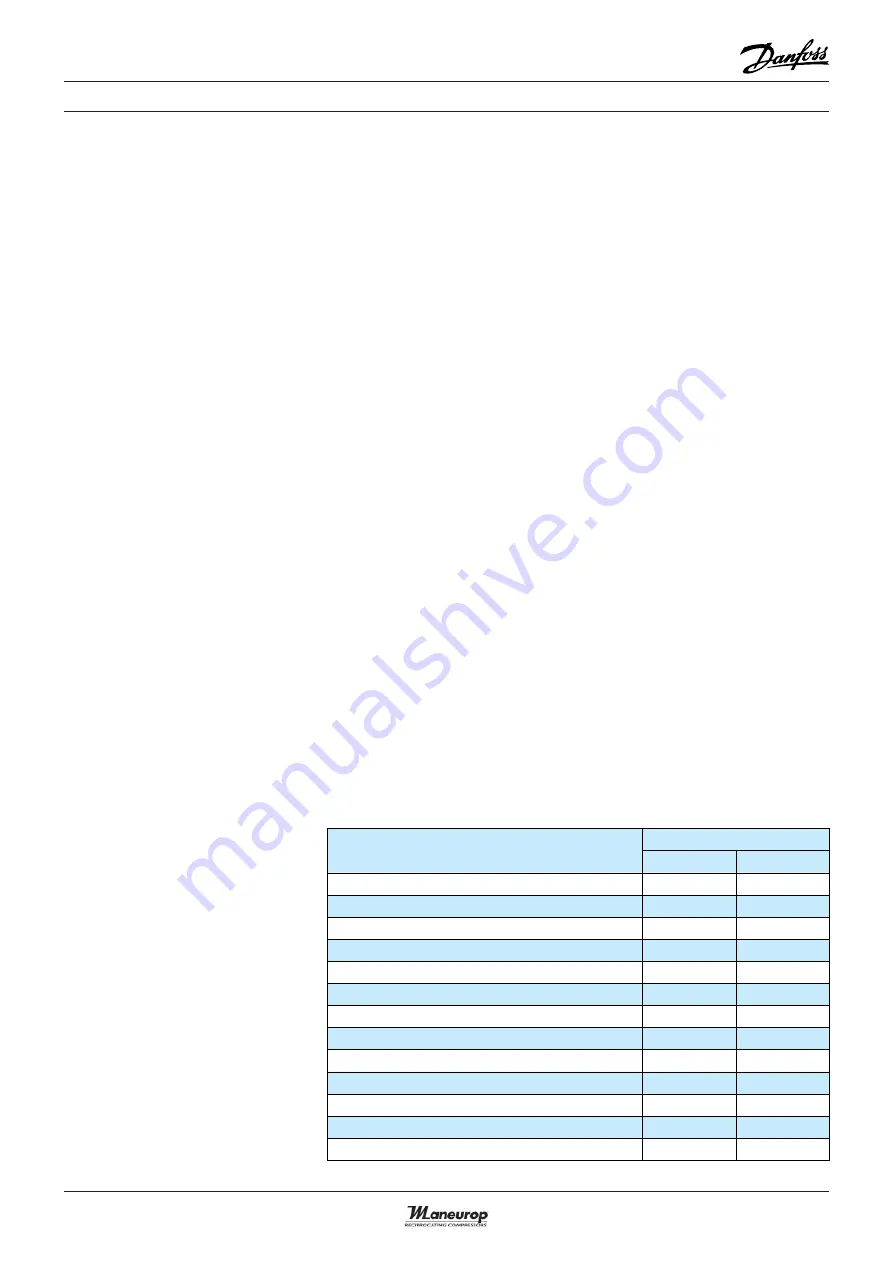
23
INSTALLATION AND SERVICE
System cleanliness
System contamination is one of the
main factors that aff ects equipment
reliability and compressor service life.
Therefore it is important to take care
of the system cleanliness when as-
sembling a refrigeration system. Dur-
ing the manufacturing process, circuit
contamination can be caused by:
z
Brazing and welding oxides,
z
Filings and particles from removing
burrs from pipe-work,
z
Brazing fl ux,
z
Moisture and air.
Only use clean and dehydrated,
refrigeration-grade copper tubes and
silver alloy brazing material. Clean all
parts before brazing and always purge
nitrogen or CO
2
through the pipes
during brazing to prevent oxidation.
If fl ux is used, take every precaution
to prevent the leakage of fl ux into
the piping. The use of fl ux core or
fl ux coated braze wire or rod instead
of brush applied paste fl ux is strongly
recommended. Do not drill holes
(e.g. for schrader valves) in parts
of the installation that are already
completed, when fi lings and burrs
cannot be removed. Carefully follow
the instructions below regarding
brazing, mounting, leak detection,
pressure test and moisture removal.
All installation and service work shall
only be done by qualifi ed personnel
respecting all procedures and using
tools (charging systems, tubes, vacuum
pumps, etc.) dedicated for R404A and
R507A.
Compressor handling,
mounting and connection
Component
Torque (Nm)
Min.
Max.
Rotolock suction valve, NTZ048 - NTZ068
80
100
Rotolock suction valve, NTZ096 - NTZ271
100
120
Rotolock discharge valve, NTZ048 – NTZ068
70
90
Rotolock discharge valve, NTZ096 - NTZ271
80
100
Electrical T-block screws HN°10-32 UNF x 9.5
-
3
Earth screw
-
3
Oil sight glass (with black chloroprene gasket)
40
45
3/8” fl are oil equalisation nut
45
50
Schrader nut
11.3
17
Schrader valve (internal)
0.4
0.8
Mounting grommet bolt, NTZ048 – NTZ136
12
18
Mounting grommet bolt, NTZ215 - NTZ271
40
60
Belt crankcase heater
-
4
Compressor handling
Maneurop® NTZ compressors must be
handled with care and all handling pro-
cedures must be performed smoothly
and gently. Each NTZ has been fi tted
with one lift ring which shall always be
used to lift the compressor. Once the
compressor is installed, the lift ring
shall never be used to lift the complete
installation.
Always use the proper tools for trans-
porting the compressor. Keep the
compressor in an upright position dur-
ing all handling tasks (manipulating,
transport, storage). The angle off the
vertical must not exceed 15 degrees.
Compressor mounting
The compressor must be mounted
onto a horizontal surface with a maxi-
mum slope of 3 degrees. Always use
the rubber mounting grommets that
are shipped with the compressor.
Mounting torques are listed in the be-
low table.