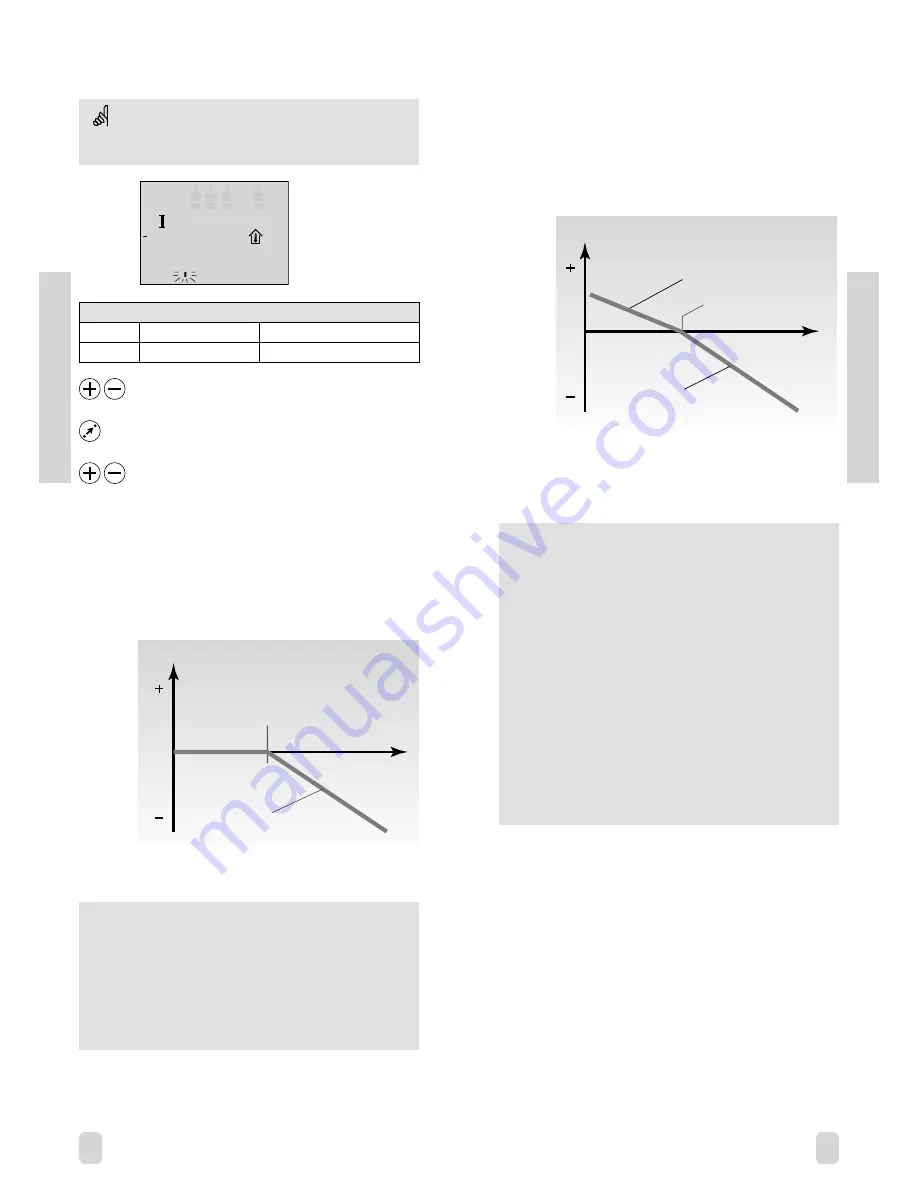
The grey
side of the
ECL Card
Basic set-up
The grey
side of the
ECL Card
Basic set-up
23a
Room temperature influence -
line 3
23a
This section is only relevant if you have installed a room
temperature sensor or ECA 60 / ECA 61 / ECA 62 / ECA 63.
Min.
influence
1
2
ON
0
-4
0
3
1
ON
3
ON
Max.
influence
3 Room temperature influence
Circuit
Setting range
Factory setting
I
0 ... 99 / -99 ... 0
min. 0, max. -40
The bar below the min. value blinks. Adjust the
min. influence.
Select the max. influence.
The bar below the max. value blinks.
Adjust the max. influence.
There are two basic principles for control of the room
temperature influence:
A: Max. room temperature limitation
Use this limitation if your system is fully equipped with
thermostats and you also want to obtain a max. limitation of
the room temperature. The controller will allow for free heat
gains, i.e. solar radiation or heat from a fire place, etc.
Influence
Desired room
temperature
Room
temperature
Max.
limitation
The max. influence determines how much the room
temperature should influence the desired flow temperature.
Example
The actual room temperature is 2 degrees too high.
The influence at max. limitation (right corner of the display) is
set to -40.
The influence at min. limitation (left corner of the display) is set
to 0.
Heat curve H is 1.8.
Result:
The desired flow temperature is changed by
2 x -40 x 1.8 x 0.1 = -14.4 degrees.
23b
B: Reference room temperature control
Used if your system is not equipped with thermostats and
you select the room with room temperature sensor as a
temperature reference for the rest of the rooms.
Set a positive value for the min. influence and a negative
value for the max. influence.
The room temperature sensor in the reference room registers
the difference between the desired and the actual room
temperature. The desired flow temperature will be corrected
to eliminate this difference.
Example 1
The actual room temperature is 2 degrees too low.
The influence at max. limitation (right corner of the display) is
set to -35.
The influence at min. limitation (left corner of the display) is set
to 20.
Heat curve H is 1.8.
Result:
The desired flow temperature is changed by
2 x 20 x 1.8 x 0.1 = 7.2 degrees.
Example 2
The actual room temperature is 2 degrees too high.
The influence at max. limitation (right corner of the display) is
set to -35.
The influence at min. limitation (left corner of the display) is set
to 20.
Heat curve H is 1.8.
Result:
The desired flow temperature is changed by
2 x (-35) x 1.8 x 0.1 = -12.6 degrees.
Influence
Min. limitation
Desired room
temperature
Room
temperature
Max. limitation