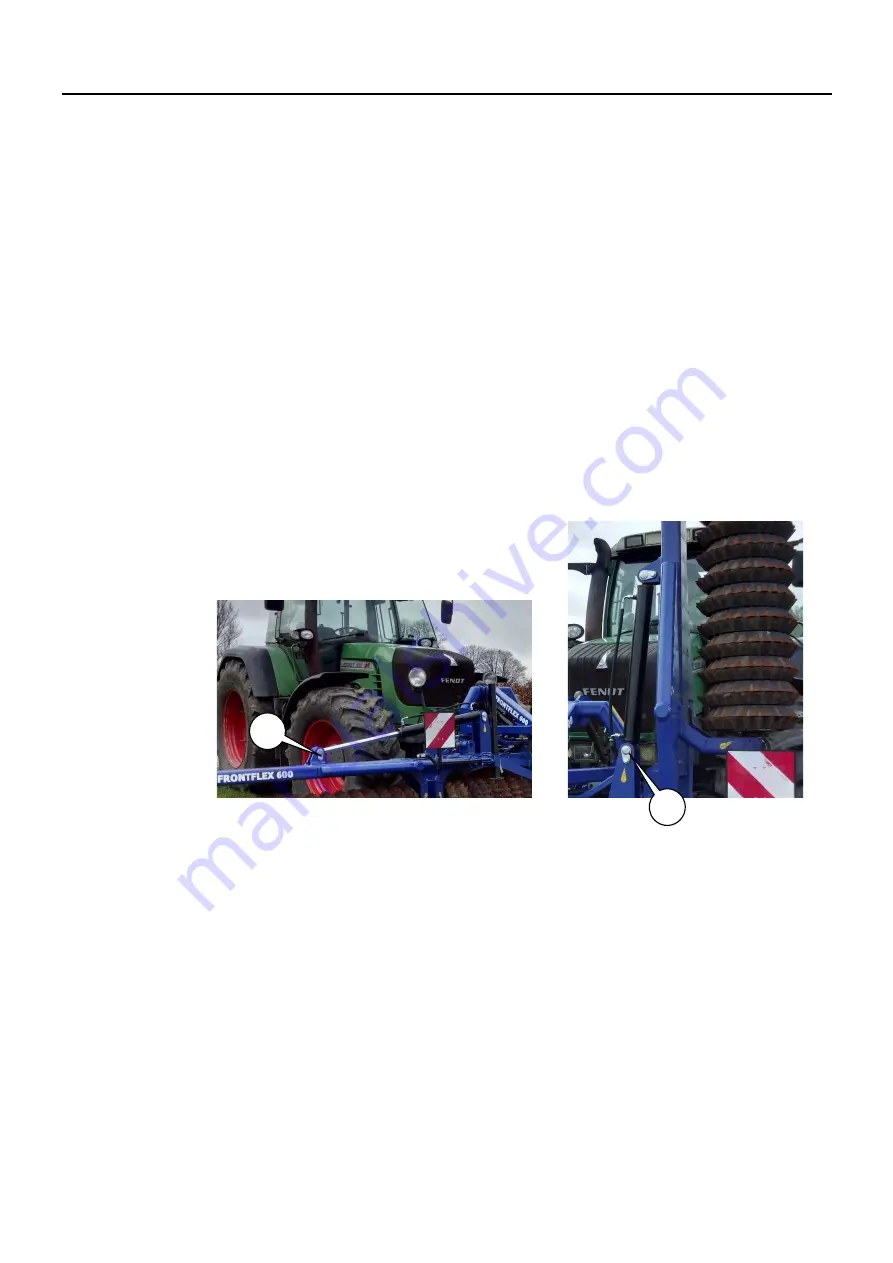
FRONTFLEX
Page 24
Replacing the cylinder for folding
Carry out the repair with the FRONTFLEX lowered and the side section turned downwards so
that the entire machine is resting on the ground. Remember to depressurise the hydraulic
system before disconnecting the hydraulic hoses.
1.
Loosen and remove the hoses. (If necessary, collect the oil in a tray to prevent contam-
ination of the machine and surfaces)
2.
Remove the split pins, screws and nuts from the side panel (A), as per Fig.
14.
3.
Raise the cylinder to the horizontal position.
4.
Remove the split pins, screws and nuts from the centre section (B), as per Fig.
15.
5.
The cylinder is free and can now be removed.
6.
Install the new/repaired cylinder in the reverse order.
7.
Attach the hoses.
8.
After installation, activate the cylinder and move it up and down a few times to remove
any air from the system.
Fig.
14
Fig.
15
A
B