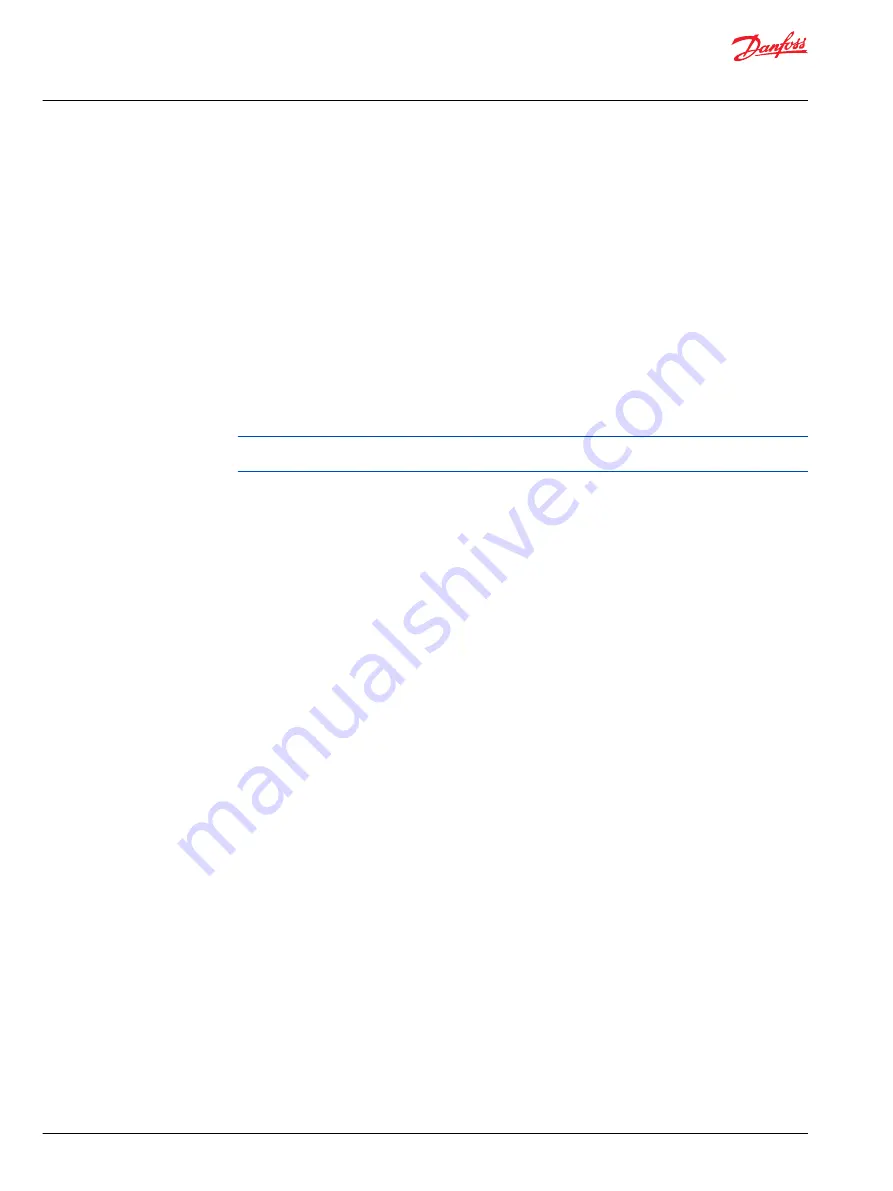
Pressure Compensated Control Adjustment
1. Install a pressure gauge in port MB to measure outlet pressure.
2. Ensure the pump is operating at maximum displacement. If the control has Electric Displacement
Control, input 700mA to obtain maximum displacement.
3. Load the pump outlet pressure to at least 30 bar higher than the expected pressure compensated
control setting. This may be achieved by operating a hydraulic function to its full extension, putting
the pump in a dead-head condition.
4. Loosen the Pressure compensated control lock nut and turn the Pressure compensated control
adjusting screw until the desired setting is indicated on the pressure gauge at port MB. Clockwise
rotation increases pressure, counterclockwise rotation decreases; approximate gain per turn (see
table). Once the PC adjustment is complete, hold the position of the adjustment screw
and torque the PC control lock nut to 21.6-24.6 N·m [lbf·in].
5. Stop the prime mover, remove the pressure gauge, and return the system to its normal operating
configuration.
If the pressure does not increase, an external system relief valve may require adjustment. External
system relief valve must be set above the Pressure compensated control setting for proper operation.
Power Control Adjustment
1. Install a pressure gauge in port MB to measure outlet pressure. Install a flow meter in outlet line to
measure pump flow.
2. Start the prime mover and make sure the pump is operating at maximum displacement. If the control
has Electric Displacement Control, input 700mA to obtain maximum displacement. By doing this, the
functions will not interfere with each other, if maximum displacement is commanded by the EDC at
all times, the MTC function will take priority once the start point pressure is reached.
3. Load the pump outlet pressure to the reference pressure value previously obtained in the calculation,
loosen the power control lock nut and turn the power control adjusting screw and monitor the flow
meter, when the flow meter shows the flow corresponding to the previous calculation, stop turning,
while holding the position of power control adjusting screw, torque the power control lock nut to
21.6~24.6 N•m [191-218 lbf•in]. Clockwise rotation increases power, counterclockwise rotation
decreases, approximate gain per turn (See
table.)
4. Stop the prime mover, remove the pressure gauge and flow meter, and return the system to its
normal operating configuration.
Load Sensing Control Adjustment
1. Install a pressure gauge in port MB to measure outlet pressure, Tee-in a pressure gauge to the LS
signal line (port X) to measure LS signal pressure. Install a flow meter in outlet line to measure pump
flow.
2. Start Prime mover and allow fluid to reach normal operating temperature.
3. Totally lock the LS control; to do this first loosen the LS control lock nut and turn the LS control
adjusting screw clockwise all the way to the end, while holding the LS control adjusting screw, torque
the control lock nut to 21.6~24.6 N•m [191-218 lbf•in].
4. Adjust Power control and pressure compensated control (if used).
Service Manual
D1 High Power Open Circuit Pumps Size 65/130/145/193/260
Adjustments
38 |
©
Danfoss | July 2019
L1527453 | AX00000292en-CN0201