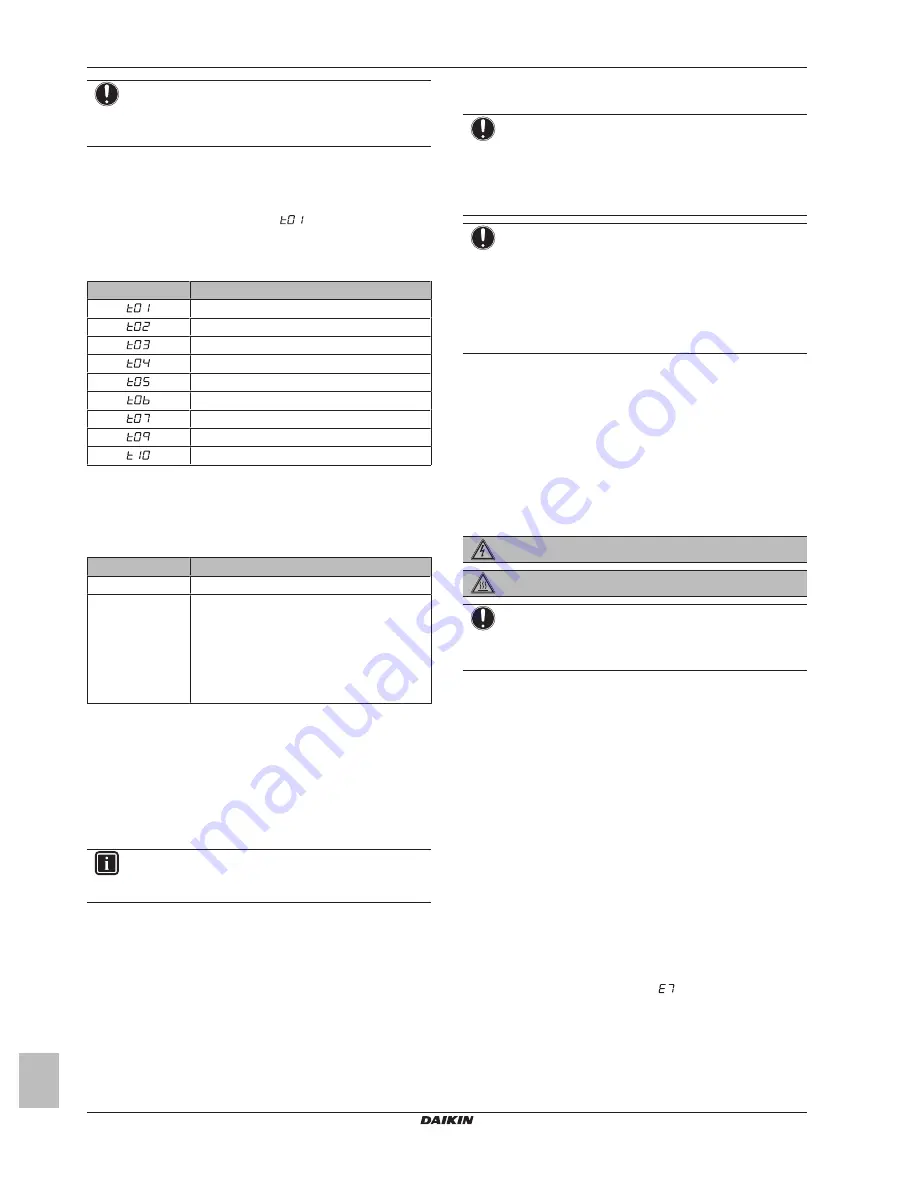
9 Maintenance and service
Installer and user reference guide
40
RXYTQ8~16T7YF
VRV IV system air conditioner
4P388989-1B – 2016.02
NOTICE
Be sure to turn on the power 6 hours before operation in
order to have power running to the crankcase heater and
to protect the compressor.
4
Make sure the default (idle) situation is existing; see
"7.2.4 To
access mode 1 or 2" on page 32
. Push BS2 for 5 seconds or
more. The unit will start test operation.
Result:
The test operation is automatically carried out, the
outdoor unit display will indicate "
" and the indication "Test
operation" and "Under centralised control" will display on the
user interface of indoor units.
Steps during the automatic system test run procedure:
Step
Description
Control before start up (pressure equalisation)
Cooling start up control
Cooling stable condition
Communication check
Stop valve check
Pipe length check
Refrigerant amount check
Pump down operation
Unit stop
Note:
During the test operation, it is not possible to stop the unit
operation from a user interface. To abort the operation, press BS3.
The unit will stop after ±30 seconds.
5
Check the test operation results on the outdoor unit 7‑segment
display.
Completion
Description
Normal completion No indication on the 7‑segment display (idle).
Abnormal
completion
Indication of malfunction code on the
7‑segment display.
Refer to
"8.6 Correcting after abnormal
completion of the test run" on page 40
to take
actions for correcting the abnormality. When
the test operation is fully completed, normal
operation will be possible after 5 minutes.
8.6
Correcting after abnormal
completion of the test run
The test operation is only completed if there is no malfunction code
displayed on the user interface or outdoor unit 7‑segment display. In
case of a displayed malfunction code, perform correcting actions as
explained in the malfunction code table. Carry out the test operation
again and confirm that the abnormality is properly corrected.
INFORMATION
Refer to the installation manual of the indoor unit for other
detailed malfunction codes related to indoor units.
8.7
Operating the unit
Once the unit is installed and test operation of outdoor unit and
indoor units is finished, the operation of the system can start.
For operating the indoor unit, the user interface of the indoor unit
should be switched ON. Refer to the indoor unit operation manual for
more details.
9
Maintenance and service
NOTICE
Maintenance must be done by an authorised installer or
service agent.
We recommend to do maintenance at least once a year.
However, applicable legislation might require shorter
maintenance intervals.
NOTICE
In Europe, the
greenhouse gas emissions
of the total
refrigerant charge in the system (expressed as tonnes
CO
2
-equivalent) is used to determine the maintenance
intervals. Follow the applicable legislation.
Formula to calculate the greenhouse gas emissions:
GWP value of the refrigerant × Total refrigerant charge [in
kg] / 1000
9.1
Overview: Maintenance and
service
This chapter contains information about:
▪ Preventing electrical hazards when maintaining and servicing the
system
▪ The refrigerant recovery operation
9.2
Maintenance safety precautions
DANGER: RISK OF ELECTROCUTION
DANGER: RISK OF BURNING
NOTICE: Risk of electrostatic discharge
Before performing any maintenance or service work, touch
a metal part of the unit in order to eliminate static electricity
and to protect the PCB.
9.2.1
To prevent electrical hazards
When performing service to inverter equipment:
1
Do not open the electrical component box cover for 10 minutes
after the power supply is turned off.
2
Measure the voltage between terminals on the terminal block
for power supply with a tester and confirm that the power supply
is shut off. In addition, measure points as shown in the figure
below, with a tester and confirm that the voltage of the capacitor
in the main circuit is less than 50 V DC.
3
To prevent damaging the PCB, touch a non-coated metal part
to eliminate static electricity before pulling out or plugging in
connectors.
4
Pull out junction connectors X1A, X2A (X3A, X4A) for the fan
motors in the outdoor unit before starting service operation on
the inverter equipment. Be careful not to touch the live parts. (If
a fan rotates due to strong wind, it may store electricity in the
capacitor or in the main circuit and cause electric shock.)
5
After the service is finished, plug the junction connector back in.
Otherwise the malfunction code
will be displayed on the
user interface or on the outdoor unit 7‑segment display and
normal operation will not be performed.
For details refer to the wiring diagram labelled on the back of the
electrical component box cover.
Summary of Contents for RXYTQ8T7YF
Page 71: ......