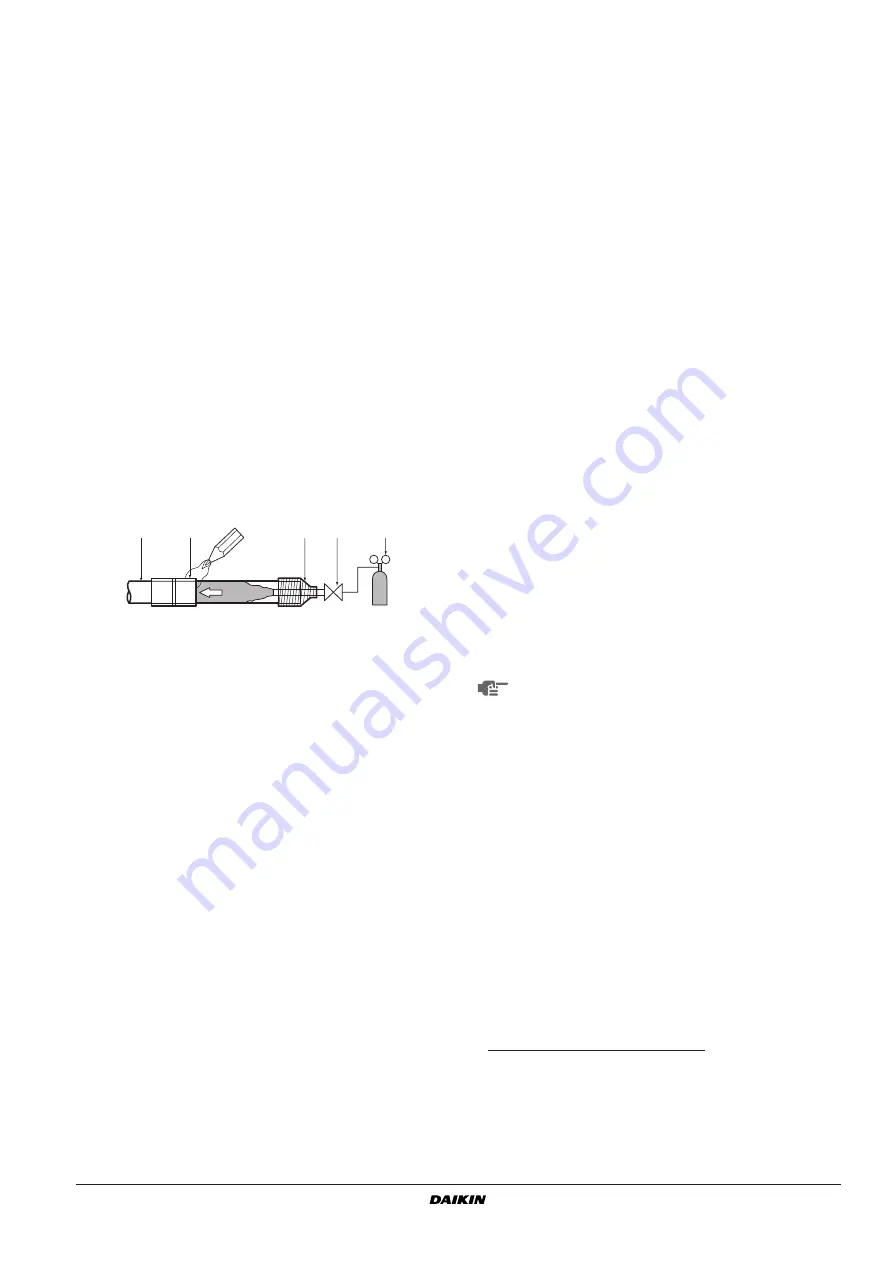
AZQS7 AZQS100~14 AZQS100~140A7W1B
Split System air conditioners
4PW68422-1 – 03.2011
Installation manual
8
Cautions for necessity of a trap
Since there is fear of the oil held inside the riser piping flowing back into
the compressor when stopped and causing liquid compression
phenomenon, or cases of deterioration of oil return, it will be necessary
to provide a trap at an appropriate place in the riser gas piping.
■
Trap installation spacing.
A
Outdoor unit
B
Indoor unit
C
Gas piping
D
Liquid piping
E
Oiltrap
H
Install trap at each difference in height of 10 m.
■
A trap is not necessary when the outdoor unit is installed in a
higher position than the indoor unit.
Cautions for brazing
■
Be sure to carry out a nitrogen blow when brazing.
Brazing without carrying out nitrogen replacement or releasing
nitrogen into the piping will create large quantities of oxidised
film on the inside of the pipes, adversely affecting valves and
compressors in the refrigerating system and preventing normal
operation. When brazing pipes however, do not use oxidation
preventers. Residue of such preventers may result in choking of
pipes or malfunction of components.
■
When brazing while inserting nitrogen into the piping, nitrogen
must be set to 0.02 MPa with a pressure-reducing valve (=just
enough so that it can be felt on the skin).
E
VACUATING
■
Do not purge the air with refrigerants. Use a vacuum pump to
vacuum the installation. No additional refrigerant is provided for
air purging.
■
Pipes inside the units were checked for leaks by the
manufacturer. The refrigerant pipes fit on site are to be checked
for leaks by the installer.
■
Confirm that the valves are firmly closed before leak test or
vacuuming.
Set up for vacuuming and leak test:
Procedure for leak test
Leak test must satisfy EN378-2.
1
Evacuate the pipes and check vacuum
(1)
. (No pressure increase
for 1 minute.)
2
Break the vacuum with a minimum of 2 bar of nitrogen. (Never
pressurize more than 4.0 MPa.)
3
Conduct leak test by applying soap water, etc. to the connecting
part of the pipes.
4
Discharge nitrogen.
5
Evacuate and check vacuum again
.
6
If the vacuum gauge no longer rises, the stop valves can be
opened.
1
Refrigerant piping
2
Part to be brazed
3
Taping
4
Hands valve
5
Pressure-reducing valve
6
Nitrogen
1
2
3
4
5
6
6
1
Pressure gauge
2
Nitrogen
3
Refrigerant
4
Weighing machine
5
Vacuum pump
6
Stop valve
(1) Use a 2-stage vacuum pump with a non return valve which
can evacuate to –100.7 kPa (5 Torr, –755 mm Hg).
Evacuate the system from the liquid and gas pipes by using
a vacuum pump for more than 2 hours and bring the system
to –100.7 kPa. After keeping the system under that condition
for more than one hour, check if the vacuum gauge rises or
not. If it rises, the system may either contain moisture inside
or have leaks.
Following should be executed if there is a possibility of
moisture remaining in the pipe (if piping work is carried out
during the raining season or over a long period of time,
rainwater may enter the pipe during work).
After evacuating the system for 2 hours, pressurize the
system to 0.05 MPa (vacuum break) with nitrogen gas and
evacuate the system again using the vacuum pump for
1 hour to –100.7 kPa (vacuum drying). If the system
cannot be evacuated to –100.7 kPa within 2 hours, repeat
the operation of vacuum break and vacuum drying. Then
after leaving the system in vacuum for 1 hour, confirm that
the vacuum gauge does not rise.
After air purging with a vacuum pump it may happen that
the refrigerant pressure does not rise, not even if the stop
valve is opened. Reason for this phenomenon is the closed
state of for instance the expansion valve in the outdoor unit
circuit, but this is not a problem for running the unit.