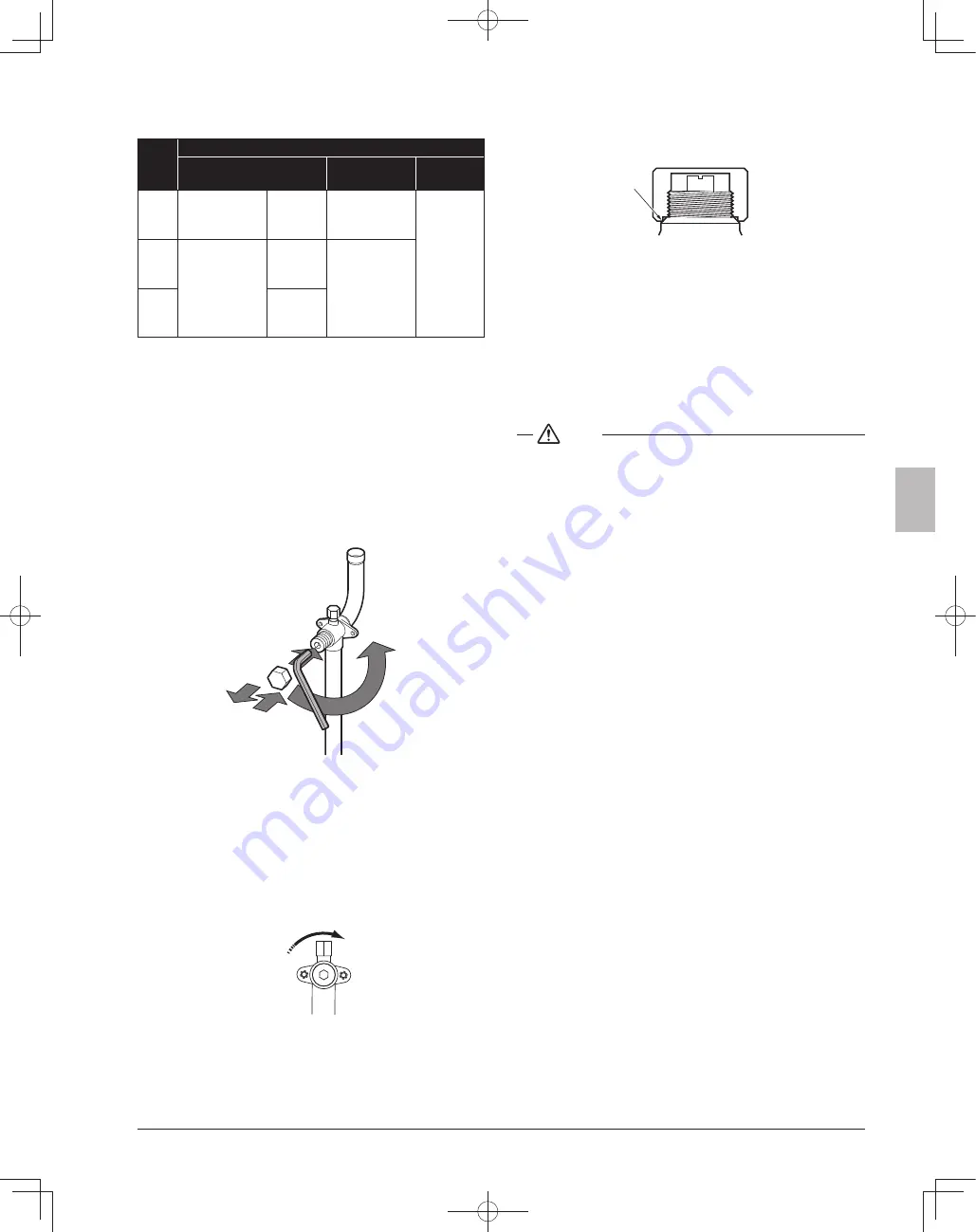
18
English
8.3.2. How to use the stop valve
Tightening torques
Stop
valve
size
Tightening torque (Turn clockwise to close)
Shaft (valve body)
Cap
(valve cover)
Service
port
f
1/2
5.97-7.30 ft
•
lbf
(8.1-9.9 N
•
m)
Hexagonal
wrench
4 mm
13.3-16.2 ft
•
lbf
(18.0-22.0 N
•
m)
8.48-10.3
ft
•
lbf
(11.5-13.9
N
•
m)
f
1
19.9-24.3 ft
•
lbf
(27.0-33.0 N
•
m)
Hexagonal
wrench
8 mm
16.6-20.3 ft
•
lbf
(22.5-27.5 N
•
m)
f
1-1/8
Hexagonal
wrench
10 mm
Opening the stop valve
1
Remove the stop valve cover.
2
Insert a hexagon wrench into the stop valve and turn the stop valve
counterclockwise.
3
When the stop valve cannot be turned any further, stop turning.
The valve is now open.
• Turn the stop valve (
f
3/8,
f
1/2) until the shaft stops.
(Opening the valve with excessive force may damage it.)
• Turn the stop valve (
f
3/4-
f
1-1/8) until the shaft stops and the
designated torque is achieved.
4
Tighten the stop valve cover securely by applying the designated
torque.
1
2
3
4
Closing the stop valve
1
Remove the stop valve cover.
2
Insert a hexagon wrench into the stop valve and turn the stop valve
clockwise.
3
Turn until the shaft stops by applying the designated torque.
The valve is now closed.
4
Tighten the stop valve cover securely by applying the designated
torque.
Closing direction
8.3.3. Cautions on handling the stop valve cover
• The stop valve cover is sealed where indicated by the arrow. Take
care not to damage it.
• After handling the stop valve, make sure to tighten the stop valve
cover securely. For the tightening torque, refer to 8.3.2. How to use
the stop valve.
• Check for refrigerant leaks after tightening the stop valve cover.
8.3.4. Cautions on handling the service port
• Always use a charge hose equipped with a valve depressor pin,
since the service port is a Schrader type valve.
• After handling the service port, make sure to tighten the service
port cover securely. For the tightening torque, refer to 8.3.2. How to
use the stop valve.
• Check for refrigerant leaks after tightening the service port cover.
9. Field wiring
NOTE
•
All field wiring and components must be installed by a licensed elec
-
trician and must comply with relevant local and national regulations.
• Be sure to use a dedicated power circuit. Never use a power supply
shared by another appliance.
• Never install a phase-advancing capacitor. As this unit is equipped
with an inverter, installing a phase-advancing capacitor will not only
deteriorate power factor improvement effect, but also may cause
capacitor abnormal heating accident due to high-frequency waves.
• Only proceed with wiring work after blocking off all power.
• Always ground wires in accordance with relevant local and national
regulations.
• This machine includes an inverter device. Connect ground and
leave charge to eliminate the impact on other devices by reducing
noise generated from the inverter device and to prevent leaked cur-
rent from being charged in the outer shell of the product.
• Do not connect the ground wire to gas pipes, sewage pipes, light-
ning rods, or telephone ground wires.
Gas pipes
can explode or catch fire if there is a gas leak.
Sewage pipes:
no grounding effect is possible if hard plastic piping
is used.
Telephone ground wires and lightning rods
are dangerous when
struck by lightning due to abnormal rise in electrical potential in the
grounding.
• This equipment can be installed with a Ground-Fault Circuit Inter-
rupter (GFCI). Although this is a recognized measure for additional
protection, with the grounding system in North America, a dedi-
cated GFCI is not necessary.
• Electrical wiring must be done in accordance with the wiring dia-
grams and the description herein.
• Do not operate until refrigerant piping work is completed. Operating the
unit before completing piping work could cause the compressor to break.
• Never remove a thermistor, sensor or similar parts when connecting
power wiring and transmission wiring.
(If operated with a thermistor, sensor or similar parts removed, the
compressor may be broken down.)
• Never connect the power supply in reverse-phase.
01_EN_03_Body_3P734038-4.indd 17
01_EN_03_Body_3P734038-4.indd 17
2023/05/29 17:14:35
2023/05/29 17:14:35