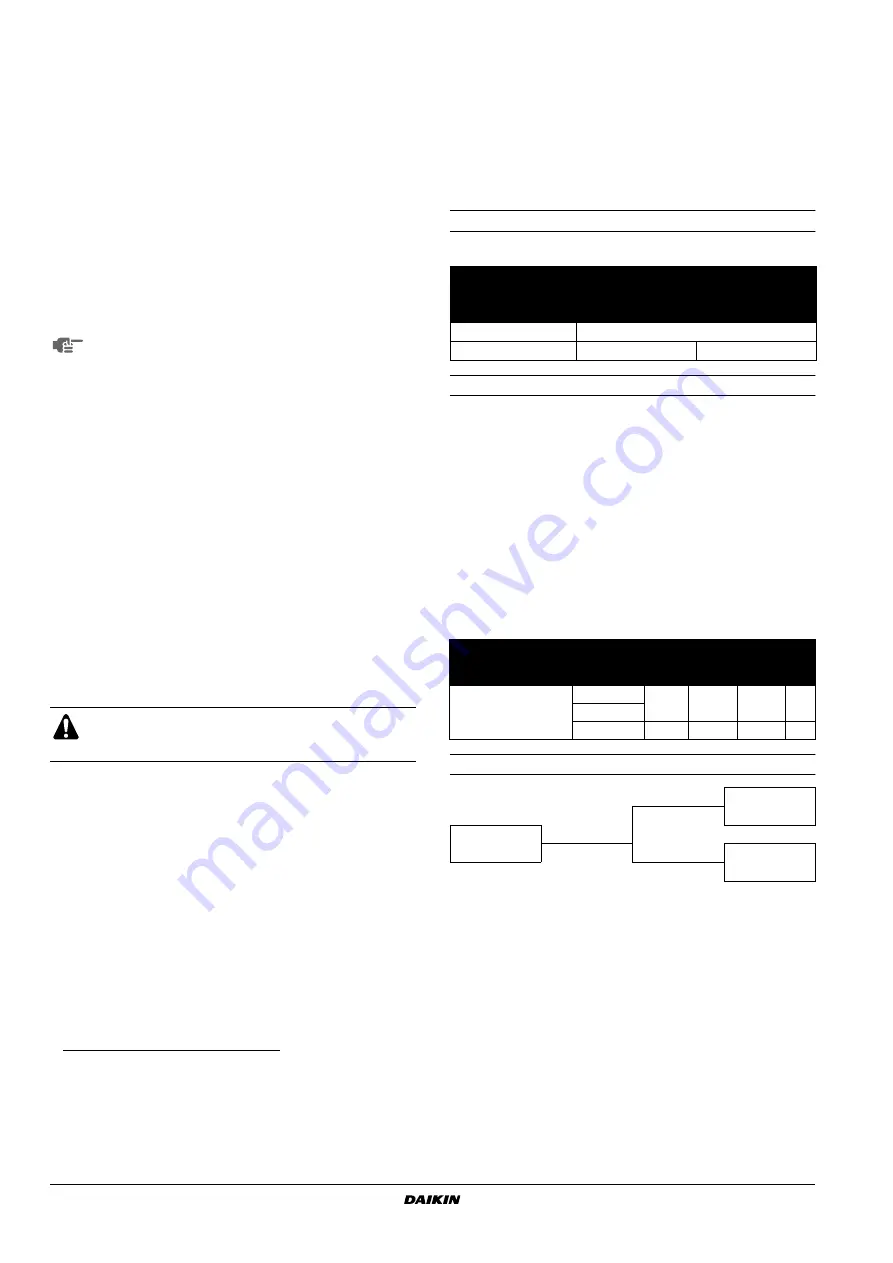
Installation manual
9
RZQS71~125B7V3
Split System air conditioners
4PW32097-1
Procedure for leak test
Leak test must satisfy EN378-2.
1
Evacuate the pipes and check vacuum
(1)
. (No pressure increase
for 1 minute.)
2
Break the vacuum with a minimum of 2 bar of nitrogen. (Never
pressurize more than 4.0 MPa.)
3
Conduct leak test by applying soap water, etc. to the connecting
part of the pipes.
4
Discharge nitrogen.
5
Evacuate and check vacuum again
6
If the vacuum gauge no longer rises, the stop valves can be
opened.
C
HARGING
REFRIGERANT
Precaution for servicing
This unit requires additional charging of refrigerant according to the
length of pipe connected at the site. Charge the refrigerant to the
liquid pipe in its liquid state through the service port of the liquid stop
valve. Since R410A is a mixed refrigerant, its composition changes if
charged in a state of gas and normal system operation would no
longer be assured.
On this model it is not necessary to charge additionaly if the piping
length
≤
30 m.
<5 m: See
"Total charging weight of the refrigerant (after a leak, etc.)"
.
Additional charging of refrigerant
■
The additional charging amounts relate to the refrigerant piping
length as in
"Maximum total one-way piping length"
in paragraph
"Allowable pipe length and height difference" on
. (E.g. twin: L1+L2+L3).
■
Over 30
m, please add refrigerant quantity according to
following table.
For future servicing, mark with a circle the selected amount on the
tables below
For pair system
Table 1: Additional charging of refrigerant <unit: kg>
For twin, triple, and double twin system
Please charge additionaly according to the following calculation.
(additional amount is R1+R2)
1.
G1: total length of
Ø
9.5 mm liquid piping
G2: total length of
Ø
6.4 mm liquid piping
2.a G1>30 m
calculate length over 30 m (=G1–30 m)
Based on this length decide R1, R2 in the table
b G1
≤
30 m and G1+G2>30 m
calculate total length over
30
m (=G1+G2–30 m)
Based on this decide R2 in the table, R1=0
3.
Total additional charge amount
R=R1+R2 (kg)
Table 2: Length <unit: m>, additional charging of refrigerant
<unit: kg>
Example 1
1
G1=L1=35 m
G2=L2+L3=7+5=12
2
Over
30
m
a
G1
–
30=5 m
➙
Ø9.5 R1=0.5 kg
b
G2=12 m
➙
Ø6.4 R2=0.6 kg
3
Refrigerant charge amount=R=R1+R2=0.5+0.6=1.1 kg
(1) Use a 2-stage vacuum pump with a non return valve which
can evacuate to –100.7 kPa (5 Torr, –755 mm Hg).
Evacuate the system from the liquid and gas pipes by using
a vacuum pump for more than 2 hours and bring the system
to –100.7 kPa. After keeping the system under that condition
for more than one hour, check if the vacuum gauge rises or
not. If it rises, the system may either contain moisture inside
or have leaks.
Following should be executed if there is a possibility of
moisture remaining in the pipe (if piping work is carried out
during the raining season or over a long period of time,
rainwater may enter the pipe during work).
After evacuating the system for 2 hours, pressurize the
system to 0.05 MPa (vacuum break) with nitrogen gas and
evacuate the system again using the vacuum pump for
1 hour to –100.7 kPa (vacuum drying). If the system
cannot be evacuated to –100.7 kPa within 2 hours, repeat
the operation of vacuum break and vacuum drying. Then
after leaving the system in vacuum for 1 hour, confirm that
the vacuum gauge does not rise.
After air purging with a vacuum pump it may happen that
the refrigerant pressure does not rise, not even if the stop
valve is opened. Reason for this phenomenon is the closed
state of for instance the expansion valve in the outdoor unit
circuit, but this is not a problem for running the unit.
When performing service on the unit requiring the
refrigerant system to be opened, refrigerant must be
evacuated according to local regulations.
Standard liquid pipe size
Connected piping length is between
Model
30~40 m
40~50 m
RZQS71
—
125
0.5
1.0
Liquid piping
Ø
Length exceeding
“Chargeless length”
Model
0~10
10~20
125
Main
9.5
0.5
1.0
R1
Branch
Branch
6.4
0.3
0.6
R2
L2=7 (Ø6.4)
50 type
100 type
L1=35 (Ø9.5)
indoor
L3=5 (Ø6.4)
50 type
outdoor heat pump