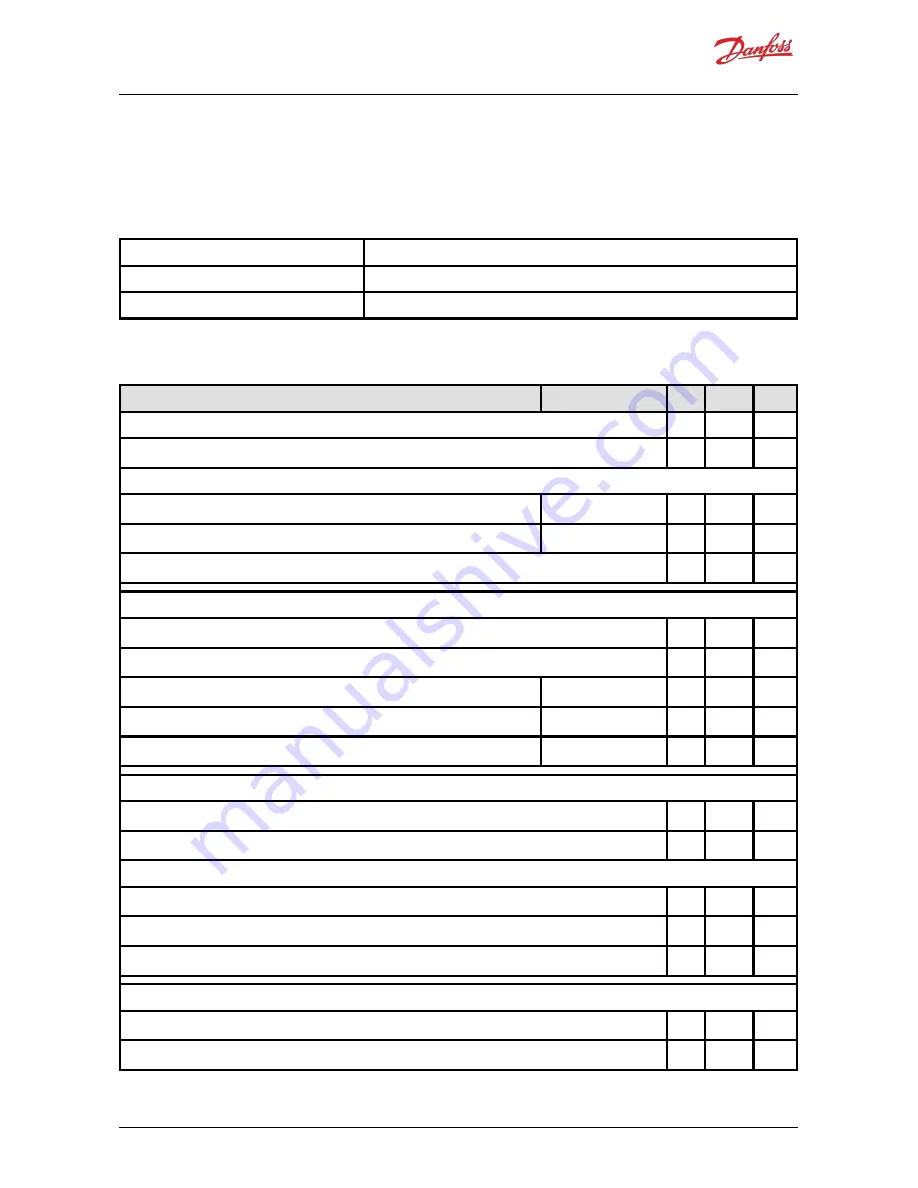
Electric Machine Yearly Maintenance Checklist
Date:
Table 20. Machine and customer information
Customer:
Machine type (from the rating plate):
Customer reference:
Machine serial number:
Service reference:
Date installed:
N.A = Procedure not applicable PASS = Procedure passed FAIL = Procedure failed
Table 21. Yearly maintenance checklist
Acceptance
N.A
PASS
FAIL
General construction
Noise or vibration during operation in general
☐
☐
☐
Mounting bolt tightness
D-end attachment bolt tightening torque
40 Nm
☐
☐
☐
N-end attachment bolt tightening torque
30 Nm
☐
☐
☐
Cleanliness of the enclosure and connected parts
☐
☐
☐
Electrical system
Weariness of the cables
☐
☐
☐
Electrical connections in general
☐
☐
☐
Cable gland tightening torque (to the box)
15 Nm
☐
☐
☐
Cable lug tightening torque (to the busbar)
13 Nm
☐
☐
☐
Connection box cover bolts tightening torque
4 Nm
☐
☐
☐
Cooling system
Coolant ow direction changed and connection checked
☐
☐
☐
Coolant quality as speci ed
☐
☐
☐
Used coolant:
Functioning of the cooling system in general
☐
☐
☐
Tightness of the tubing and connections (no leakages)
☐
☐
☐
Cleanliness of the ventilation plug
☐
☐
☐
Grounding
Power cable shield connection resistances to ground (machine enclosure) checked
☐
☐
☐
Low voltage cable shield grounding resistances checked
☐
☐
☐
Do not try to tighten bolts or screws that are not discussed in the product manual and that are not
needed for the normal installation procedures. Sealing of the screws may break.
EM-PMI375
13. Storage, installation and maintenance checklists
72 |
©
Danfoss | Produced By: Danfoss Power Solutions | January 2019
| BC265856307805en-000105
Summary of Contents for EM-PMI375-T200
Page 1: ...User Guide Motor Generator EM PMI375 danfoss com ...
Page 77: ......