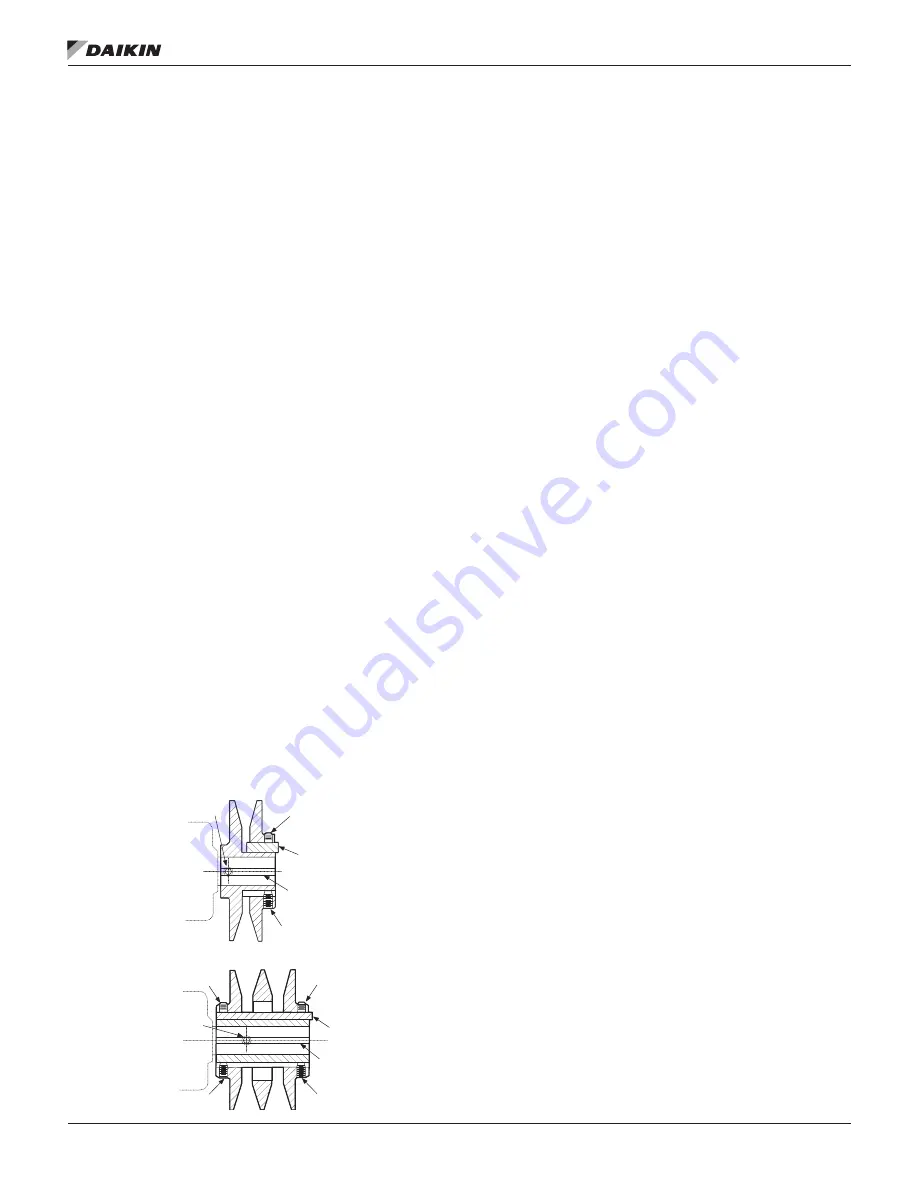
IM 777-8 • Skyline Air Handler 34 www.DaikinApplied.com
s
ervICe
and
M
aInTenanCe
VM and VP Variable Pitch Key Type
Sheaves
Mounting
1. Mount all sheaves on the motor or driving shaft with the
setscrews
A
toward the motor.
2. Verify that both driving and driven sheaves are in
alignment and that shafts are parallel.
3. Fit internal key
D
between sheave and shaft and lock
setscrew
A
securely in place.
Adjusting
1. Loosen setscrews
B
and
C
in moving parts of sheave
and pull out external key
E
. (This key projects a small
amount to provide a grip for removing.)
2. To adjust sheave pitch diameter for desired speed, open
moving parts by half or full turns from closed position.
Do
not open more than five full turns for
A
belts or six
full turns for
B
belts
.
3. Replace external key
E
and securely tighten setscrews
B
over key and setscrews
C
into keyway in fixed half of the
sheave.
4. Put on belts and adjust belt tension.
Do not force belts
over grooves .
See
See Fan Drive Belt Adjustment on
page 37
.
5. Make future adjustments by loosening the belt tension
and increasing or decreasing the pitch diameter of the
sheave by half or full turns as required. Re-adjust belt
tension before starting drive.
6. To provide the same pitch diameter, adjust both halves
of the two-groove sheaves by the same number of turns
from closed position.
7. Verify that all keys are in place and that all setscrews
are tight before starting drive. Check setscrews and belt
tension after 24 hours service.
Figure 47: VP Type Sheave Adjustment
LVP Variable Speed Sheaves
Mounting
1. Slide sheave on motor shaft so that the side of the
sheave with setscrew
A
is next to the motor when
setscrew
A
is in the hub or barrel of the sheave.
2. When setscrew
A
is at an angle in the center flange
B
,
mount it away from the motor so that the outer locking
ring and flange can be removed to get to the setscrew.
3.
To remove the flange and locking ring:
a. Loosen setscrews
D
.
b. Loosen but
do not remove
capscrews
E
.
c. Remove key
F
.
d.
Rotate the flange counterclockwise until it
disengages the threads on the sheave barrel.
NOTE:
This key projects a small amount to provide a grip for
removing.
4. Verify that the driving and driven sheaves are in
alignment and the shafts are parallel. When aligning two-
groove sheaves, allow room between the sheave and
motor to access capscrews
E
.
5. Insert key
C
between the sheave and the shaft and
tighten setscrew
A
securely.
6.
If flange and locking ring have been removed, when
replacing them make sure that the inner and outer
flanges are open from the closed position by the same
amount as the other flange. Determine this by accurately
measuring the top width of the grooves.
7. Insert key
F
.
8. Tighten setscrews
D
and capscrews
E
.
9. Put on belts and adjust belt tension.
Do not force belts
over grooves .
See
See Fan Drive Belt Adjustment on
page 37
.
10. Before starting the drive, ensure that all keys are in
place and all setscrews and all capscrews are tight.
Check and retighten all screws and retention belts after
approximately 24 hours of service.
Two Groove
C
A
B
B
D
E
C
A
D
E
D
C
Single Groove
Key "E" projects
to provide a grip
for removal.
Do not operate
sheeves with flange
projecting beyond
the hub end.