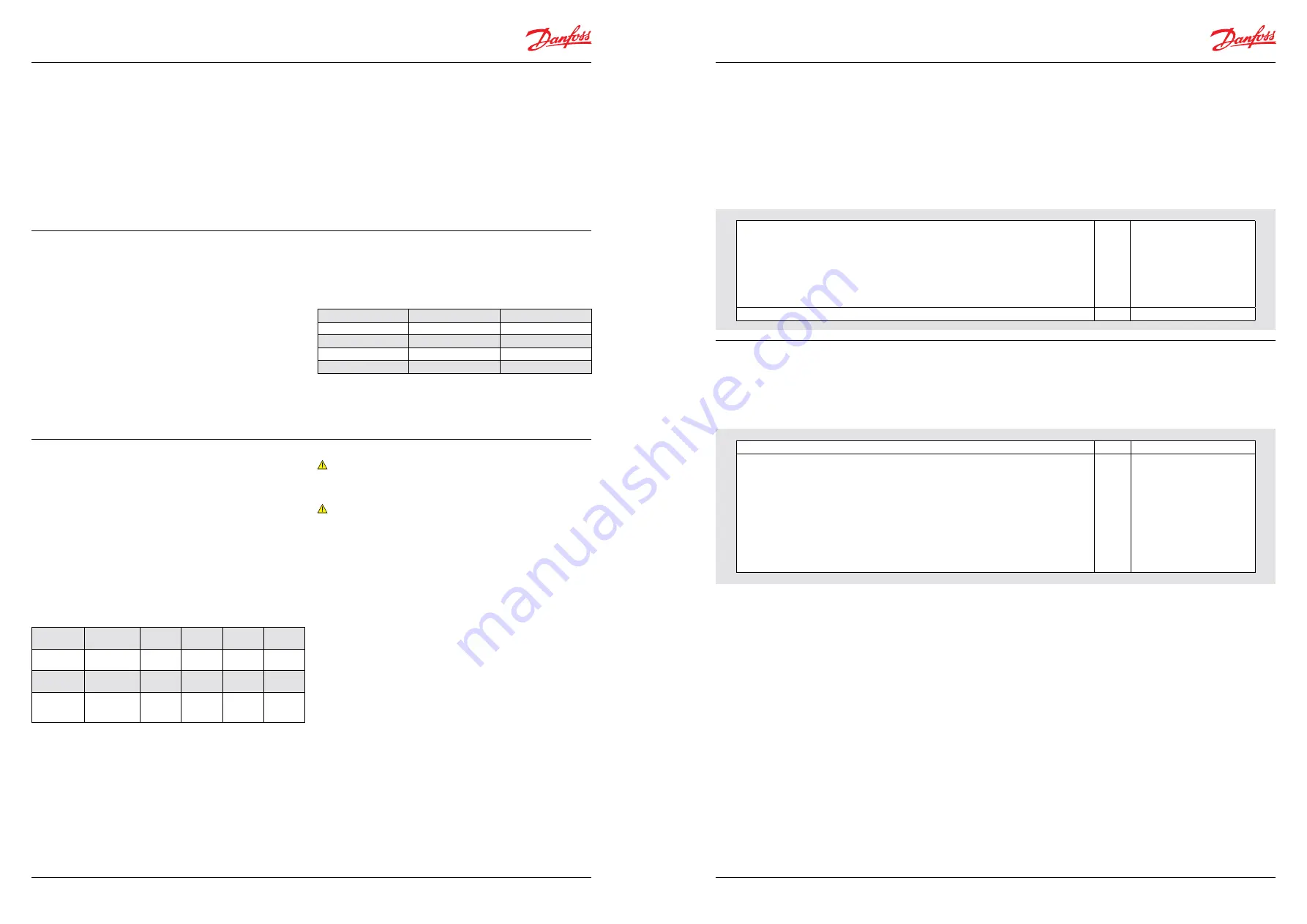
©Danfoss A/S (AC-MCI / sw), 2014-03
DKRCC.PS.RP0.A1.02/520H7142
13
12
DKRCC.PS.RP0.A1.02/520H7142
©Danfoss A/S (AC-MCI / sw), 2014-03
Manual Superheat controller type EKD 316
Manual Superheat controller type EKD 316
Types of regulation
As a general rule, do not use mode 2 (Load define application)
if the effect is not evaluated by e.g. an OEM chiller
manufacturer in a laboratory.
An incorrect setting will only make regulation poorer than the
factory setting of mode 1.
Single Loop (address o56 Reg.type = 1)
The EKD 316 has the traditional PI controlling function with the Kp
factor for Proportional Gain and Tn for Integration Time in seconds.
This is also known as the Single loop control with only one PI
block, as shown in the diagram below.
Instability caused by too much Proportional Gain can be corrected
by reducing to the value of the Kp factor.
This should be done by gradually reducing and observing the
results before making further reductions.
If the superheat response is slow to change, it can be increased by
reducing the value of the Integration Time Tn.
When tuning the superheat stability, it is good practice to have a
fixed superheat reference by making
SH max the same as SH min.
Double Loop (address o56 Reg.type = 2)
The controller can regulate the superheat using a double loop
system. The so-called outer loop is really the same as in the single
loop system except that the output of PI block is the reference for
the inner loop.
The inner loop also has a PI block where the Proportional Gain
factor is KpT0 and the Integration Time is TnT0.
The feedback of the inner loop is the temperature difference
between media temperature S4 and S1. This value represents the
load on the evaporator and large values will tend to increase the
opening degree OD% of the valve.
The tuning of the double loop is more complicated than the single
loop and it is advisable not to change too many parameters at
the same time. The starting point should be to use the following
settings.
Function
Parameter
Value
Kp factor
n04
0.7
Tn sec
n05
120
KpT0
n20
3
TnT0 sec
n44
30
If the superheat is unstable, the KpT0 parameter should be slightly
reduced. The value parameter Kp factor is not large so little is
gained by reducing this parameter.
For details refer to the "Finding the optimum setting” section.
When to use Single or Double Loop
In most applications and especially air coolers, the single loop is
the best option due to its simplicity and being easier to tune.
In water chillers where the S4 sensor is located at the leaving water
outlet, the double loop gives some advantage in terms of being
less susceptible to compressor or fan step changes. In addition, it
opens the valve quicker during startup. However, the double loop
is less advantageous on air coolers because of the slower response
to the media temperature changes.
Recommended control loop type and settings for some
applicatiions
From the experience of using single loop and double regulation,
the following recommendations are given. These are only
recommendations and the final choice is made by the end user.
Application
Reg. type
Kp
factor
Tn sec
KpT0
TnT0 sec
address
n56
address
n04
address
n05
address
n20
address
n44
Air cooler
1
(Single loop)
3.0
120
0.4
-
Water chiller
2
(Double
loop)
0.7
120
2.0
30
Note:
The S4 sensor has to be connected when Reg. type = 2, otherwise
an alarm sounds.
Note:
After o56 is changed, the controller must be switched off and
powered up again.
There are two modes for operating the valve manually, and these
are described in the following sections.
Operating the valve manually from the external display (or via
MODBUS)
The opening degree of the ETS can be operated manually by
setting parameter o18 to 1 and then setting parameter o45 to the
required opening degree between 0% and 100%. Relay outputs
can also be checked using parameter o18.
Operating the valve manually using an external analogue
signal
The opening degree of the ETS 6/ETS valve can be operated
manually with 0 to 20 mA or 4 to 20 mA or 0 to 10 V or 1 to 5 V
external analogue signal connected to terminals 21 (-) and 22 (+)
of the controller.
Manual control of outputs
For service purposes the ETS 6/ETS output and alarm relay outputs can be forced, but
only when regulation has been stopped.
OFF: No override
1: Manual control via o45 is enabled
2: The alarm relay releases so that there is a connection between 24 and 25 (= alarm)
3: The alarm relay picks up so that there is a connection between 25 and 26 (= no alarm)
018
Manual ctrl
Manual control of the valve’s opening degree
045
0-100% valve OD
Controlling a valve with an analogue signal
061
Application mode 061=1
Input signal for external control of the valve's opening degree
Only used if o61 is set to 1.
Definition of the signal's range:
0: No signal
1: 0-20 mA
2: 4-20 mA
3: 0-10 V
4: 1-5 V
(At the lower value the valve will be closed. At the upper value the value will be fully
open. There is a linear relationship between the signal and the opening degree. The
height of the valve is not taken into account.)
o10
AI type
Manually operating the valve