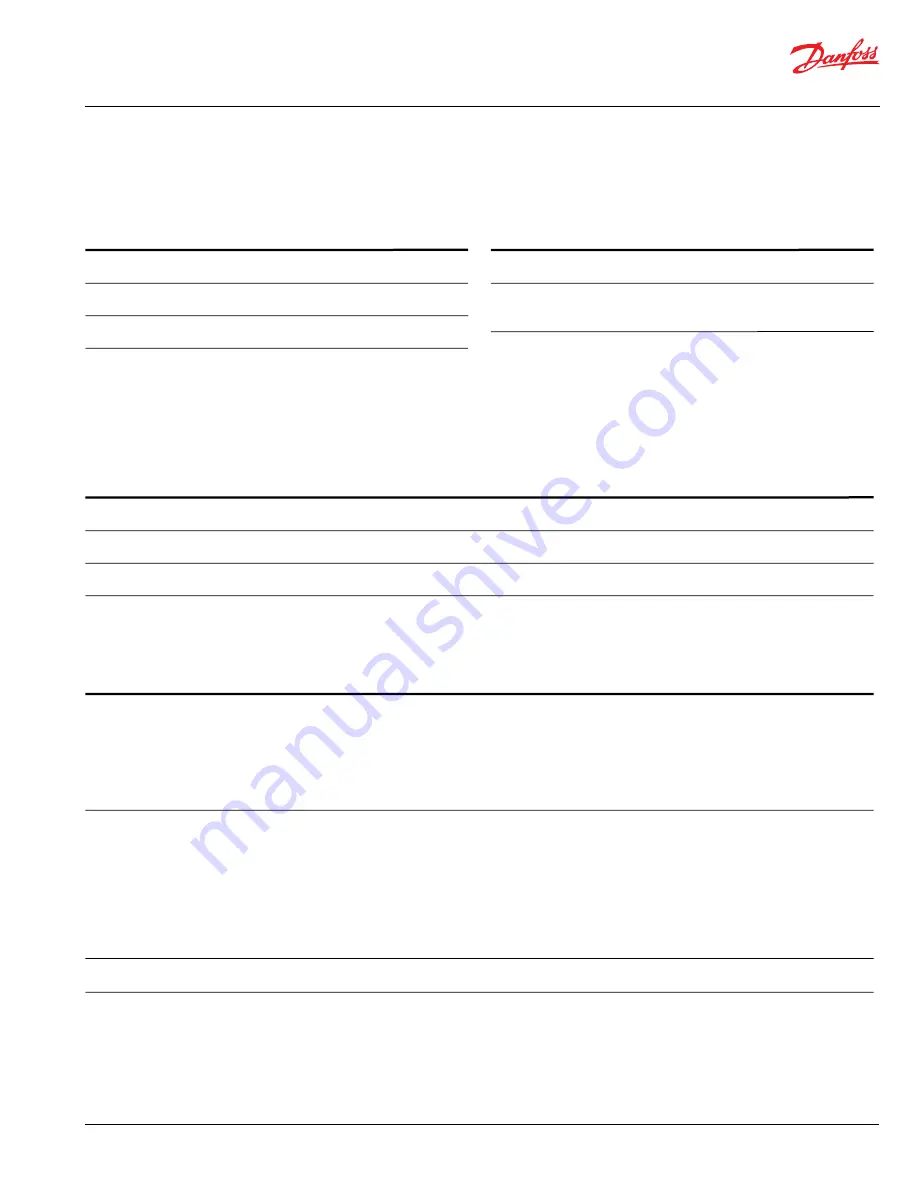
Danfoss ET1280 Crimp Machine Operator’s Manual
AQ439269292775en-000101
© Danfoss ET1280 Crimp Machine Operator’s Manual | 2023.01. | 9
Maintenence
Intervals
DIE CAGE LUBRICATION
Every 50 crimps
Relube sliding surfaces of dies
Every 500 crimps
Remove old grease and relube
Every 1000 crimps
Die cage maintenance
CRIMP RING MAINTENANCE
Every 500 crimps
Remove old grease and relube
Every 2000 crimps
Remove old grease;. Inspect for wear
or damage and relube if okay.
NOTE:
Use high efficiency PTFE grease (Danfoss part number T-400-G).
Procedures
MACHINE MAINTENANCE PROCURES
1.
Sliding surfaces must be kept free of dirt and other abrasive materials.
2.
All exposed black metal surfaces should be coated occasionally with a light film of oil to prevent corrosion.
3.
Periodically check the oil level in the fluid reservoir of the hydraulic power unit. Maintain the oil level of pump manufacturer’s hydraulic oil as needed.
NOTE:
Completely retract the crimp ring when checking the oil level.
DIE CAGE MAINTENANCE PROCEDURES
1.
Lubricate the die cage.
For maximum service. FT1380 die cages require lubrication at 50-crimp intervals with high efficiency PTFE grease (Danfoss part number T-400-G).
Periodically remove grease residue that has built-up on the sides of the dies and the crimp ring during the crimping process. Grease residue becomes
contaminated with metal and plating chips and airborne contaminants, which can cause premature wear of the dies and crimp ring.
It should carefully be removed without mixing it with newly applied grease.
2.
Die cage maintenance should be performed at 1000-crimp intervals or every six months, which ever occurs first.
Die cages should be clean of grease and debris and inspected for worn or damaged components.
a.
The sliding surface of the dies should appear smooth with no apparent galling.
Galled dies must be replaced. Individual dies in a cage can be replaced without replacing all eight dies.
b.
Replace springs that show any sign of damage or collapse (are shorter than other springs).
c.
The spring plate should appear smooth with no apparent galling.
Galled spring plates must be replaced.
d.
Inspect remaining components and replace those that are badly worn.
3.
Reassemble components and liberally apply grease to the die surface which slides along the spring plate. Torque the die cage bolts to 50in.-lbs.
4.
Ensure that all dies slide in and out freely.