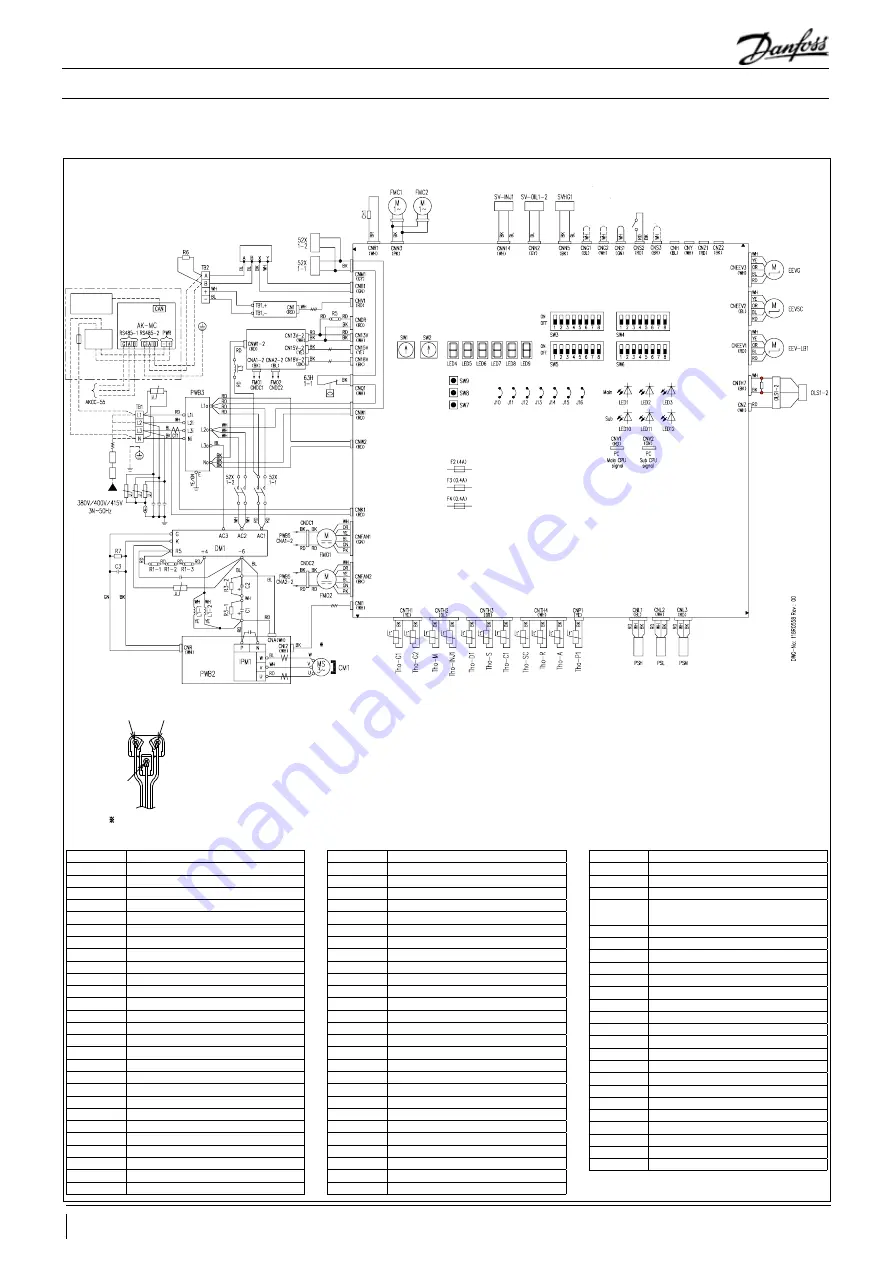
4. Installation
Wiring Diagram
Symbol
Name
C1,2
Electrolytic capacitor
C3
Filter capacitor
CH1
Crankcase heater
CM1
Compressor motor
CNA-Z
Connector
CT1
Compressor current
DM1
Diode module
EEVG
EEV for middle pressure receiver inlet
EEV-LB1
JEEV for liquid bypass
EEVSC
EEV for subcooling coil
F
Fuse
FMC1,2
Inverter cooling fan
FMO1,2
Fan motor
IPM1
intelligent power module
J10
Spare
J11,12
Power supply, voltage switching
J13
External input signal type switching
J14~16
Spare
L1-1,2
DC reactor
L3
Reactor
LED1
Main, inspection (red)
LED2
Main, normal (green)
LED3
Main, service (green)
LED4~6
7-segment LED (function display)
LED7~9
7-segment LED (data display)
LED10
Sub, normal (green)
LED 11
Sub, inspection (red)
Symbol
Name
LED 12
Sub, service (green)
OLS1-2
Oil level sensor
PSH
High pressure sensor
PSL
Low pressure sensor
PSM
Middle pressure sensor
PWB1~3,5~7
Printed wiring board
R1-1,2,3
Inrush suppression resistance
R3-1,2
Discharge resistance
R5
Drop resistance
R6
Termination resistance
R7
Filter resistance
SVHG1
Solenoid valve for hot gas bypass
SV-INJ1
Solenoid valve for gas injection
SV-OIL1-2
Solenoid valve for oil return
SW1
Compressor low pressure control setting (10s)
SW2
Compressor low pressure control setting (1s)
SW3-1~3
Spare
SW3-4
Protection start II cancel
SW3-5
Gas cooler fan control
SW3-6
Spare
SW3-7
Compressor total operation time reset
SW3-8
Spare
SW4-1~4
Model selection
SW4-5~8
Spare
SW5-1~3
For target middle pressure adjustment
SW5-4,5
Spare
SW5-6~8
Pressure check operation mode
Symbol
Name
SW6-1~3
Spare
SW6-4
Presence of subcooling suppression control
SW6-5
Oil level error/oPE display switching
SW6-6
Presence of regular inspection and
maintenance contract
SW6-7
Oil level error
Sw6-8
Spare
SW7
Data erase/write
SW8
7-segment display (1s)
SW9
7-seqment display (10s)
TB1,2
Terminal block
Tho-A
Outdoor air temp. sensor
Tho-C1
Under dome temp. sensor
Tho-D1
Discharge pipe temp. sensor
Tho-G1
Gas cooler temp. sensor 1 (inlet)
Tho-G2
Gas cooler temp. sensor 2 (outlet)
Tho-INJ1
Gas injection inlet temp. sensor 1
Tho-M
Middle pressure receiver inlet temp. sensor
Tho-P1
Power transistor temp. sensor
Tho-R
Liquid feed pipe temp. sensor
Tho-SC
Subcooling coil temp. sensor
Tho-S
Suction pipe temp. sensor
ON-OFF SW
Operation switch
52X1-1,2
Magnetic contactor for CM
63H1-1
High pressure switch
Notes
1. This drawing shows the electrical circuit of CO2 condensing unit.
2. Dotted line (----- ) shows the wiring on site.
Long dashed double-short dashed line (----- ) shows installation on site.
3. Separate signal line from power line.
4. CNG1,CNG2,CNS1,CNS2 and CNS3 are no voltage contact inputs.
If they will be used, use the attached harness for level input.
5. Output of CNH,CNY,CNZ1 and CNZ2 is 12V. Maximum current is less than 20mA (+ side (1 PIN side) is common) .
If they will be used, use the attached harness and be sure to connect to unit relay (Coil resistance of 7502 or more
provided on site).
U (red)
W (Blue)
Enlarged drawing of
compress terminals
V (White)
Ex
ter
nal output 2
Ex
ter
nal output 1
Er
ror output
Oper
ation output
Oper
ation in
tput
G
as c
ooler fan sno
w
con
tr
ol input
Multistage demand input
C
ompulsor
y oil
retun c
on
tr
ol input
ON - OFF SW
ASSLY CO2 MODULE CONTROLLER
Super Link
Adapter PCB
PWB6
User interface
MMILDS
12VDC
Power
Module controller
Circuit breaker
for cabling
Earth leakage
breaker
Power source
Inverter PCB
Compressor terminal
See enlarged view
Control PCB
PWB1
Noise filter PCB
Power PCB PWB5
Remote PCB PWB7
Ready connector
30
AB408540130380en-000102
© Danfoss | Climate Solutions | 2023.02
Application Guidelines