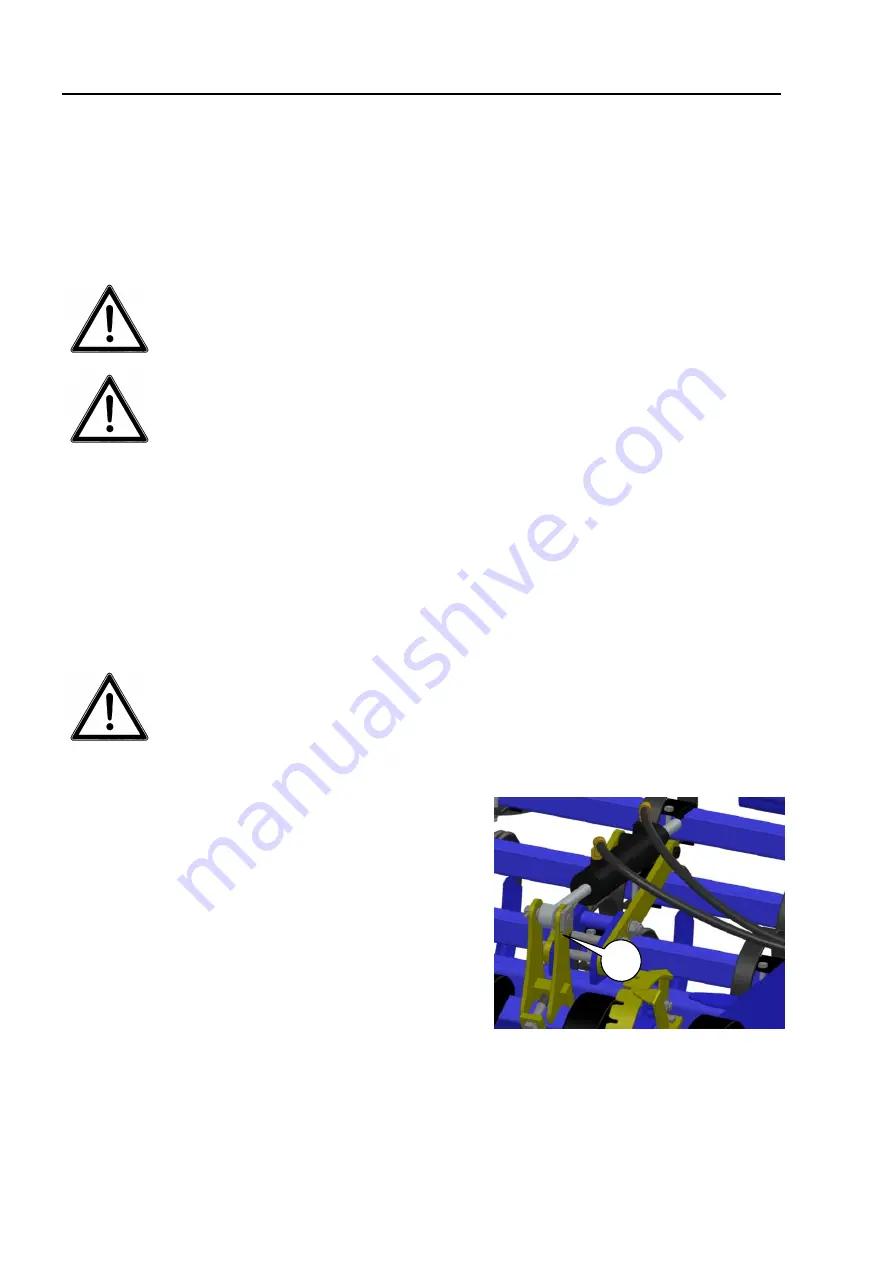
CULTITRAIL
Page 30
Replacement andrepairs
Safety is vital for all repair work. Always observe the following points, plus those
under Safety First in the instruction manual.
All maintenance and repair work can only be performed when the machine is low-
ered to the ground, the tractor is braked, engine stopped and ignition key re-
moved to prevent accidental start.
Particular attention must be paid to safety when repairing hydraulics. Depressu-
rise the hydraulic system before starting work.
When replacing cylinders, always fill new cylinder with oil before pressurising sys-
tem. We recommend fitting cylinder to frame first, fill with oil, before completing
fitting at top.
Hydrauliccylinders
Hydraulic cylinder replacement
The machine must be fully extended and standing on ground for repairs. If a wheel
cylinder is to be replaced for example, bring the wheels to a position in which the
wheel rests on the ground. Depressurise the cylinder by putting the tractor's hy-
draulic handle in the flow position.
1.
Depressurise cylinders. Discon-
nect hoses.
2.
Remove split pins and pins. Cylin-
der will now be free.
3.
Fit new or repaired cylinder. Check
pin locks into the pin stop (A), se-
cure pins with split pins.
4.
Connect hoses. Check there is no
danger of hoses being ripped or
crimped after fitting.
A
Summary of Contents for CULTITRAIL 500
Page 1: ...CULTITRAIL EN 500 600 cm Serial no 00100 XXXX ...
Page 2: ......