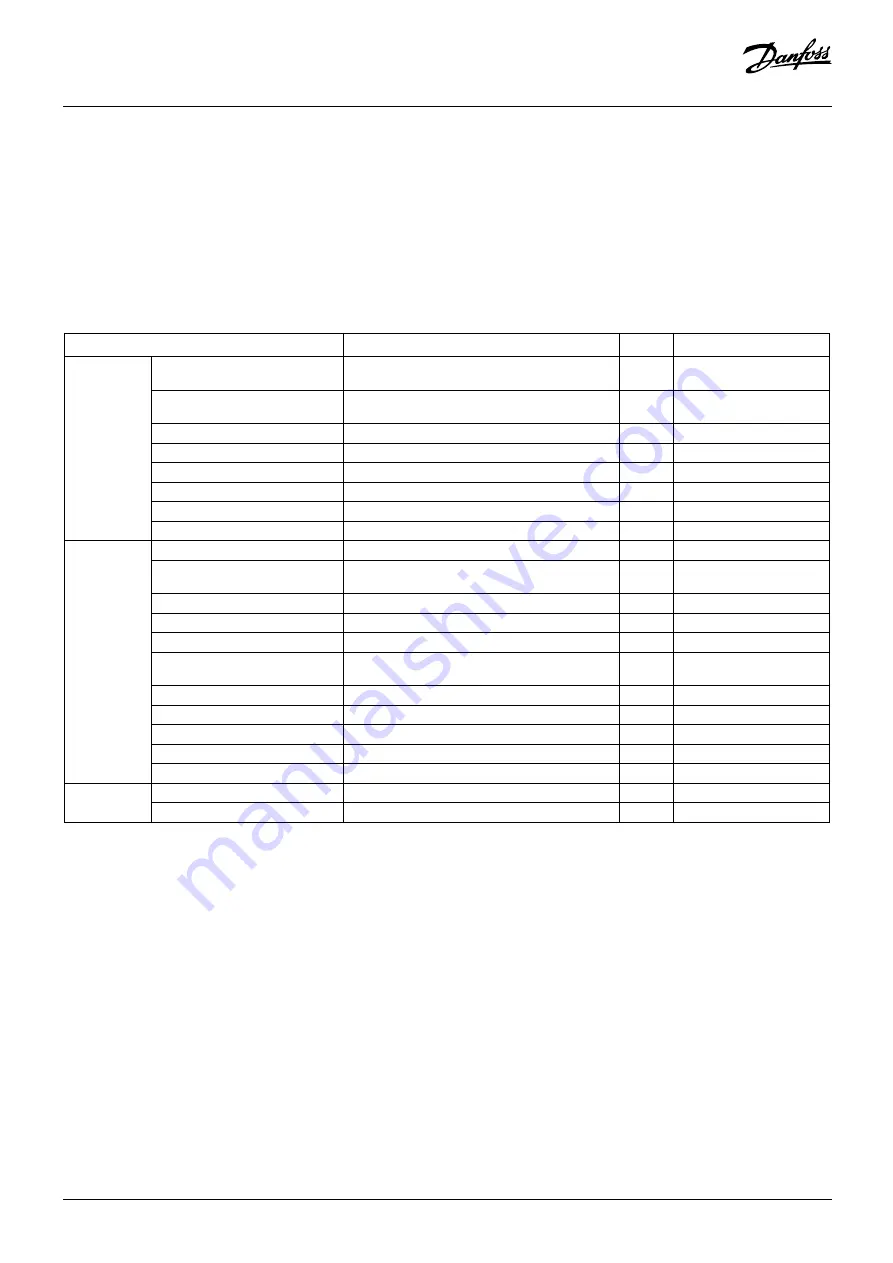
Instructions
40 | AN405821998738en-000102 - 118A5495A
© Danfoss | Climate Solutions | 2023.02 | LCA012A024
14.1. Maintenance and inspection
To personnel for daily operation and control
• The list shows contents of regular inspection and replacement guideline under general usage condition. The cycle of regular inspection is on an annual
basis and it shows estimated cycle for component replacement and repair as the replacement guideline based on the result of the regular inspection.
"Under the general usage condition" supposes 7 minutes of stop-start cicle and 5,000 running hours per year upon normal operational condition.
• Execute maintenance and inspection for load side (unit cooler and show-case) and module controller in accordance with criteria of load side and module
controller.
In case that adjustment, maintenance and inspection for load side and module controller are not adequate, there is significant harmful effect on
condensing unit.
• Condensing unit shall be utilized as putting in the system via on-site construction works like installation, refrigerant pipe work and electric work and so on.
Since lifetime for failure and operation significantly depends on degree of right and wrong on construction works, criteria of construction works
described on installation manual must be followed.
Part
Inspection
Cycle
Guide for replacement
Refrigerant
circuit parts
Compressor
High/medium/low pressure, vibration, noise,
insulation resistance, loose terminal
1
40,000 h
Air-side heat exchanger
(Gas cooler)
High/medium/low pressure, fouled fin,
discharge temperature
1
8 yr
Solenoid valve
Operation, leak, clogging
1
7 yr
Electronic expansion valve
Operation
1
7 yr
Safety valve
Whether or not there is refrigerant leakage
1
5 yr
Strainer
Strainer out-/inlet temp.
1
8 yr
Capillary tube
Contact wear, vibration
1
8 yr
Piping
Contact wear, vibration
1
8 yr
Electric
circuit parts
Relay
Operation, contact/ insulation resistance
1
8 yr
Solenoid valve, electronic expansion
valve coil
Insulation resistance
1
8 yr
Crankcase heater
Insulation resistance
1
20,000 h
Fuse
Appearance
1
8 y
PCB (Control, inverter)
Appearance
1
8 y
High pressure breaker,
pressure sensors
Contact resistance, capillary rubbing
1
8 y
Terminal block
Looseness on terminal board
1
8 y
Wring, connector
Disconnection, looseness, deterioration, rubbing
1
8 y
Dielectric capacitor
No liquid leak, deformation allowed
1
8 y
Cooling fan
Insulation resistance, noise
1
8 y
Electromagnetic switch (52C)
Contact resistance, operation
1
8 y
Blower
Propeller fan
Balance, crack
1
8 y
Fan motor
Insulation resistance, noise, vibration
1
20,000 h
14.2. When a protective device has tripped
To personnel for daily operation and control
• When the condensing unit is stopped by a protective device, consult your dealer or contact desk of maker. Report 1 Product model, 2 Alarm code
content and 3 Condition of failure, referring to User guide, “
Operation data sheet
”
To service and maintenance personnel
• Upon receipt of a report on the trip of protective device and resulting stop of condensing unit, reconfirm whether it was operated within a proper
operating range and did match the load capacity that of the condensing unit. For major items, refer to the following table.
• If the condensing unit or parts of refrigerant circuit have failed, take care of following points in order to prevent recurrence of the failure.
• Diagnose the cause in detail to identify the location and cause of failure.
• When repairing a leak from welding on pipe, make sure to recollect the refrigerant, and weld by passing nitrogen gas.
• When replacing the compressor, restore original formation on the suction, discharge pipes of compressor and the liquid injection pipe. If the formation is
changed, it could cause cracks on pipes owing to vibration. Take care not to mistake on the wire connection of compressor (L1, L2, L3) to prevent reverse
phase.
• When a part failed (including compressor), do not replace the while condensing unit, but replace defective part only.
• When disposing the condensing unit, make sure to collect the refrigerant beforehand.
• When the cause of failure is unknown, check the model of condensing unit, production No. and condition of failure, and report them to specified service
company.