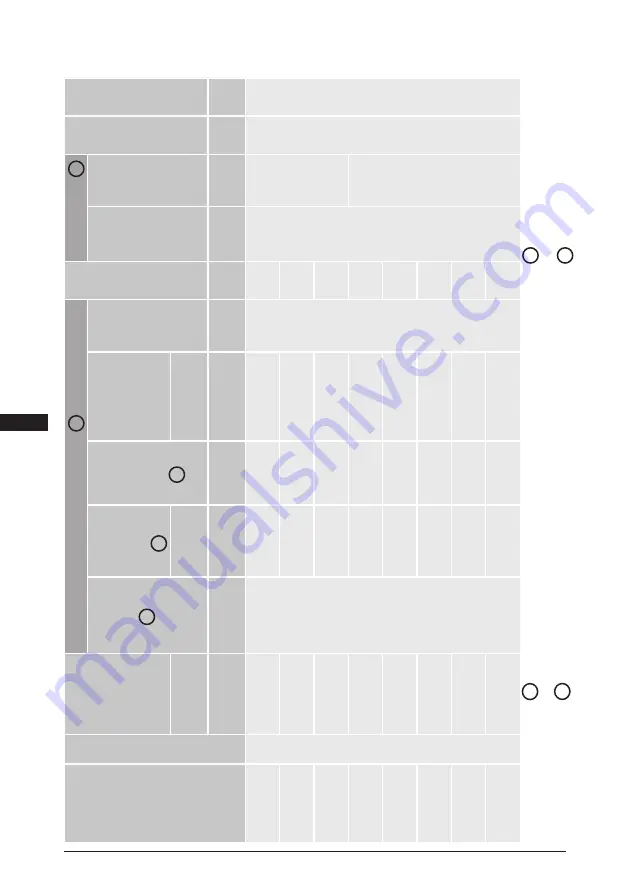
D
US
F
E
30 | AQ450440081306en-US0201
© Danfoss | Climate Solutions | 2023.07
Type UL-HGX44e/
No. of cylinders
Displacement
(1450 / 1740 rpm)
Electrical data
Weight
C
onn
e
c
tion
s
Oil charge
(ex works)
Oil charge
(sight glass center)
Voltage
Max.
operating
current
Max. power
consumption
Starting
current
(rotor locked)
permissible
frequency range
Discharge line
DV
Suction line
SV
50 Hz
60 Hz
P
W
1+
2
P
W 1 / P
W
1+
2
cfh
V
A
kW
(H
P)
A
Hz
kg
m
m
(in
ch)
m
m
(in
ch)
ltr
(fl
.oz
)
ltr
(fl
.oz
)
475 M
L 9
4
14
6
0
17
52
380-420 V Y/YY - 3 - 50 Hz PW
440-480 V Y/YY - 3 - 60 Hz PW
PW = Part Winding
Winding ratio
: 50 % / 50 %
19
11
,0
(15
,0
)
65 / 1
09
25 - 70
361
28 (
1
1
/
8
)
35 (
1
3 /
8
)
2.7
(9
5)
2.
3
(8
1)
475 S 1
2
14
6
0
17
52
23
13,1
(17,8)
87 / 1
49
372
56
5 M
L 1
2
17
37
20
85
22
13,2
(17,9)
65 / 1
09
359
56
5 S 1
5
17
37
20
85
26
15,6
(21,2)
10
1 / 1
74
388
42 (
1
5
/
8
)
66
5 M
L 1
4
20
39
24
47
26
15,4
(20,9)
87 / 1
49
380
66
5 S 2
0
20
39
24
47
30
18,3
(24,9)
10
1 / 1
74
387
77
0 M
L 1
5
2365
2838
30
17,8
(24,2)
10
1 / 1
74
385
77
0 S 2
2
2365
2838
35
21,4
(29,1)
10
1 / 1
74
385
9
|
Technical data
1
2
3
2
4
Tolerance (± 10%) rela
tive to the mean value of the volta
ge range.
Other volta
ges and types of current on request
.
-
Th
e s
pe
ci
fic
at
io
ns f
or ma
x. p
ow
er c
on
su
m
pt
io
n a
pp
ly f
or 6
0H
z o
pe
ra
tio
n.
-
Take account of the max.
opera
ting current / max.
po
wer consumption for
design of fuses,
supply lines and safety devices.
Fuse:
Consumption ca
tegor
y
AC3
1
2
All specifica
tions are based on
the a
vera
ge of the volta
ge range
For solder connections
3
4