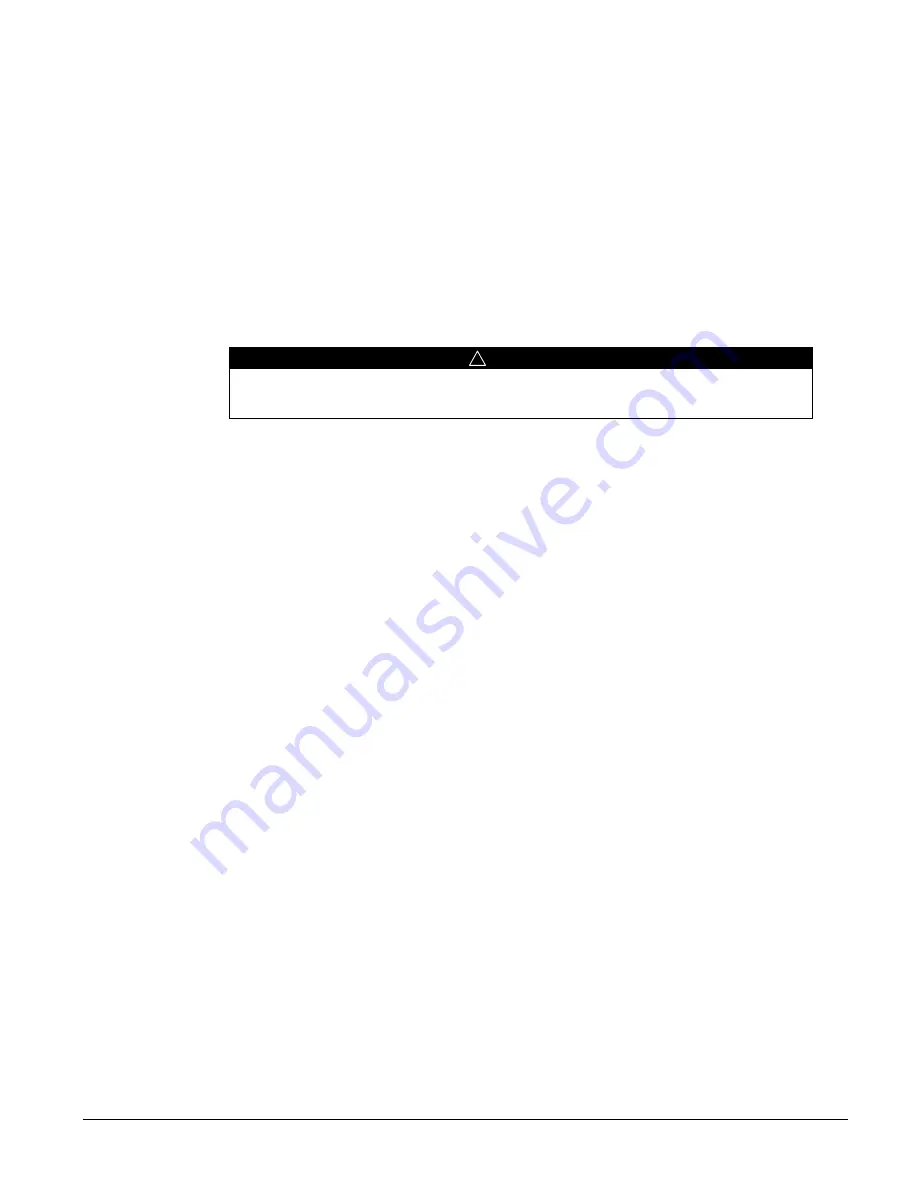
OMM WCT
Centrifugal Chillers
D-EOMWC01302-16EN - 73/84
Leak Testing
After a service repair
,
the unit must be checked for leaks prior to recharging the complete system.
This can be done by charging enough refrigerant R-134a into the system to build the pressure up to
approximately 10 psig (69 kPa) and adding sufficient dry nitrogen to
bring the
pressure up to a
maximum of 125 psig (860 kPa). Leak test with an
R-134a compatible
electronic
leak
detector to be
sure all joints are tight. Halide leak detectors do not function with R-134a.
Leak testing should be focused on the areas worked on. Leaks around tubing or fitting connections
can often be stopped by simply tightening them. However, for
any leaks that are found in welded or
brazed joints, or if it is necessary to replace a gasket, relieve the test pressure in the system before
proceeding. Brazing is required for copper joints.
After it has been determined that there are no refrigerant leaks, the system must be evacuated as
described in the following section starting from step 3 in the following Evacuation section.
WARNING
Do not use oxygen or a mixture of refrigerants and air to build up pressure as an
explosion can occur causing serious personal injury.
Evacuation of the System
If there is a need for major service work on the chiller or on the condenser for any of the circuits
and the whole charge must be evacuated then proceed as follows:
1) Connect the service valve at the bottom of the condenser to the refrigerant cylinder and start
taking charge out while running the unit at full load with high condenser water inlet temperature
until the unit shuts down on low evaporator pressure.
2) Continue taking liquid charge out after shutdown while circulating warm condenser water in the
unit to keep the condenser pressure higher than the cylinder pressure.
3) Once the pressures between the cylinder and unit equalizes, connect a recovery unit with a
capacity that will reduce the vacuum to the acceptable EPA standards.
4) An electronic or other type of micron gauge, must be connected at the farthest point from the
vacuum pump. For readings below 1000 microns, an electronic or other micron gauge must be used.
5) To improve evacuation circulate warm water not to exceed 122
F ( 50
C ) through the condenser
and evaporator tubes to thoroughly dehydrate the shells. A portable water heater can be employed as
an alternative source for hot water. A suggested method is to connect a hose between the source of
hot water under pressure and the evaporator head drain connection, out the evaporator vent
connection, into the condenser head drain and out the condenser vent back to the inlet of the water
heater.
6) The triple evacuation method may be necessary due to severe contamination of the refrigerant.
7) The system is first evacuated to approximately 500 microns. Dry nitrogen is then added to the
system to bring the pressure up to zero pounds.
8) Then the system is once again evacuated to approximately 500 microns.
9) After evacuation is completed to 500 microns, a vacuum hold test should be conducted.
10) Close the condenser service valve to the vacuum pump and hold the vacuum in the system for 4
hours. The slightest rise in pressure is an indication of either a leak to the atmosphere or the
moisture in the chiller or both. If, after 4 hours the micron gauge has not risen above 1000 microns,
the system may be considered tight.
11) If the vacuum hold test fails then do another leak test.
!