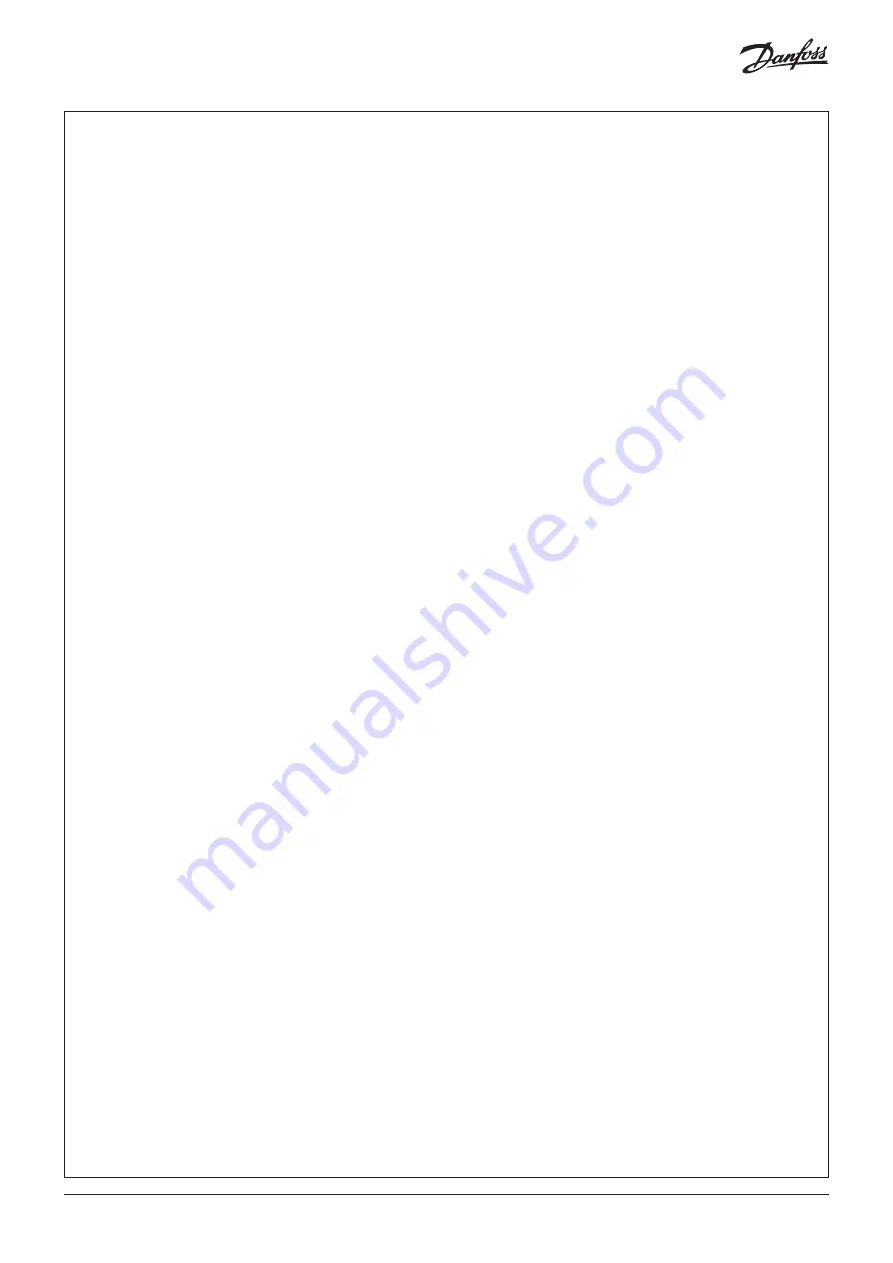
© Danfoss | Climate Solutions | 2021.07
7 | AN375548103097en-000202
General features and Warnings
Plastic housing:
• DIN rail mounting complying with EN 60715
• Self-extinguishing V0 according to IEC 60695-11-10 and glowing/hot wire test at 960 °C according to IEC 60695-2-12
CE COMPLIANCE
- Operating conditions CE: -20T60, 90% RH non-condensing
- Storage conditions: -30T80, 90% RH non-condensing
- Electromagnetic compatibility EMC: 2014/30/EU with the following norms,
- EN 61000-6-2:2005, Generic standards - Immunity for industrial environments (AC and DC voltage supply)
- EN 61000-6-3+A1:2011 and EN 61000-6-3:2007, Generic standards - Emission standard for residential, commercial and
light-industrial environments (DC voltage supply only)
- EN 61000-6-4:2019 and EN 61000-6-4:2007+A1, Generic standards – Emission standard for industrial environments
(AC and DC voltage supply)
GENERAL WARNINGS
- Every use that is not described in this manual is considered incorrect and is not authorized by the manufacturer
- Verify that the installation and operating conditions of the device respect those specified in the manual, especially concerning the
supply voltage and environmental conditions
- All service and maintenance operations must be performed by qualified personnel
- The device must not be used as a safety device
- Liability for injury or damage caused by the incorrect use of the device lies solely with the user
INSTALLATION WARNINGS
- Recommended mounting position: vertical
- Installation must comply with local standards and legislation
- Before working on the electrical connections, disconnect the device from the main power supply
- Before carrying out any maintenance operations on the device, disconnect all electrical connections
- For safety reasons the appliance must be fitted inside an electrical panel with no live parts accessible
- Do not expose the device to water sprays or to a relative humidity greater than 90%.
- Avoid exposure to corrosive or pollutant gases, natural elements, environments where explosives or mixes of
flammable gases are present, dust, strong vibrations or shock, large and rapid fluctuations in ambient temperature
that might cause condensation in combination with high humidity, strong magnetic and/or radio interference
(e.g. transmitting antennae)
- Use cable ends suitable for the corresponding connectors. After tightening connector screws, tug the cables gently to check their
tightness
- Minimize the length of probe and digital input cables as much as possible, and avoid spiral routes around power
devices. Separate from inductive loads and power cables to avoid possible electromagnetic noises
- Avoid touching or nearly touching the electronic components on the board to avoid electrostatic discharges
PRODUCT WARNINGS
• Use a class II power supply.
• Connecting any EKF ports to mains voltage will permanently damage the controller.
• Battery backup terminals do not generate power to recharge a device connected.
• Battery backup - the voltage will close the stepper motor valves if the controller loses its supply voltage.