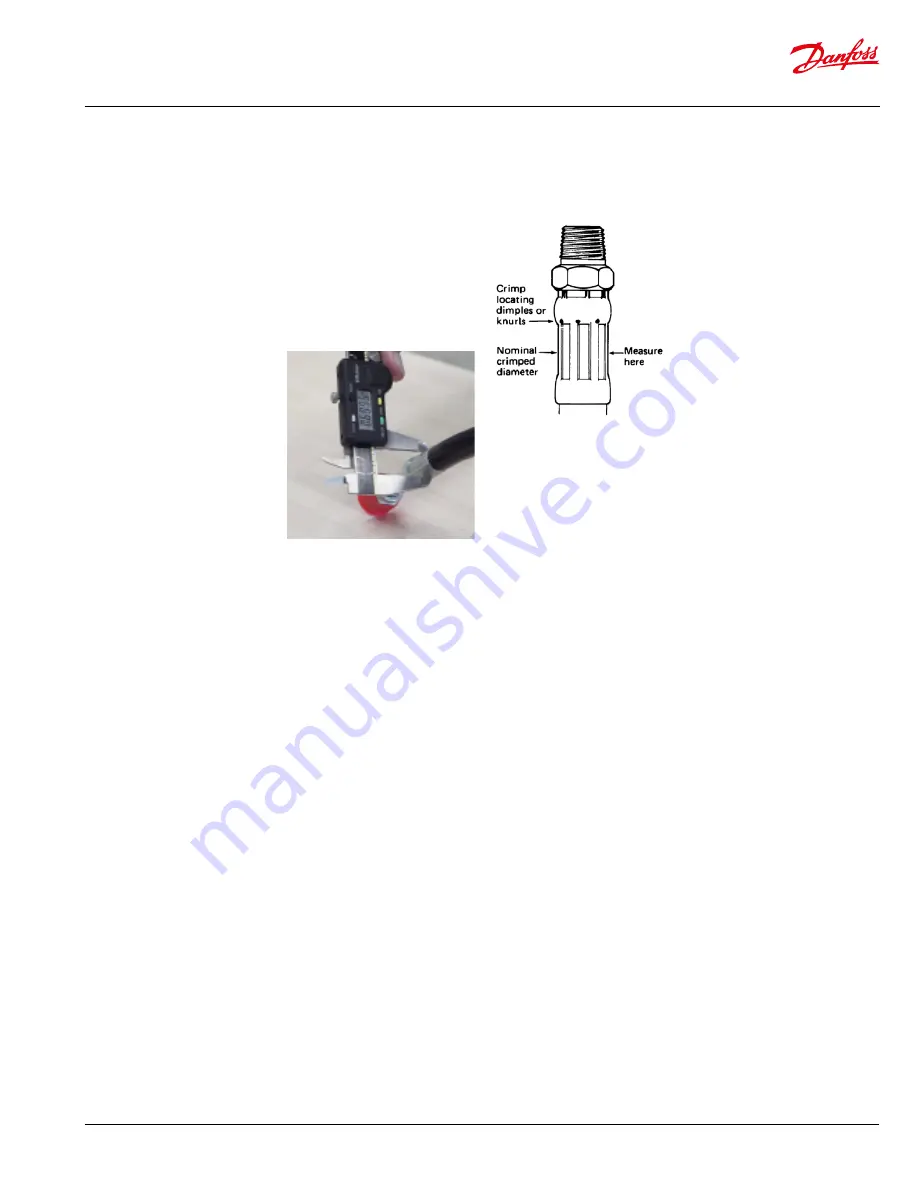
Danfoss ET1000 Crimp machine operator’s manual
AQ418954799548en-000101
© Danfoss ET1000 Crimp machine operator’s manual | 2022.06. | 5
Maintenance
Maintenance
Intervals
Machine
maintenance
procedures
Collet Assembly & Die
Ring Adapter Plate
Lubrication:
Every 30 crimps =
Re-lubricate sliding
surfaces of dies
Every 250 crimps =
Remove old grease
and re-lubricate
Base Die Ring & Die Ring
Adapter Plate
Maintenance:
Every 250 crimps = Remove old
grease and re-lubricate
Every 1,000 crimps =
Remove old grease,
inspect for wear or damage and
relubricate if okay.
1.
Sliding surfaces must be kept
free of dirt and other abrasive
materials.
2.
All exposed black metal surfac-
es should be coated occasion-
ally with a light film of oil to
prevent corrosion.
3.
Some fitting/hose combina-
tions require full pump reser-
voir capacity to complete the
crimp cycle. The oil level in the
fluid reservoir of the hydraulic
pump should be checked peri-
odically and refilled as required
with the pump manufacturer’s
hydraulic oil as needed.
NOTE:
Completely retract
the cylinder when checking the
oil level.
Nominal crimp diameter
Crimping procedures (cont.)
Measuring crimp diameters
should be a part of the
normal hose assembly
procedure. To ensure a
proper crimp diameter,
follow these steps:
1.
Measure the diameter in
the middle of the crimped
portion of the hose end. Place
the caliper in a position to al-
low for a measurement across
the pressed (flat) portion of
the crimp.
2.
Repeat step 1 for each of the
remaining sides for a total of
four measurements.
3.
Average the four measure-
ments and compare this
average to the target crimp
diameter shown in the Power
Source crimp spec tool and
ensure it falls within tolerance.