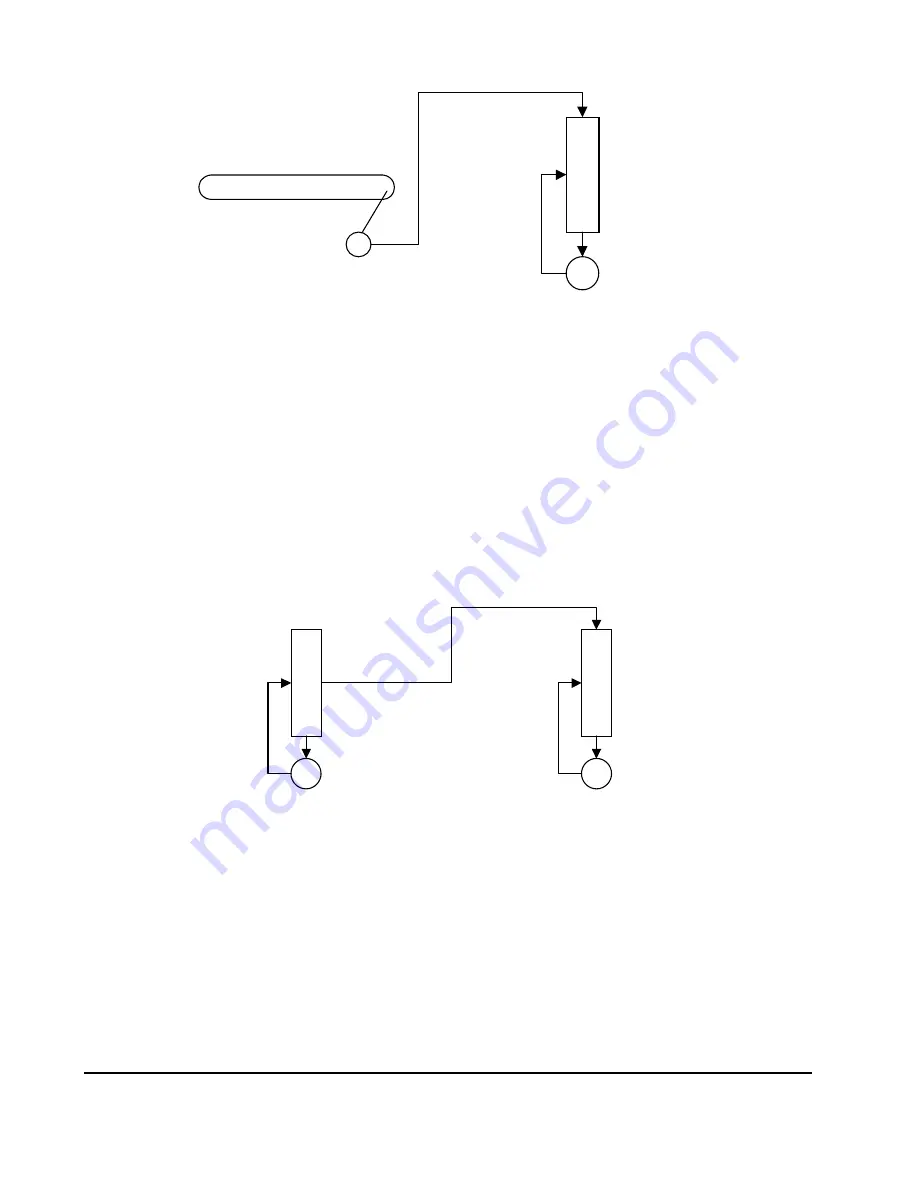
Document Number: P-SS-004-09 Rev 5
Old Numbers (AS6007H, A-SS-004-20208)
Revised 11/20/2003
www.DanaherMotion.com
Page
2
Conveyor
Encoder
SE
R
V
O
ST
A
R
S
60
0
Encoder input
Resolver/
sine encoder
feedback
Electronically-
geared
drive
Electronically-
geared
motor
Figure 1: Following a Non-driven Encoder
Following a Servomotor
Some gearing applications need one servomotor to follow another. Here, the encoder from the first
(master) motor becomes the gearing input to the second (slave) motor. In this case, the master
encoder must connect as both the feedback for the master drive and input for the slave drive.
For cases where the feedback device of the master servomotor is something other than a physical
encoder, the SERVO
STAR
S600 provides encoder emulation. For example, neither a sine encoder
nor a resolver directly produce signals compatible with encoders. The SERVO
STAR
S600 encoder
emulation circuit produces output signals equivalent to an encoder from any feedback device that is
used as the main feedback device. This allows any SERVO
STAR
S600 to serve as the master for
any other electronically-geared SERVO
STAR
S600.
SE
RV
O
ST
A
R
S6
00
Encoder input
Resolver/
sine encoder
feedback
Electronically-
geared
drive
Electronically-
geared
motor
SE
RV
O
ST
A
R
S6
00
Resolver/
sine encoder
feedback
Master
drive
Master
motor
Encoder
emulation
output
Figure 2: Following a Servo-driven Encoder
Following a Multi-Pulse Generator (MPG)
Some applications require a motor to follow the input from an operator via a multi-purpose
generator (MPG), such as an encoder handwheel. In many cases, a traditional contact-based
potentiometer is used to take input from the operator. However, such a device is not appropriate for
some environments because the contact surface wears over time and becomes unreliable. By using
electronic gearing, an optical encoder is used to replace a contact potentiometer. The
SERVO
STAR
S600 accepts the input from an encoder as either a velocity or position command.