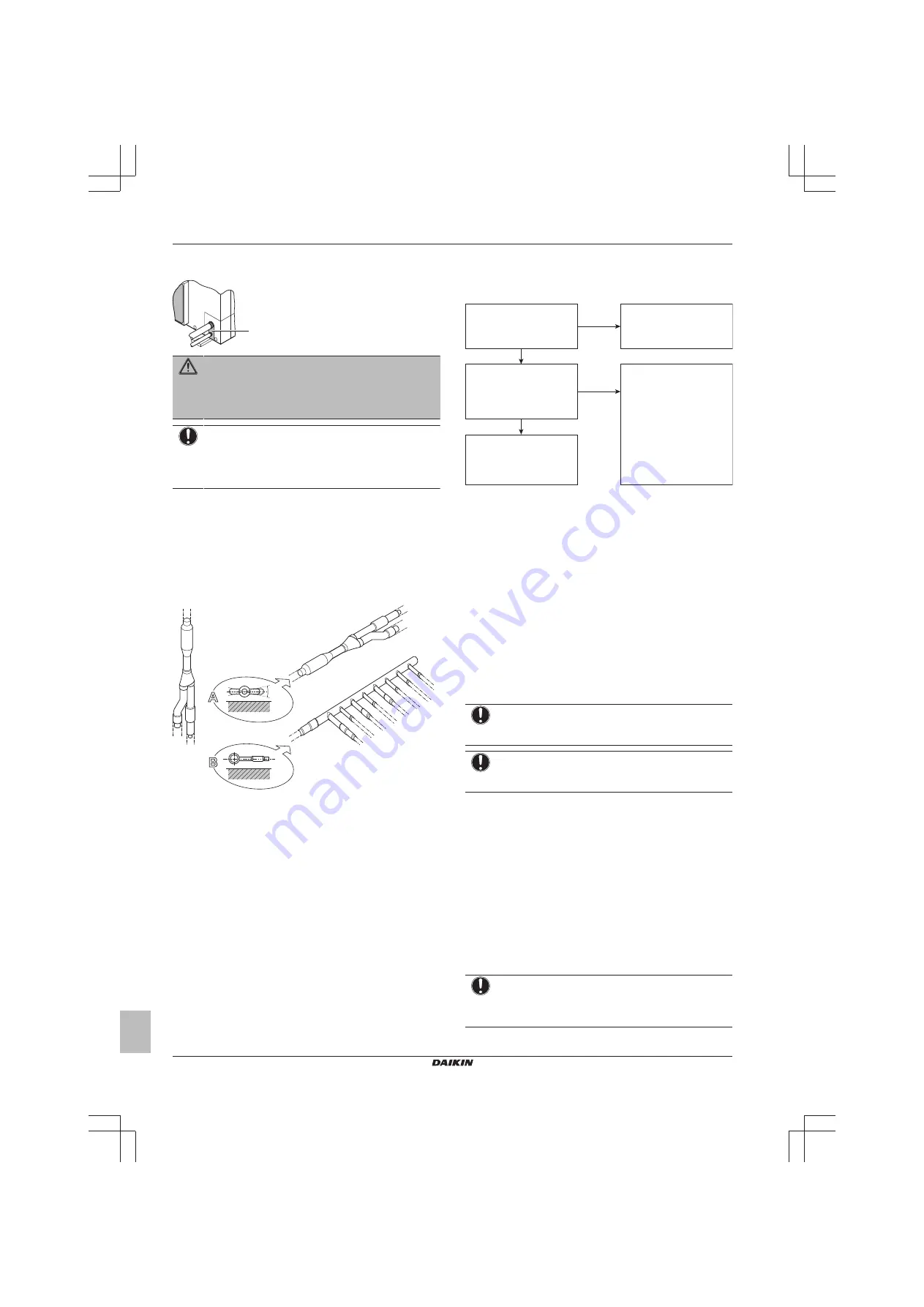
6 Installation
Installer and user reference guide
20
RXYSQ4~6TAY1B
VRV IV-S system air conditioner
4P482257-1 – 2017.03
6
Seal all gaps (example: a) to prevent snow and small animals
from entering the system.
a
WARNING
Provide adequate measures to prevent that the unit can be
used as a shelter by small animals. Small animals that
make contact with electrical parts can cause malfunctions,
smoke or fire.
NOTICE
Make sure to open the stop valves after installing the
refrigerant piping and performing vacuum drying. Running
the system with the stop valves closed may break the
compressor.
6.4.8
To connect the refrigerant branching kit
For installation of the refrigerant branching kit, refer to the installation
manual delivered with the kit.
▪ Mount the refnet joint so that it branches either horizontally or
vertically.
▪ Mount the refnet header so that it branches horizontally.
A
B
±3
0
°
a
b
c
a
a
Horizontal surface
b
Refnet joint mounted vertically
c
Refnet joint mounted horizontally
6.5
Checking the refrigerant piping
6.5.1
About checking the refrigerant piping
Refrigerant piping works are
finished?
The indoor units and/or
outdoor unit were already
powered ON?
Use procedure:
"Method 2: After power ON".
Finish piping work.
Use procedure:
"Method 1: Before power ON
(regular method)".
Yes
No
No
Yes
It is very important that all refrigerant piping work is done before the
units (outdoor or indoor) are powered on.
When the units are powered on, the expansion valves will initialise.
This means that they will close. Leak test and vacuum drying of field
piping and indoor units is impossible when this happens.
Therefore, there will be explained 2 methods for initial installation,
leak test and vacuum drying.
Method 1: Before power ON
If the system has not yet been powered on, no special action is
required to perform the leak test and the vacuum drying.
Method 2: After power ON
If the system has already been powered on, activate setting [2‑21]
(refer to
"7.2.4 To access mode 1 or 2" on page 28
). This setting
will open field expansion valves to guarantee a R410A piping
pathway and make it possible to perform the leak test and the
vacuum drying.
NOTICE
Make sure that all indoor units connected to the outdoor
unit are powered on.
NOTICE
Wait until the outdoor unit has finished the initialisation to
apply setting [2‑21].
Leak test and vacuum drying
Checking the refrigerant piping involves:
▪ Checking for any leakages in the refrigerant piping.
▪ Performing vacuum drying to remove all moisture, air or nitrogen
in the refrigerant piping.
If there is a possibility of moisture being present in the refrigerant
piping (for example, water may have entered the piping), first carry
out the vacuum drying procedure below until all moisture has been
removed.
All piping inside the unit has been factory tested for leaks.
Only field installed refrigerant piping needs to be checked.
Therefore, make sure that all the outdoor unit stop valves are firmly
closed before performing leak test or vacuum drying.
NOTICE
Make sure that all (field supplied) field piping valves are
OPEN (not outdoor unit stop valves!) before you start leak
test and vacuuming.