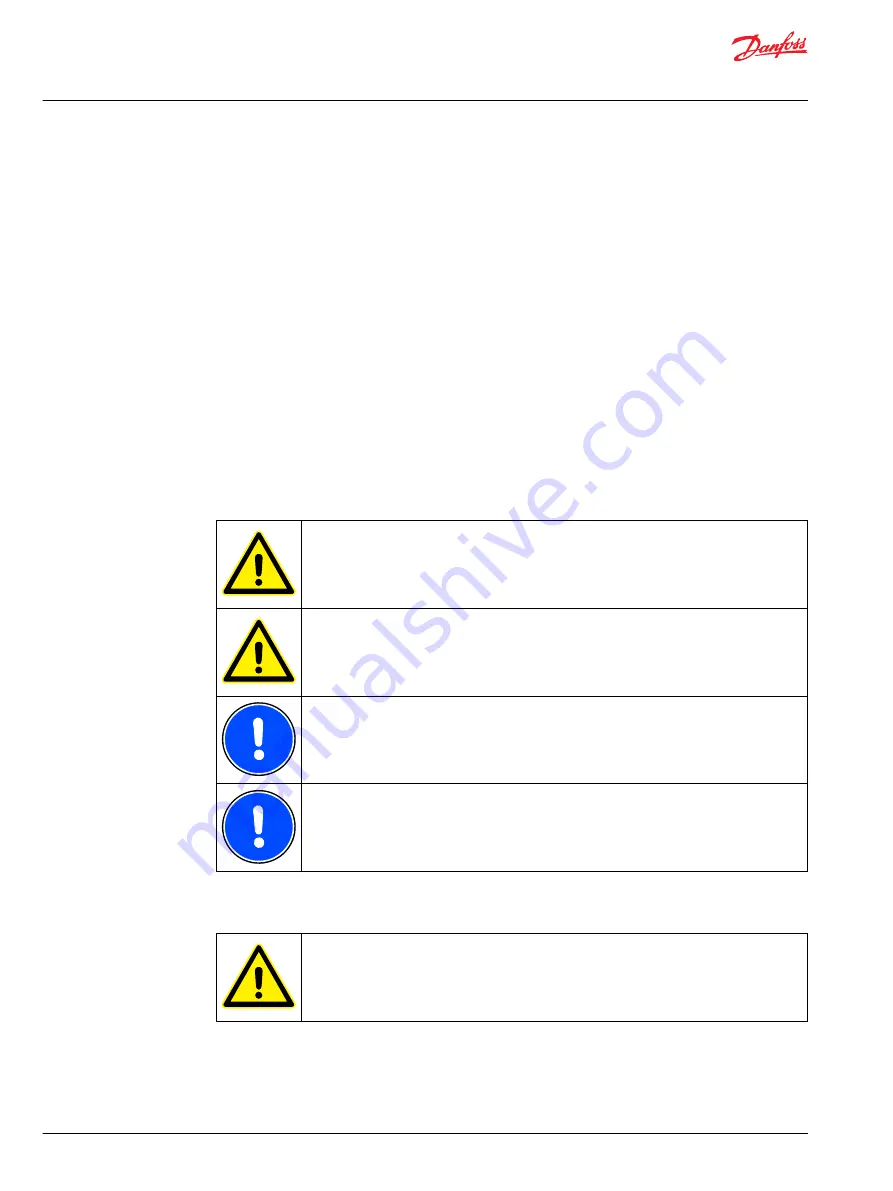
Operation conditions
The electric machine should be used for its intended purpose only and within limits specified by the
manufacturer, concerning:
•
Loading.
•
Cooling.
•
Speed range.
•
Service interval.
•
Ambient condition such as temperature and moisture.
The electric machine is designed for the following conditions:
•
Ambient temperature limits: -40°C ...+65 °C.
•
Maximum altitude 1000 m above sea level.
•
Maximum coolant liquid temperature at the inlet of the coolant circuit, see product data sheet.
•
Coolant liquid must be water- glycol mixture with maximum of 50 % glycol content. See
Chapter
.
If electric machine operation limits are exceeded, please contact Danfoss representative.
Condition monitoring during operation
Supervise the electric machine during operation to make sure that the electric machine
operates correctly and has a designed lifetime.
If you notice any deviations from the normal operation, for example elevated temperatures,
noise or vibration, stop the electric machine. Find the reason for the deviation and repair the
electric machine. Refer to Chapter
on page 63.
Maximum temperature of the bearings of the electric machine is:
120°C.
The maximum allowed winding temperature of the electric machine is shown on the rating
plate and in the data sheet.
Recommended lubricants
Do not mix different types of greases!
Greased for life bearings do not need relubrication during their lifetime. Grease relubricable bearings
(BHS option) need regular greasing. For further information, see Chapter
59.
The recommended grease type for the machine bearings is SKF LGHP-2 or equivalent. LGHP-2 is high
performance, high temperature bearing grease. For further information, see
User Guide
EM-PMI540-T2000
Operation
54 |
©
Danfoss | July 2021
BC265857530809en-000202