY LEFT BLANK...
Page 292: ...Page 292 of 294 M SV 001 EN Rev H 1 23 2023 THIS PAGE INTENTIONALLY LEFT BLANK...