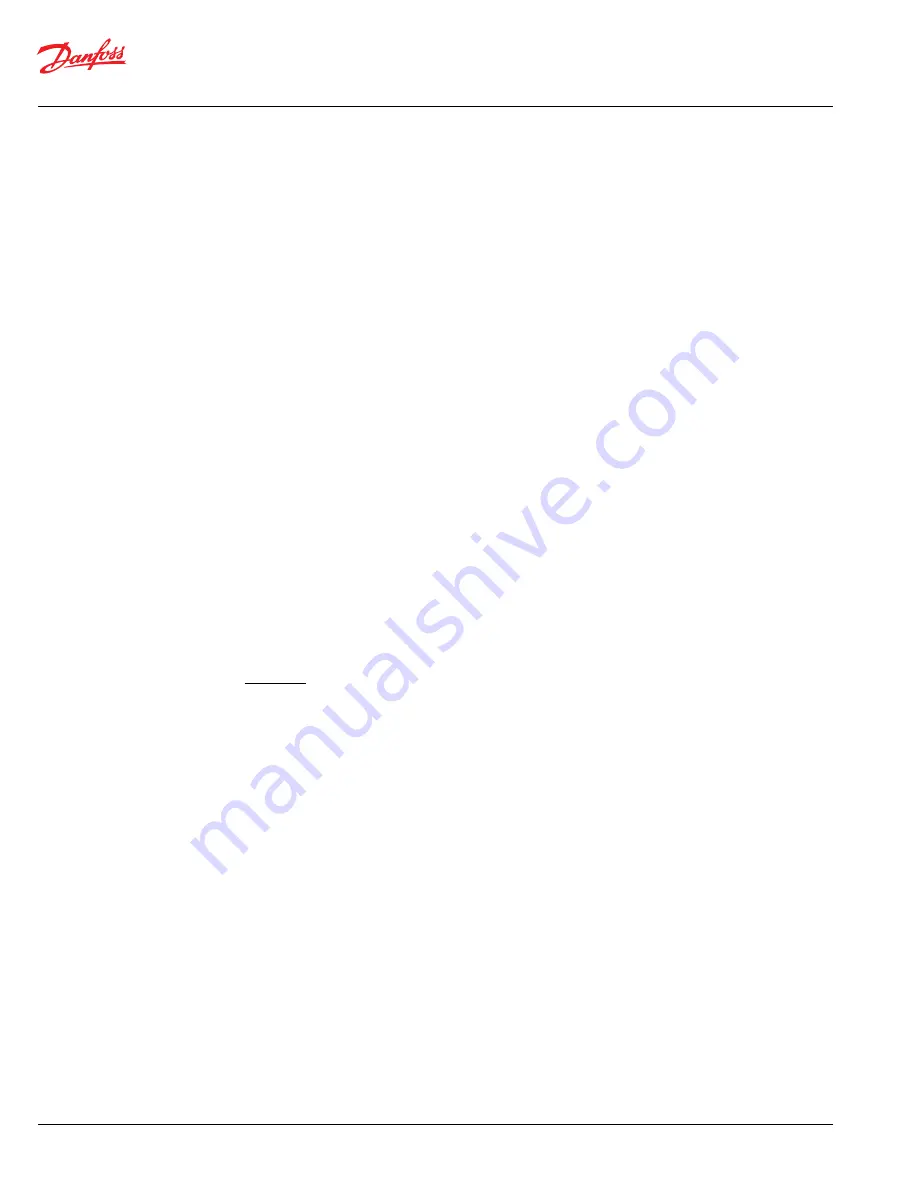
Danfoss
FT1330 Crimp Machine Operator’s Manual
8 | © Danfoss FT1330 Crimp Machine Operator’s Manual | 2023.02.
AQ439269212774en-000101
Basic Machine Operation & Operating Instructions
With the machine installed as outlined in this manual and with the power cord plugged into a suitable receptacle, switch the toggle switch
on the front of the cabinet to the “ON” position. The pump will start running.
The crimp die cage is pushed into the crimp ring by a hydraulic cylinder. Depressing the footswitch will extend the cylinder moving the
crimp die cage forward. Pressing the jog reverse button (next to the on/off switch) will move the crimp die cage back to its retracted
position.
The forward crimp limit is preset and requires no adjustment. If the footswitch is depressed and held until the forward crimp limit is
reached, the crimp die cage will stop its forward movement and return automatically to the retracted position when the footswitch is
released. If the footswitch is released before the forward crimp limit is tripped, the crimp die cage will stop and remain in that position.
Depressing the footswitch again will move the crimp die cage further forward or pressing the jog reverse button will move the crimp die
cage back toward the retracted position.
You will find that being able to jog the crimp die cage in either direction will be very helpful when positioning the fitting within the crimp
dies during the crimping cycle or when setting up the fitting locator.
The Danfoss FT1330 crimp machine is especially designed to provide a low cost, quick, easy to use machine to hydraulically crimp
Aeroquip standard field crimp fittings in hose sizes -4 through -20 and most four spiral hose through -20. Check the PowerSource Crimp
Spec Tool at danfoss.com/crimp for exceptions. This machine features color coded quick change dies (field crimp fittings) for greater
operating simplicity.
It is designed to crimp straight and elbow assemblies with standard fittings.
1. Check oil level. Fill to within one inch of opening with the cylinder fully retracted. Replace reservoir plug with breather cap supplied.
2. Plug into electrical outlet (dedicated circuit).
3. Select proper hose and fitting and preassemble (See Hose Preparation).
4. Insert proper die cage in place.
CAUTION: MAKE SURE DIES ARE COMPLETELY IN PLACE, FLAT AGAINST PRESSURE PLATE OR
DAMAGE TO THE DIES OR MACHINE MAY RESULT.
5. Position assembly against locator and adjust locator.
6. Set digital diameter control selector to the proper setting. Reference crimp diameter chart for field crimp and pages 45 - 52 for skive
type fittings.
7. Turn switch to “ON” position.
8. Depress foot switch, cylinder will stop automatically when crimp diameter is reached.
9. Release foot switch, cylinder will automatically retract.
10. Remove crimped assembly.
11. Check the crimp diameter of first crimped assembly of each run (it is best to adjust machine for nominal diameters).
12. When machine is not in use turn switch to “OFF” position.
Note:
The crimp diameter can be changed by adding or subtracting numbers on the digital indicator. The ratio is 2 to 1.
If the setting is .500 and it is changed to .502 the crimp diameter will be reduced by .001.
If the setting is changed to .498 the crimp diameter will be increased by .001.