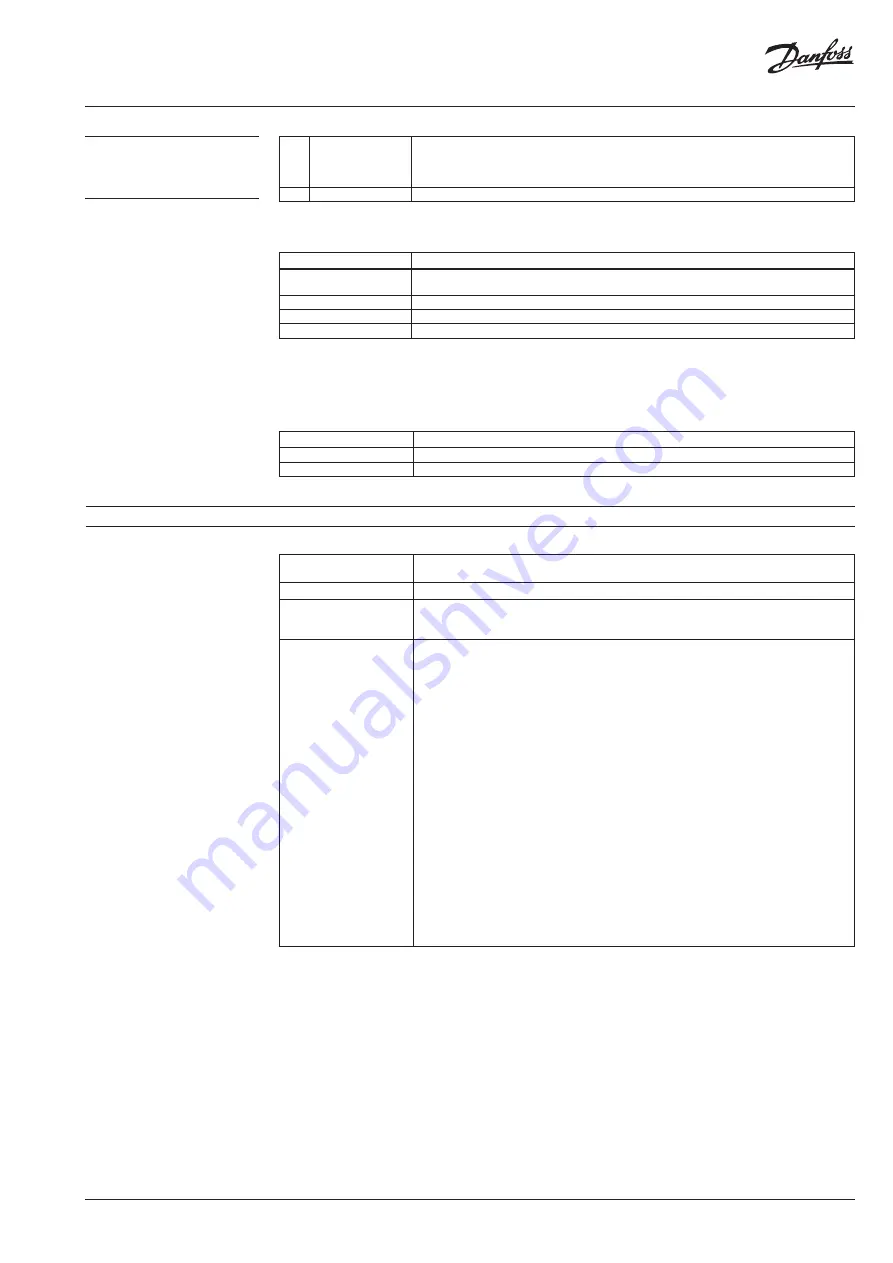
© Danfoss | 2019.02 | 15
VI.D3.C2.02
CCR2+ Controller
78
Slave Unit Comm.
Status
Shows Slave Unit communication status between CCR2+ Controller
0% –
no communication
100% –
communication OK
Possible (readable values): 0 – 100%
Save Settings
Click »Save Settings« to confirm changes
Note:
In case of changing IP address in CCR+ Controller, changes should also be applied in PC local network settings.
FIRMWARE MENU:
Name
Description
Upgrade of firmware
To update CCR2+ with new firmware first download firmware file from Danfoss website.
Then follow procedure: Browse file -> Start upgrade!
Reset settings to default
To return all setting to default (except Network settings) click on “Return Defaults”
Reset to defaults passwords To reset all passwords to defaults (admin1234) click on “Reset Passwords«.
Reset network settings
Reset all network settings to defaults
NOTE:
When uploading firmware, do not interrupt the web browser by closing the window, clicking a link, or loading a new page. No
not power-off CCR2+. It could corrupt the firmware.
When the upload is complete, CCR+ restarts. The upgrade process typically takes several minutes.
LOGIN MENU – push user to change password
Name
Description
Login
Access with login password enable changes in all setting
Skip login
Access without password allows only data readings. Changes of settings values can not be done.
11. Service/trouble shooting
Reset Wi-Fi password
Available via long press on reset button (located on LAN port) for at least 5 seconds.
Wi-Fi password is reset to “admin00x” where x is the number of BT (blue) LED blinks.
Reset the setting only
Go to firmware menu and click on “Return Defaults”
Reset password only
(but not change other
parameters)
Go to firmware menu and click on “Reset passwords”
Recovery (device can be
recover back to factory
firmware)
Via long press on reset button, power down and with access code “
369
” (code for recovery to
default firmware). To perform a recovery, you need to make these steps:
1. turn off power supply
2. press hardware button
3. turn on power supply, power led will be ON
4. hold button for more than 5 sec until ALL 3 leds turned ON
5. when all 3 leds is turned immediately release the button
From this moment you need to enter 3 digits code
In this mode there are two hardware button function:
- short press increase code number,
- long press switch to next code digit
Currently code number is signalled by lighting of led diode: blue led = 1 digit, white led = 2 digit,
orange led = 3 digit
Example to enter code 123:
- first led diode (blue) is turned ON, then make a short button press 1 time, blue led should
blink once
- make a long press until white led is turned on
- using short button press 2 times, white led should blinks 2 times
- make a long press until orange led is turned on
- using short button press 3 times, orange led should blinks 3 times
- if code is entered properly than recovery has started.
DO NOT TURN OFF POWER SUPPLY!
10. CCR2+ DASHBOARD
(Web App Screen)
(continuous)