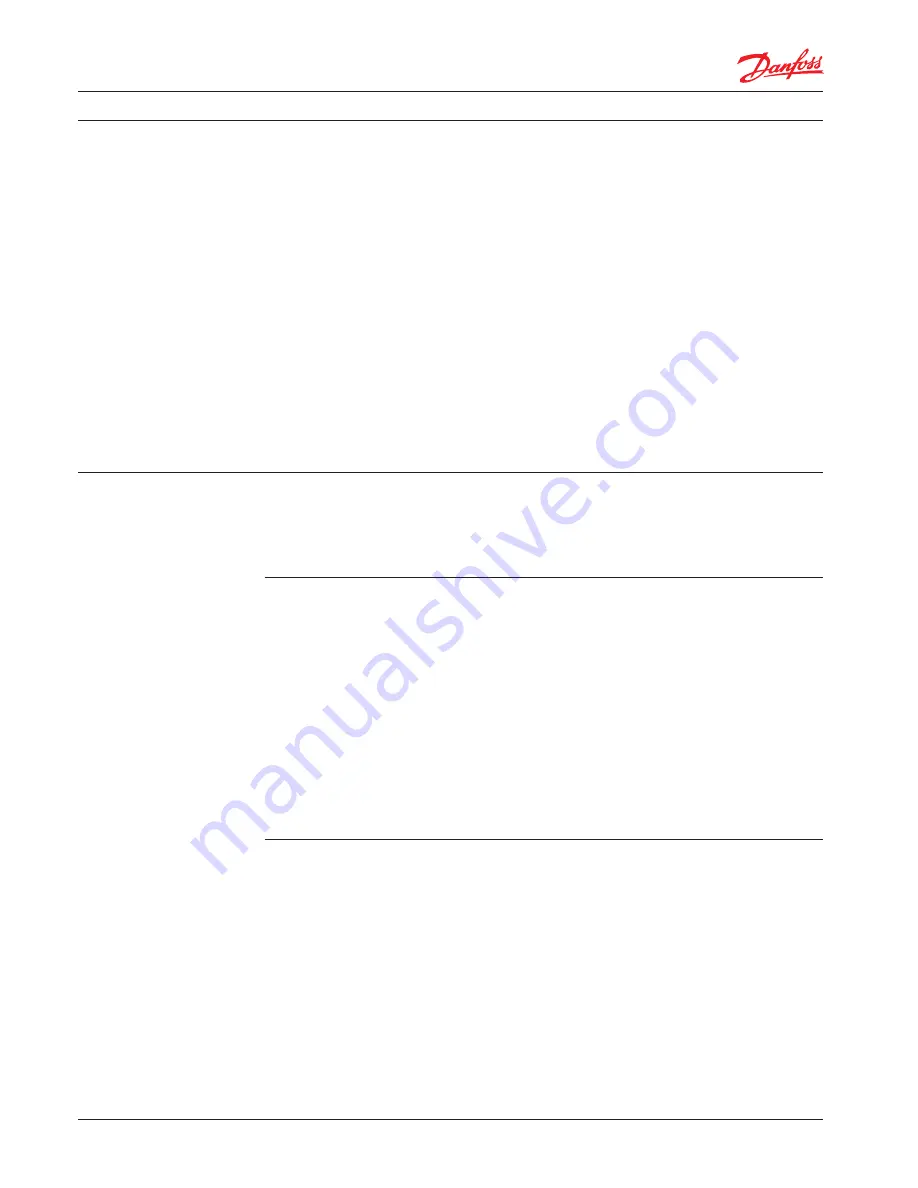
A
PPLICATION
GUIDELINES
Tests for pump down cycle approval:
As the pump-down switch setting is inside the
•
application envelope, tests should be carried out
to check unexpected cut-out during transient
conditions (ie. defrost – cold starting). When un-
wanted cut-outs occur, the low pressure pump-
down switch can be delayed. In this case a low
pressure safety switch without any delay timer
is mandatory.
While the thermostat is off, the number of pres-
•
sure switch resets should be limited to avoid
short cycling of the compressor. Use dedicated
wiring and an additional relay which allows for
one shot pump-down.
The pump-down allows to store all the refriger-
ant in the high pressure side circuit. On unitary or
close-coupled systems, where the system refrig-
erant charge is expected to be both correct and
definable the entire system charge may be stored
in the condenser during pump-down if all compo-
nents have been properly sized.
Other application needs a liquid receiver to store
the refrigerant.
Receiver dimensioning requires special attention.
The receiver shall be large enough to contain part
of the system refrigerant charge but it shall not
be dimensioned too large. A large receiver easily
leads to refrigerant overcharging during mainte-
nance operation.
Suction accumulator:
a suction accumulator of-
fers protection against refrigerant flood back at
start-up, during operations or defrosting by trap-
ping the liquid refrigerant upstream from the
compressor. The suction accumulator also pro-
tects against off-cycle migration by providing ad-
ditional internal free volume to the low side of the
system.
A suction accumulator must be carefully dimen-
sioned, taking into account the refrigerant charge
as well as the gas velocity in the suction line. De-
pending on the operating conditions it may hap-
pen that the recommended connections of the
accumulator are one size smaller than the suction
line.
Liquid fl ood back
During normal operation, refrigerant enters the
compressor as a superheated vapour. Liquid flood
back occurs when a part of the refrigerant enter-
ing the compressor is still in liquid state.
A continuous liquid flood back will cause oil di-
lution and, in extreme situations lead to lack of
lubrication and high rate of oil leaving the com-
pressor.
Liquid flood back test
- Repetitive liquid flood
back testing must be carried out under TXV
threshold operating conditions: a high pressure
ratio and minimum evaporator load, along with
the measurement of suction superheat, oil sump
temperature and discharge gas temperature.
During operations, liquid flood back may be de-
tected by measuring either the oil sump tempera-
ture or the discharge gas temperature. If at any
time during operations, the oil sump temperature
drops to within 20°F or less above the saturated
suction temperature, or should the discharge gas
temperature be less than 65°F above the satu-
rated discharge temperature, this indicates liquid
flood back.
Continuous liquid flood back can occur with a
wrong dimensioning, a wrong setting or malfunc-
tion of the expansion device or in case of evapora-
tor fan failure or blocked air filters.
A suction accumulator providing additional pro-
tection as explained hereunder can be used to
solve light continuous liquid flood back.
28
FRCC.PC.016.A1.22