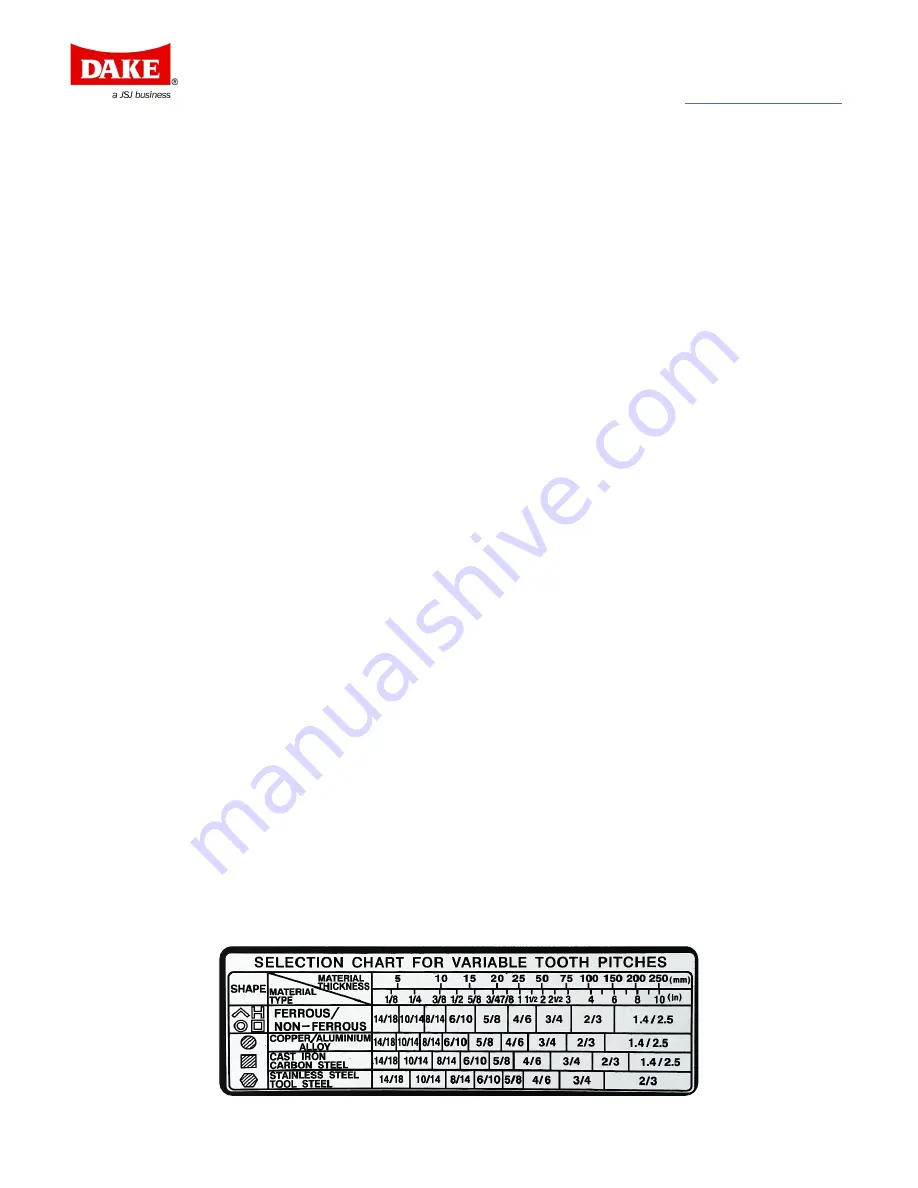
Dake Corporation
724 Robbins Road
Grand Haven, MI 49417
www.dakecorp.com
7
REV022019
SET UP
ASSEMBLY
Motor Pulley Cover: (Items 290, 291, 293, 294, & 343)
1) Open the cover and slide the bottoms openings around the pulleys.
2) Line up the holes in the motor pulley case with the hole in the bracket coming up from the
motor mount bracket.
3) Use the washers and hex screws to attach the cover to the bracket in the center and
righthand side of the cover.
4) Close cover and snap lower fastener closed, then use the washer and round head screw
to keep it securely closed.
Wheels: (Items 94-96)
1) Take the wheel rods and slide them though the holes at the bottom of the saw stand. See
exploded parts view as reference.
2) Pace a wheel on each end of the rods.
3) Use a cotter pin and insert it through the hole in the end of the rod to secure the wheels.
BLADE SELECTION
An 8-tooth per inch general use blade comes installed with this metal cutting bandsaw.
Additional blades in 4, 6, 8, and 10 tooth pitches are available. However, 3 teeth should be
engaged with the workpiece at all times for proper cutting.
For maximum cutting efficiency and lowest cost per cut, it is important to select the blade with
the correct number of teeth per inch (TPI) for the material being cut. The material size and
shape dictate tooth selection.
Located on the saw is a chart to determine the tooth pitch or TPI needed for cutting various
material types and shapes.
For piping, tubing, and structural the material thickness used is the average thickness that the
blade goes through during the cut.